Technical Data Top chain  Selection
This page introduces the following items.
Click on each item to scroll to the main text.
- 2-1. Wearstrip arrangement
- 2-2. Guide Clearance
- 2-3. Example of wearstrip installation (at ambient temperature)
- 2-4. Conveyor Layout
- 2-5. WT0700 series with nose bars at both ends
- 2-6. WT1500 series and BTN5 with nose bars at both ends
- 2-7. Layout of forward/reverse bottom drive for WT2520 series
- 2-8. Layout of Abutting Nose Bars
- 2-9. Layout of Abutting BTC4-M Chains
- 2-10. In-line layout of WT2520 series
- 2-11. Layout of Right-Angle Transfers
- 2-12. Right-Angle Transfer with WT1500 and WT1505G
- 2-13. Take-up for inclined conveyors
- 2-14. Return-way in flight type chain
- 2-15. Special formation of float-preventive attachments (tabs)
- 2-16. Installation of transfer plate
Plastic modular chain (Wide type) Conveyor Design
2-1. Wearstrip arrangement
Wearstrip arrangement depends on the installation space and other factors. An example is shown in the figure below. (High load application)
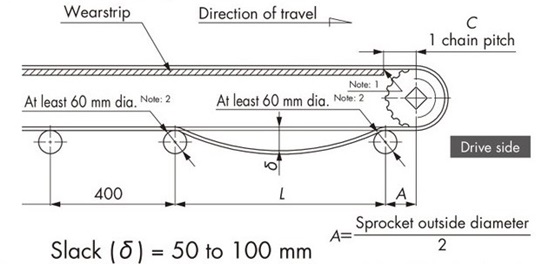
Note)
- 1. The wearstrips and conveyor flame near the drive end should be chamfered to prevent chain from interference.
- 2. Return rollers having an 80 mm diameter or more should be used for WT1907, WT3827 and WT5707.
- 3. Return rollers having an 20 mm diameter or more should be used for WT0705-W, WT1515-W, WT1516-W, WT0705-M, WT1515G-M and BTC4-M.
2-1-1. Chain slack
Table 5 shows the spacing L between return rollers supporting the chain on the return-way near the drive sprocket. The amount of the slack of the chain between these rollers should be 50 to 100 mm, or the chain may result in skipping. The slack prevents the chain skipping.
Table 5. Return roller spacing L
Chain Type | Return roller spacing L | |
---|---|---|
chain tension rate (F1) | ||
50% or less | More than 50% | |
WT0405, WT0705 | 400 ~ 600 | |
BT6, BT8 | 500 ~ 700 | 800 ~ 1000 |
WT2250, BTC8S, WT2515, WT2525, WT2525VG | 600 ~ 900 | |
WT1500, 2500, 3000, 3800 | 450 ~ 500 | |
WT3109, BTH16 | 750 ~ 1000 |
WT1907, WT3827, WT3835, WT5707
Conveying conditions | Return roller spacing L |
---|---|
Length of conveyor: Less than 12 m/conveyed mass: 75 kg/m2 or less | 600 ~ 900 |
Length of conveyor: Less than 20 m/conveyed mass: 100 kg/m2 or less | 750 ~ 900 |
Length of conveyor: Less than 20 m/conveyed mass: exceeds 100 kg/m2 | 1200 ~ 1500 |
Note)
- 1. Design with mold to width is same as plastic top chain.
- 2. For pasteurizers and other special conveyors, contact a Tsubaki representative.
- 3. Refer to the nose bars are mounted on both ends.
WT0705-W, WT1515/6-W, WT0705-M, WT1515G-M, BTC4-M
Return roller | Recommended chain width | Return roller spacing |
---|---|---|
TP-RR20650 | 300mm or less | 400mm |
TP-RR30850 | 500mm or less | 400 ~ 600mm |
TP-RR41050 | 600mm or less |
2-1-2. Engagement angle
The engagement angle of the chain on the drive sprocket should be at least 180°Note) . If the engagement angle is too small, chain skipping may occur.
Note) The engagement angle of bottom power drive should be 200° or more.
2-1-3. Wearstrip ends
A distance C, between the center of the sprocket and the end of the wearstrip, basically should be one pitch of the chain.
In addition, the end of the wearstrip faced to driven side should be rounded or chamfered downward in order to prevent the chain from snagging or catching on the wearstrip.
2-1-4. Location of sprockets and wearstrips
See illustration below.
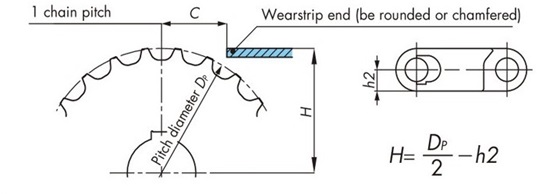
Note) For WT3109-W and BTH16, contact a Tsubaki representative.
