Technical Data Top chain  Handling
These are common pages for plastic modular chains (mold-to-width type), plastic modular chains (wide type), top chains, and plastic block chains.
Installation and Inspection
1. Sprocket attachment
Installation of the sprockets is critical for smooth operation of the conveyor, and the chain life depends on the properness of the installation.
The installation should be properly carried out in accordance with the procedures described below.
1)Check the levelness of the shafts with a level.
Adjust to within a tolerance of ± 1/300 .
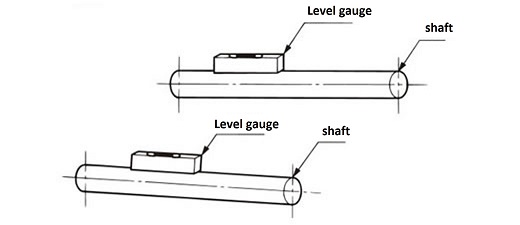
2)Check the parallelism of the shafts with a scale.
Adjust the shafts so that the parallelism as calculated with formula (A - B)/L is to within ± 1/100.
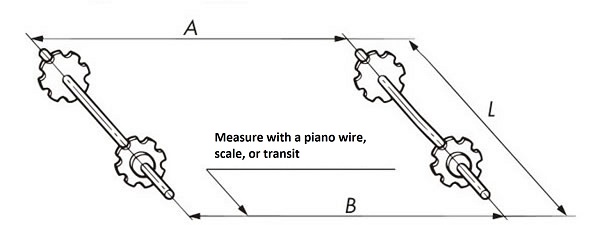
3)Align the sprocket axis to match.
- Tolerance relative to center distance up to 1 m : ±1 mm
- Tolerance relative to center distance 1 to 10 m : ± Distance between shafts (mm)1000
- Distance between shafts 10 m or longer: ±10 mm
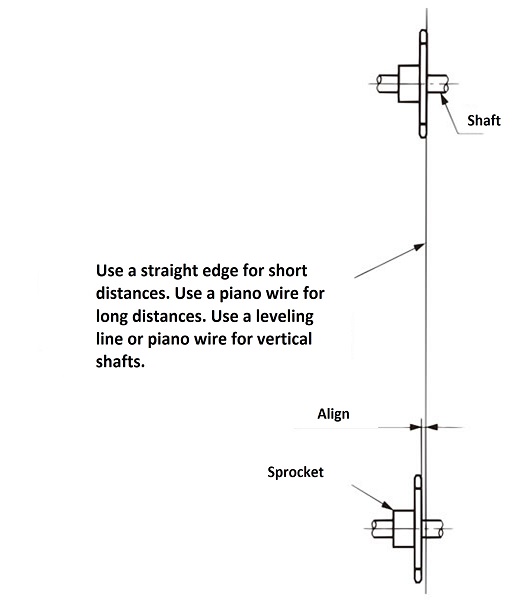
4)After the processes 1) to 3) have been completed, lock each of the sprockets to each shaft by means of keys or Tsubaki POWER-LOCK.
Lock the sprockets that are installed and used on the same shaft so that the teeth of both sprockets align in terms of phase.
2. Inspection
Frequently inspect the chain during the initial operating period in order to carry out necessary adjustment. Inspect the following items.
- 1)Unusual wear of chain
- 2)Chain Sag
- 3)Flatness of chain surface
- 4)Difference in height of top plates between appropriate plate and neighboring plate
- 5)Foreign matter between top plates and clearance between top plates
- 6)Vibration and jerking of chain
-
7)Unusual wear of sprocket, unusual contact of sprocket with other components due to eccentricity, dust accumulated on root of teeth.
When the sprocket properly engages with the chain, even contact is represented by the trace of contact shown as A in the illustration, while uneven trace of contact as B in the illustration represents improper installation of the sprocket or a twisted chain. Rechecking is needed.
The normal point of impact is slightly up from the tooth root.
However, when initial tension remains in the slacked side of the chain, the chain slightly contacts the valley. However, even in this case, strong contact should be traced around A. In the case of idlers and tighteners, contact happens at the middle of the root. - 8)Too much wear of the wearstrip
- 9)Any abnormality in the lubricating system
Causes of Vibration, Jerking, and Unusual Wear
- 1)Overload, glass fragments or bottle caps caught between components
- 2)Warping of the chain on the return-way
- 3)Insufficient lubrication or no lubrication
- 4)Interference between top plates
- 5)Wear of the sprocket
- 6)Unusual wear or breakage of the chain
3. Lubrication
Lubrication may drastically decrease elongation of the chain due to wear, wear of the sprockets and wear of the top plates and the wearstrips.
Utilization of a lubricant also reduces noise and power loss in operation.
Though plastic chains have self lubricating characteristics, lubrication exerts the same effect.
The most desirable lubricant is high-quality lubricating oil, however a lubricant prepared exclusively for this purpose or soap are often used when lubricating oil is not available.
Enough attention should be paid so that such a lubricant may be sufficiently applied to parts liable to wear such as those described above.
4. Cleaning
Chain wear dust, grease, general dust, spilled beverage syrup, etc., tend to accumulate during ordinary use, and may result in the following undesirable conditions that will require cleaning of the chain and the conveyor.
- 1)Contamination, damage, tip-over, or slippage of conveyed products
- 2)Increased load on the chain and/or the motor
- 3)Accelerated wear of sprocket teeth
- 4)Vibration and/or jerking of the conveyor
- 5)Accelerated wear in the curves and the top plates of the chain
- 6)Accelerated wear of the wearstrip
- 7)Growth of bacteria or other microorganisms
When the top chain is in operation, wear debris is normally generated.
