Cause 1 |
Chain and sprocket do not match |
Solution |
Replace the chain or sprocket with the correct size. Install a tensioner. |
Cause 2 |
Insufficient wrapping angle |
Solution |
Wrapping angle must be at least three teeth. |
Cause 3 |
Excessive load |
Solution |
Reduce the load (e.g. install a shock absorber). |
Cause 4 |
Insufficient back tension |
Solution |
Adjust catenary / take-up, install tensioners. |
Cause 5 |
Excessive chain elongation due to wear. |
Solution |
Replace with a new chain. |
Cause 6 |
Distance between the center of chain and sprocket do not match. S≠S’ |
Solution |
Inspect and adjust. |
Cause 1 |
Inadequate lubrication to the sliding portions of the pin and bush. |
Solution |
Provide adequate lubrication. |
Cause 2 |
Inadequate lubrication to the sliding portions of bush and roller. |
Solution |
Provide adequate lubrication. Use a bearing roller or plastic roller. |
Cause 3 |
Winding or riding on the sprocket. |
Solution |
See above. |
Cause 4 |
Chain casing or bearings are loose |
Solution |
Tighten all bolts and nuts. |
Cause 5 |
Chain or drive area interfering with the casing. |
Solution |
Inspect and adjust. |
Cause 6 |
Excessive chain or sprocket wear |
Solution |
Replace the chain or sprocket (replace all chains). |
Cause 7 |
Improper setting of the guide rail.
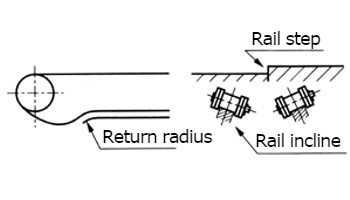 [Click to enlarge ]
|
Solution |
Inspect and adjust. |
Cause 1 |
Chain wear |
Solution |
Replace chain and sprockets at the same time. |
Cause 2 |
Insufficient number of engaged teeth |
Solution |
Increase the number of sprocket teeth. |
Cause 3 |
BF chain (no rollers) used |
Solution |
Change to RF chain (with rollers). |
Cause 4 |
Insufficient tooth hardness against wear inclusions and excessive loads |
Solution |
Use a sprocket with hardened or block replaceable teeth. |
Cause 5 |
Incompatibility between sprocket and chain |
Solution |
Replace the chain or sprocket with the correct size. |
Cause 1 |
Rusting or corrosion. |
Solution |
- ・Install a partition to protect the chain.
- ・Select a suitable chain (e.g. GS Series).
|
Cause 2 |
Conveyed material sticks between pins/bushes/plates. Or foreign matter enters. |
Solution |
- ・Install a partition to protect the chain.
- ・Select a chain with large clearance between pin, bush and roller.
- ・Remove particles or contamination, or apply penetrating oil.
|
Cause 3 |
Chain deformation due to improper installation |
Solution |
Inspect and correct the installation condition of sprocket and shaft. |
Cause 4 |
Insufficient lubrication |
Solution |
Consider lubrication or wear-resistant series (CT, BT series, etc.). |
Cause 5 |
Use in extremely high temperatures (over 400°C). |
Solution |
Provide adequate clearance. |
Cause 6 |
Seizing from excessive loads. |
Solution |
Reduce load. Lubricate regularly (e.g. install a lubricator). |
Cause 7 |
Pin bending due to excessively high loading. |
Solution |
Reduce load. Lubricate regularly (e.g. install a lubricator). |
Cause 1 |
Change the rolling friction coefficient of chain. |
Solution |
- ・Clean and lubricate moving parts with Tsubaki oil.
(・Contact a Tsubaki representative. )
- ・Replace with new sprockets.
- ・Switch to Bearing Roller Conveyor Chain.
|
Cause 2 |
Conveyor speed is too slow. |
Solution |
Increase conveyor speed. |
Cause 3 |
Insufficient rigidity in the frame. The conveyor chain is small compared to the device. |
Solution |
- ・Increase the frame rigidity, increase the chain model number.
- ・Decrease the slack in the drive chain.
|
Cause 4 |
The force of friction is excessively large. |
Solution |
- ・Lubricates between guide rail and chain to reduce frictional forces.
- ・Switch to Bearing Roller Conveyor Chain.
|
Cause 5 |
Conveyor length is too long. |
Solution |
Shorten the conveyor length by dividing the conveyor. |
Cause 6 |
Speed variation due to polygonal action |
Solution |
Number of drive sprocket teeth shall be 12T or more. |
Cause 1 |
Excessive load, too much tension on take-up. |
Solution |
- ・Eliminate the cause of overloading.
- ・Install a safety device (e.g. a Tsubaki Shock Relay).
- ・Increase chain size. (size up).
|
Cause 2 |
Reduction in strength due to wear and corrosion |
Solution |
- ・Replace with a new part. Install a cover to protect the chain.
- ・Lubricate regularly.
- ・Select a chain with the proper specs for the application.
|
Cause 3 |
Plates are pressed outward by sprocket teeth.
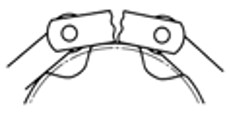 [Click to enlarge ]
|
Solution |
- ・Check and correct the installation accuracy.
- ・Check for excessively worn chain or sprocket, and replace as necessary.
- ・Check if the chain and sprocket match, and correct as necessary.
|
Cause 1 |
Roller load is excessive.
|
Solution |
Provide sufficient lubrication between the bushes and rollers. Consider bearing roller or DTA Series. |
Cause 2 |
Conveyed material/foreign objects enter between bush and roller.
|
Solution |
Clean regularly, and install a partition to protect the chain. |
Cause 3 |
Conveyed material/foreign objects accumulate on the rails.
|
Solution |
Clean regularly and install a partition to minimize accumulation. |
Cause 4 |
Lubricant adheres to the roller surface and rail without entering between bushes and rollers and between rollers and plates.
|
Solution |
Select an appropriate lubricant and lubrication method. |
Cause 5 |
Roller/bush rust.
|
Solution |
Select an appropriate specification (e.g. RT). |
Cause 6 |
Inner plate is moving sidewards.
|
Solution |
Replace with a new chain. Re-inspect the installation and load conditions. |
Cause 7 |
Bush is cracked.
|
Solution |
Reduce the load and lower the speed of rotation. |
Cause 8 |
Contact between side of roller and side of plates due to thrust load
|
Solution |
Eliminate the cause of thrust load. |
Cause 9 |
The chain and sprocket do not match, or excessively worn teeth.
|
Solution |
Check the tooth profile. |