Table 6. Backbend radius
Chain Type | Backbend radius R mm |
|
---|---|---|
Wide type | WT0405-W | 5 |
WT0705-W | 10 | |
BTN5, WT1505-K, WT1505RN-K, WT1505G-K, WT1505GTO-K, WT1505GTORN-K, WT1506-K, WT1515-W, WT1515G-W, WT1515VG-W, WT1516-W, WT1515G-M, BTC6, BTC6RN, BTC6-T, BTC6RN-T, BTO6, BTO6RN, BTN6 |
15 | |
WT1907-K | 90 | |
BTC8, BTM8H, WT2250-W, WT2525-K, BTC8S, WT2515-W, WT2515G-W |
25 | |
WT2505-K, WT2506-K, WT2706-K, WTU3015T-K |
20 | |
WT2525VG-K, WT2705-K, WT3005-K, WT3005G-K, WT3086-K, WT3086G-K |
30 | |
WT3109-W | 35 | |
WT3816-K, WT3835-K | 40 | |
WT3827-K | 50 | |
BTH16 | 60 | |
WT5707-K | 70 | |
Mold-to-Width type | BTC4-M, WT0705-M | 10 |
WT1505G-M, WT1505GTO-M, WT1505TOD-M, WT1515G-M |
15 | |
BTO8-M, WT2505-M, WT2505G-M, WT2505TOD-M, WTM2535G-M |
20 | |
BTC8H-M, BTM8H-M, WT2515G-M, WT2525-M |
25 | |
WT2525VG-M, WT3005G-M, WT3086G-M, WT3085-C325 |
30 | |
WT3835G-M | 40 |
Note) For flight types, this varies depending on flight formation and height.
2-2. Guide Clearance
Leave a clearance between the chain and the wearstrip (guide clearance) as indicated below to allow for thermal expansion.
Conveyor guide width (G) = Chain width (X) + Guide Clearance (Gc)
Table 7. Guide Clearance Gc
Chain width mm | Temperature ℃ | ||
---|---|---|---|
-20 ~ 40 | 40 ~ 60 | 60 ~ 80 | |
300 or less | 5.0 | 6.0 | 7.0 |
300 to 500 | 6.0 | 7.0 | 9.0 |
500 to 1,000 | 8.0 | 11.0 | 15.0 |
1,000 to 1,500 | 11.0 | 15.0 | 21.0 |
1,500 to 2,000 | 14.0 | 20.0 | 28.0 |
2,000 to 2,500 | 17.0 | 24.0 | 34.0 |
2,500 to 3,000 | 19.0 | 27.0 | 40.0 |
Note) Coefficient of linear expansion of polyacetal chain :12 × 10-5/℃
2-3. Example of wearstrip installation (at ambient temperature)
2-3-1. Wide types (without tab guide attachments)
Wearstrips should be located at equal intervals alternating with sprockets.
Wearstrip spacing are as follows; WT0400 series: 45 mm/WT0700 series and WT1510 series: 50 mm/WT1907 series: 50.8 mm/BTN5: 76 mm/BT6, BT8, WT1500 series, WT3005, WT3835, BT8S, WT2500 series: 76.2 mm (wearstrip width: 25 mm)/WT3086, WT2515 and WT2250: 85 mm/WT3816: 100 mm (wearstrip width: 30 mm)/WT3827 and WT5707: 152.4 mm
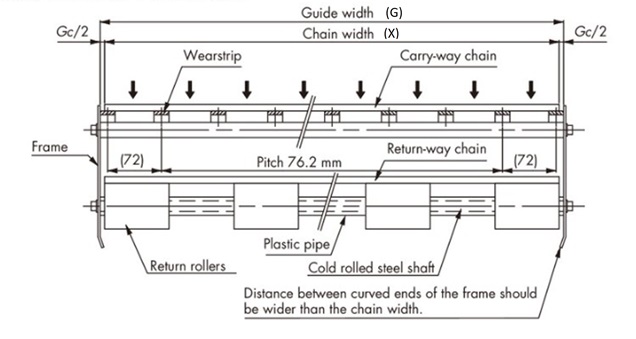
2-3-2. Wide types (with tab guide attachments)
(Chains with tab guide attachments :BTN5-A、WT1505G-K、WT1515G-W、WT1505GTO-K、WT1505GTORN-K、WT2515G-W、WT3005G-K、WT3086G-K、BTC8-A)
Tab guide attachments (to prevent meandering) should be installed so as not to interfere with the wearstrip.