Cleaning especially during initial operational periods should be performed because wear debris is prone to be generated more.
Method of fixing sprockets for plastic top chains
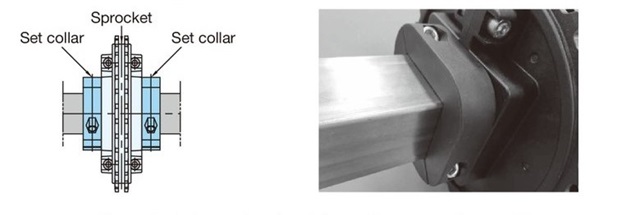
Place set collars tightly on both sides of a sprocket without leaving any clearances between them and use bolts to fix each set collar using the specified bolt tightening torque.
Method of fixing idlers
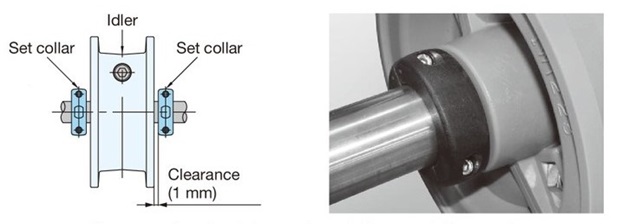
Place set collars on both sides of an idler and fix each set collars using the specified bolt tightening torque.
Ensure that there is clearance between the idler and set collar and that the idler rotates.
Refer to set collar for details.
5. Replacement of the chains, sprockets and wearstrips
5-1. Chain
Item | Inspection method | Judgment Criteria (※) | ||||||||||||||||||||||||||||||||||||||
---|---|---|---|---|---|---|---|---|---|---|---|---|---|---|---|---|---|---|---|---|---|---|---|---|---|---|---|---|---|---|---|---|---|---|---|---|---|---|---|---|
Chain elongation due to wear | Measure the length of 10 top plates by means of a measure with the chain slightly stretched to eliminate backlash through the chain links.
![]() |
Reference length = chain pitch ×10 Example: TTP chain: Result of measuring 10 links (reference length: 381 mm) Percentage of elongation and judgment when measured length was 387 mm: Percentage of elongation X = (387 - 381)÷381×100≒1.6% From table above, judgment is B. |
||||||||||||||||||||||||||||||||||||||
Wear of top plate (Plastic Top Chain and Stainless Steel Top Chain only ) |
Use a vernier caliper to measure the thickness of the part of the top plate that slides on the wearstrip. Also, verify that there are no bumps, depressions, or other irregularities measuring more than 1 mm in height or depth on the conveyor surface. |
|
||||||||||||||||||||||||||||||||||||||
Link height wear (Plastic modular chain ) |
Use a vernier caliper to measure the height of a link sliding on a wearstrip or with conveyed products.
![]() |
|
||||||||||||||||||||||||||||||||||||||
Link height wear (Plastic block chain ) |
Use a vernier caliper to measure the height of a link sliding on a wearstrip or with conveyed products.
![]() |
|
||||||||||||||||||||||||||||||||||||||
Corrosion | Check whether or not there is any place where the chain articulation is not proper due to corrosion. If corrosion should worsen, remove rust and measure the thickness of the link plate by means of a vernier caliper. |
|
||||||||||||||||||||||||||||||||||||||
Deformation of top plate | Inspect whether or not any of the following problems have happened: deformation of the top plate caused by things such as a broken bottle or bottle cap caught in the components; lifting of curled sections; looseness of a rivet in the top plate; or scratches on the upper surface of the top plate due to abnormal contact. | Replace the part if deemed that it may affect operation. For scratches on the upper surface of the top plate due to abnormal contact, investigate the wearstrip on the return-way to find the causes and repair it as necessary. |
||||||||||||||||||||||||||||||||||||||
Chipping or unsmooth rotation of the roller | Check whether or not there is any chipping of the roller and rotation is smooth. | Replace the chain and the rollers as appropriate when there is any roller that is chipped, does not rotate smoothly or is partially worn. |
A: Can be still used B: Still has margin of chain life but necessary to consider replacemen C: Chain life already expired, needs to be replaced
Note) Contact a Tsubaki representative regarding standards for link height wear for TPUN chain.
5-2. Sprocket
When the sprocket is worn as illustrated right (to the left), the chain is prone to being caught by the tips of the teeth (A), making the departure of the chain from the sprocket difficult, hence resulting in vibration of the chain.
Though wear allowance depends on the type of conveyor and the size of the chain to a certain extent, if the sprocket is replaced when the wear reaches 1.5 to 2 mm, damage to the chain can be avoided.
When the sprocket is worn in the direction of the face width as illustrated right (to the right), the shaft may not be properly aligned, therefore correct it.
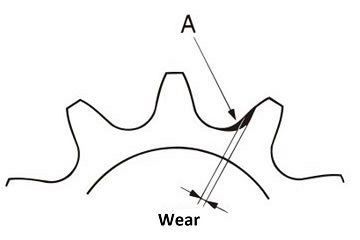
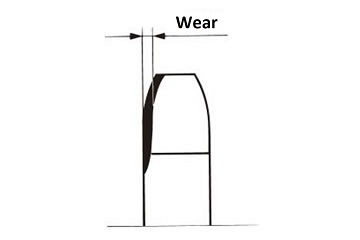
5-3. Rail
Replace the wearstrip when the thickness has been reduced to half of the original thickness.