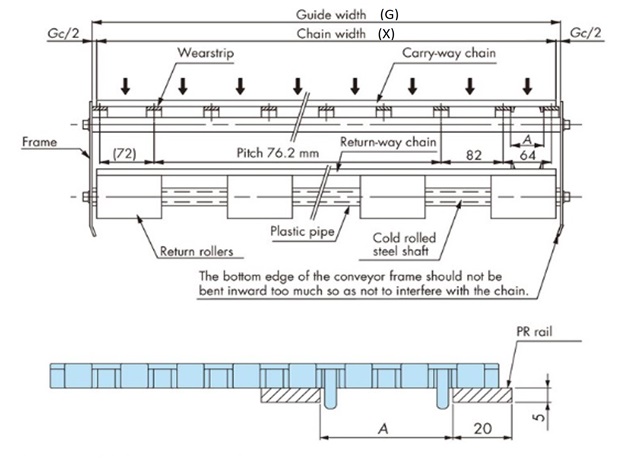
Table 8. A Dimensions [Wide Types (with Tab Guide Attachments)
Chain Type | A |
---|---|
WT1505G-K | 44 |
WT1505GTO-K, WT1505GTORN-K | 47 |
BTN5-A | 44 |
WT2515G-W | 45 |
BTC8-A | 44 |
WT3005G-K | 44 |
WT3086G-K | 44 |
WT1515G-W | 31 |
2-3-3. Wide type (WT0405-W)
In case of a multi strand application, do not make contact with the sides of adjacent strands each other. Refer to the following drawing.
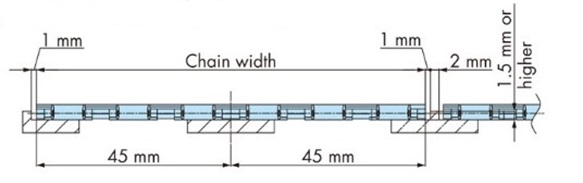
2-3-4. Wide type (WTU3015T-K)
・Layout in straight section
Wearstrips should be located at equal intervals alternating with sprockets.
1) Example of wearstrip installation
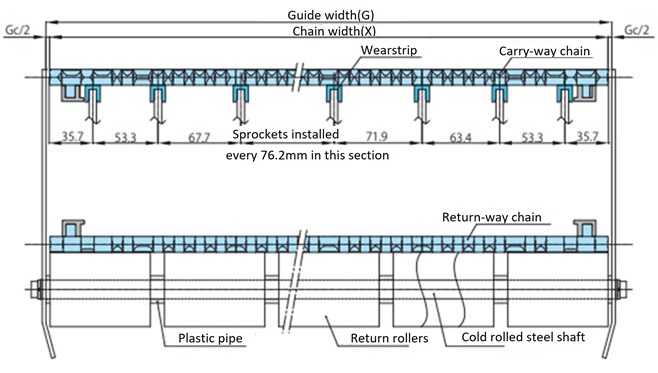
3) Layout of side transfer (lap)
When side transfering in a straight section, install the wearstrip along the side of the upstream chain's float-preventive attachment (tab).
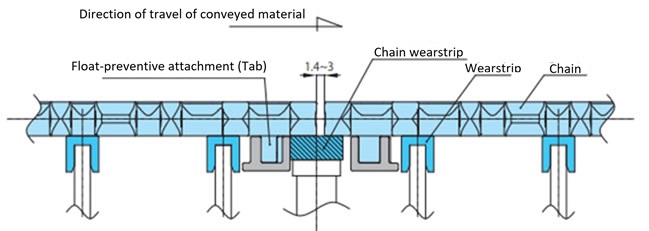
2) Layout of drive side straight section
Install a chain wearstrip on the OUT side of the straight section on the drive side of a conveyor with a curved section.
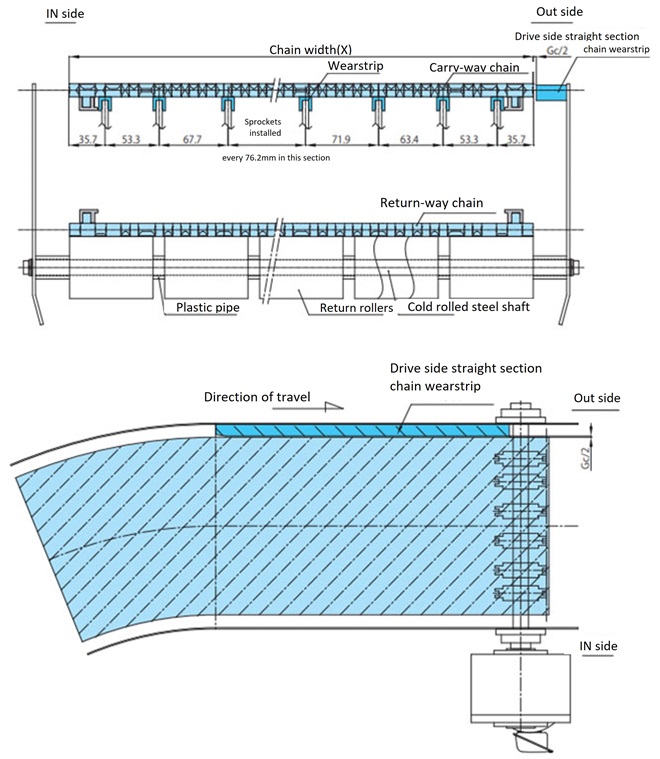
2-3-5. Wide type (for WT3109-W/BTH16)
An example is shown below for reference. Instead of fixing the wearstrip completely to the frame with bolts, provide a clearance with spacers to prevent the plastic rail from floating due to thermal expansion differences.
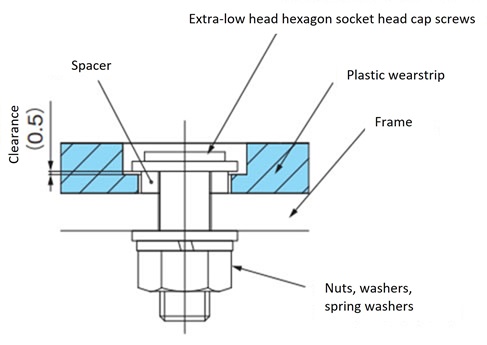
2-3-6. Mold-to-width type (with tab guide attachments)
Refer to the table below for guide clearance for chains with tab guide attachments. Leave a clearance of around 1 mm between chains when used in multi-strand conveyors.
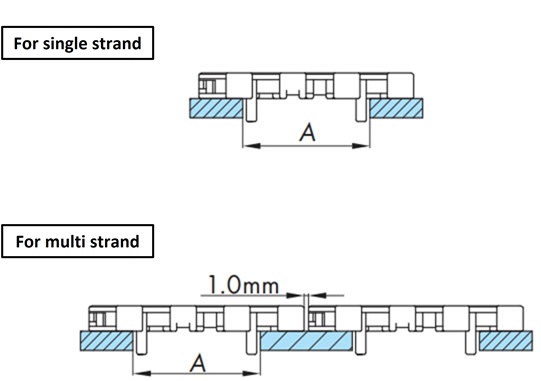
Table 9. A Dimensions (Mold-to-Width Type with Tab Guide Attachments)
Chain Type | A |
---|---|
WT1505G-M | 44 |
WT1505GTO-M | 47 |
WT1505TOD | 53 |
WT1515G-M50 | 31 |
WT1515G-M100 | 61 |
WT2505G-M | 45 |
WT2505TOD | 45 |
WT2515G-M | 45 |
WTM2535G-M | 44 |
WT3005G-M | 44 |
WT3086G-M | 44 |
WT3835G-M | 45 |
BTO8-M | 44 |
BTC8H-M | 44 |
BTM8H-M | 44 |
2-3-7. Wearstrip installation for KV series
- ・Recommended wearstrip material is stainless steel.
- ・Secure only one end of the wearstrip to allow for thermal expansion. Also, remember to leave a clearance between wearstrips to allow for thermal expansion.
- ・Take-up must be done to compensate for slack in the chain caused by thermal expansion. Take-up adjustments should be performed after reaching operating temperature.
Lower temperatures only after loosening take-up. - ・Black wear dust will be generated. Be sure to clean on a regular basis.
2-4. Conveyor Layout
There are two methods of supporting the return-way: “support system using return rollers”, and the “support system using wearstrips”. Examples are shown below.
Precautions:
- 1. Pay particular attention to the ends when connecting conveyors using TOD chain.
- 2. The infeed section of the return wearstrip should be made with a large radius of at least R40.
- 3. Cut the chain so that the catenary section will have an appropriate amount of slack to compensate for expansion and contraction caused by temperature changes. A tensioner or similar device should be used to adjust the chain take-up.
2-4-1. Supported by return rollers
The center distance of the rollers (in the direction of the conveyor width) should be adjusted according to the width of the chain to be used.
(Conveyor side view)
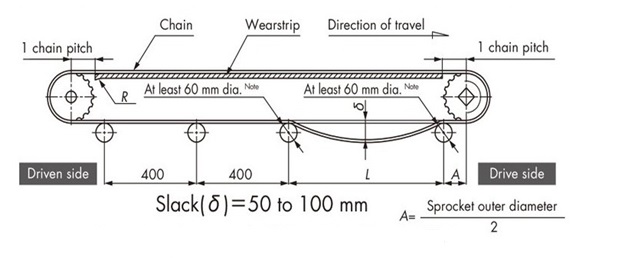
Note)
- Return rollers having an 80 mm diameter or more should be used for WT1907, WT3827 and WT5707.
Refer to the above table 5 for L dimensions.
Plan view of return-way conveyor
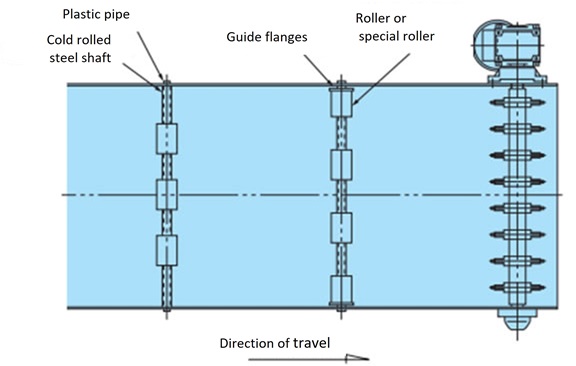
2-4-2. Support system using wearstrips
(Conveyor side view)
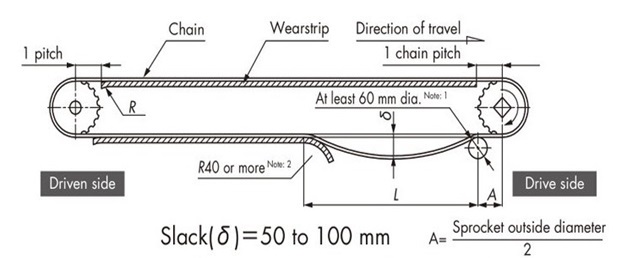
Note)
- 1. Return rollers having an 80 mm diameter or more should be used for WT1907, WT3827 and WT5707.
- 2. Equal to its backflex radius or more for WT1907, WT3827, WT5707.
Refer to the above table 5 for L dimensions.
2-4-3. Layout in curved section (in case of WTU3015T-K)
In the case of sideflexing conveyance, provide a straight section of 800 mm or more from the drive part to the curve part to secure the catenary on the return-way.
1) Example of wearstrip installation
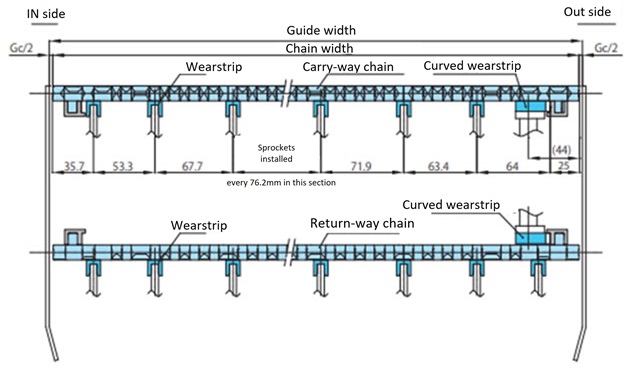
2) Processing of the entry and exit of the wearstrip
The sections where the curved wearstrip transitions to the straight wearstrip at the entry and exit should be chamfered to prevent the chain from getting caught.
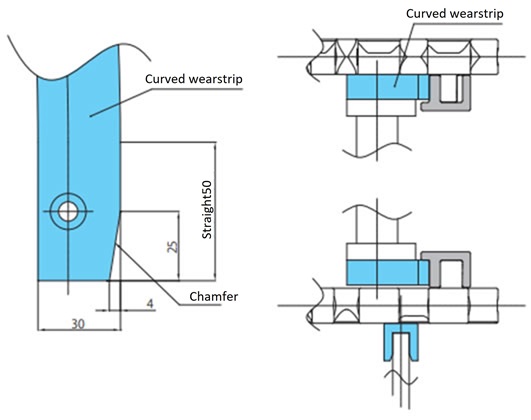
・Layout in curved section on return-way
On both ends of the curved wearstrip on return-way, install return rollers or sliding shoes (TP-C14343T-SD) 50 mm away from the wearstrip to guide the chain.
Conveyor side cross-section
2-4-4. Layout in curved section (in case of WT3085-C)
Mounting Curved Wearstrips on Carry-Way
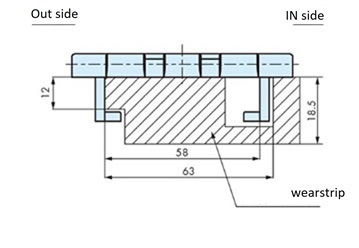
Mounting Curved Wearstrips on Returny-Way
(Attachment sliding)
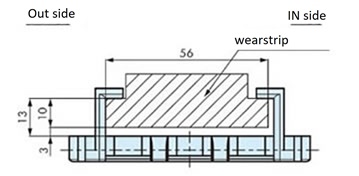
(Top plate sliding)
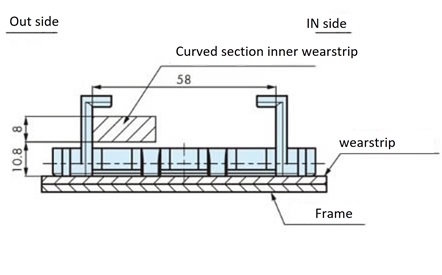
2-5. WT0700 series with nose bars at both ends
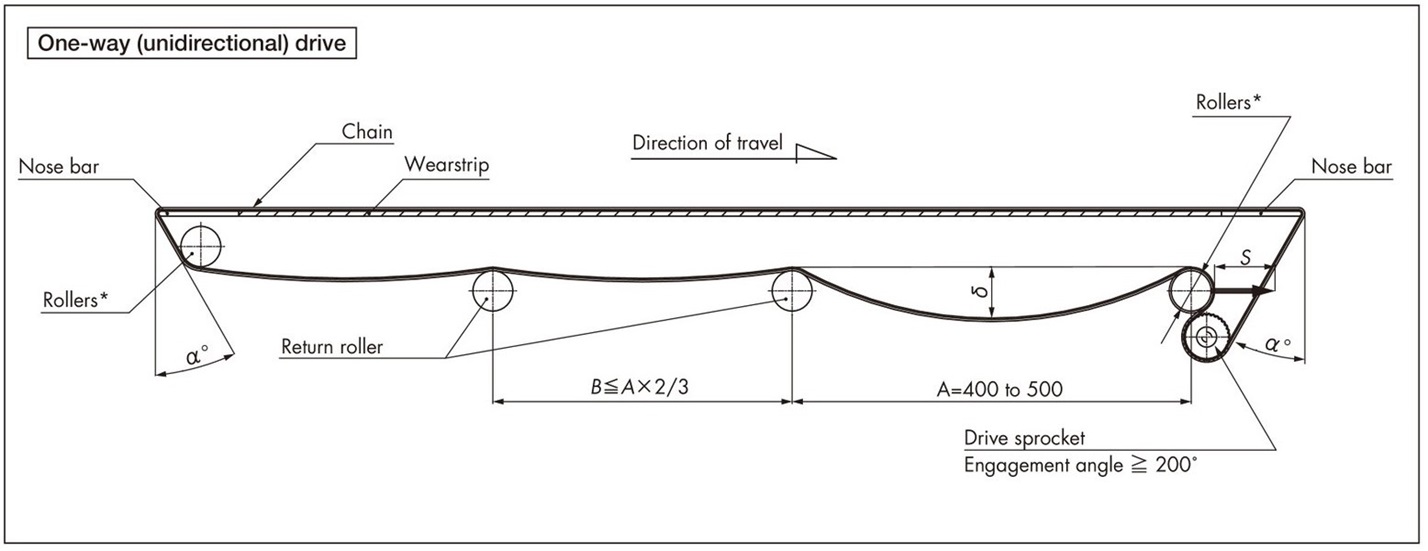
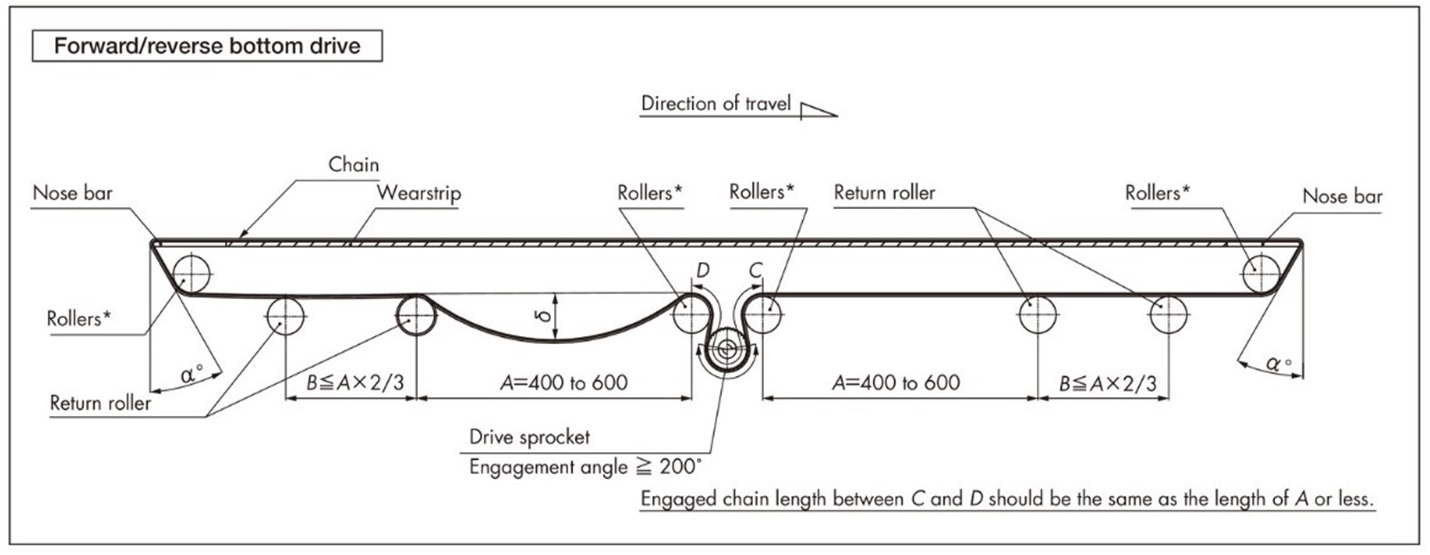
Important points regarding conveyor design
- 1. Use rollers* in the take-up system
- ・It becomes easy to take up chain stretch, cut the chain, and adjust the slack (δ).
- ・A rough guide for the take-up stroke (S) is S = conveyor length × 1%.
- 2. With regard to rollers*
- ・Select rollers that has the largest possible outside diameter (at least 50 mm).
- ・The shaft used for rollers must have adequate stiffness.
- ・The rollers should be freely rotated.
- 3. Because the chain will expand and contract due to changes in temperature, cut the chain so that an appropriate amount of slack is formed in the catenary section, or adjust using tensioners.
[Reference :Coefficient of linear expansion of polyacetal chain :12 × 10-5/℃]
- 4. In case of forward/reverse bottom drive, idler rollers receive 1.5 times higher tension load than operation tension, consider choosing more rigid shaft or supporting shaft at more than three places.
Important points when using nose bars
- 1. Nose bars must be mounted using rigid bracing. Slack must be kept within 0.5 mm.
- 2. Dimensional tolerance for bending, twisting, etc., of the frame in the direction of the conveyor width must be less than 0.3 mm.
- 3. The position and dimensions of the nose bars, rollers*, and sprockets must be set so that they form an angleα ≦ 30°.
- 4. The chain slides over the nose bar under load levels approaching the maximum working tension. Consequently, SJ-CNO (special polyamide) is recommended when running at high speeds and conveying high loading under dry conditions (no lubrication).
Note) High loading conditions have been taken into account for the design material.
2-6. WT1500 series and BTN5 with nose bars at both ends
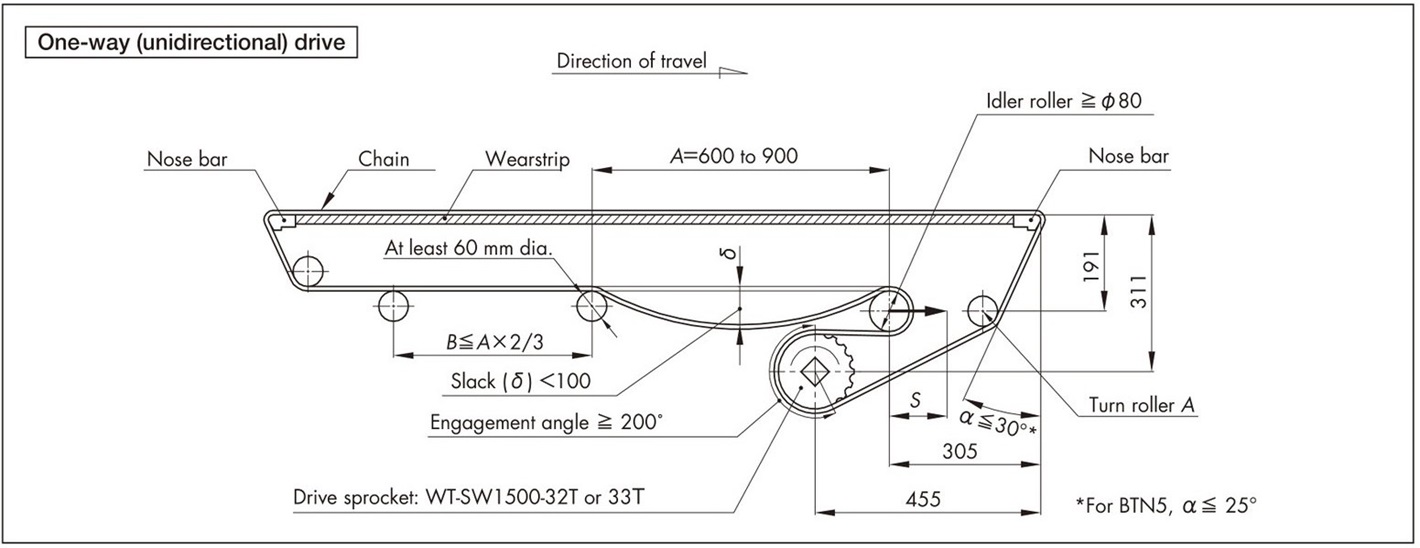
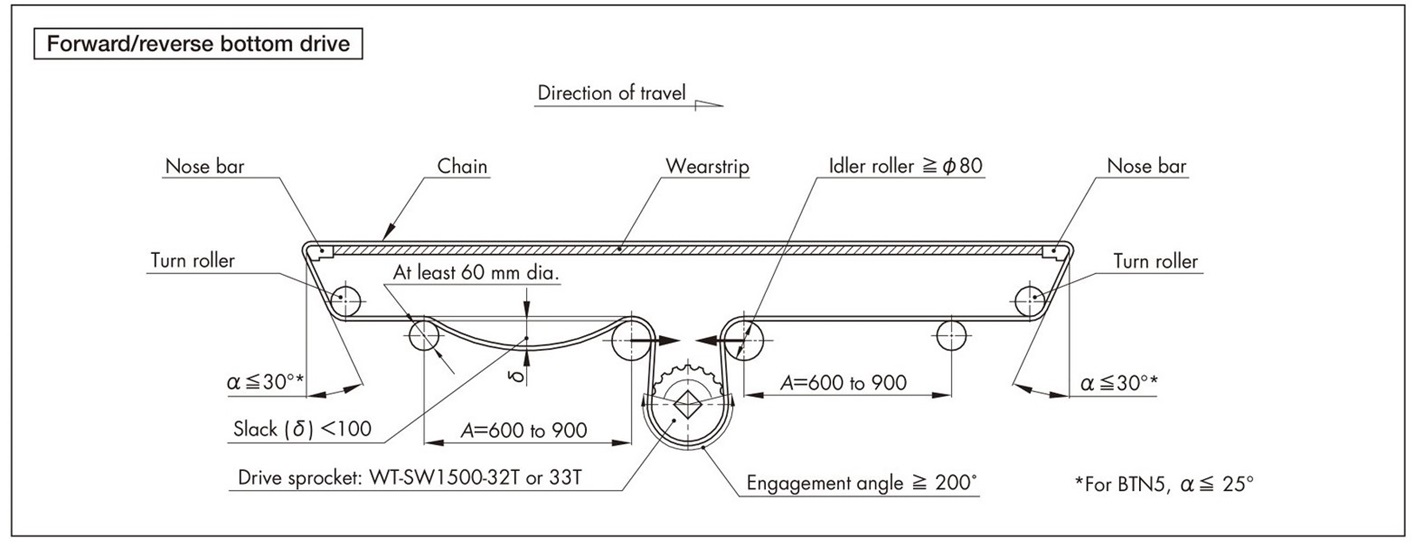
Important points regarding conveyor design
- 1. Use idler rollers in the take-up system.
- ・It becomes easy to take up chain stretch, cut the chain, and adjust the slack (δ).
- ・A rough guide for the take-up stroke (S) is S = conveyor length × 1%.
- 2. Select the idler roller that has the largest possible outside diameter (at least 80 mm diameter).
- 3. The idler roller should be freely rotated.
- 4. The shaft used for turn roller A and turn rollers must have sufficient stiffness. (Do not use high-rotation return rollers for these turn rollers.)
- 5. Because the chain will expand and contract due to changes in temperature, cut the chain so that an appropriate amount of slack is formed in the catenary section, or adjust using tensioners.
[Reference :Coefficient of linear expansion of polyacetal chain :12 × 10-5/℃]
- 6. In case of forward/reverse bottom drive, idler rollers receive 1.5 times higher tension load than operation tension, consider choosing more rigid shaft or supporting shaft at more than three places.
Important points when using nose bars
- 1. Nose bars must be mounted using rigid bracing. Slack must be kept within 0.5 mm.
- 2. Dimensional tolerance for bending, twisting, etc., of the frame in the direction of the conveyor width must be less than 0.3 mm.
- 3. The position and dimensions of the nose bars and turn rollers must be set so that they form an angle α≦ 30°.
- 4. The chain slides over the nose bar under load levels approaching the maximum working tension. Consequently, PLF or SJ-CNO (special polyamide), are recommended when running at high speeds and conveying high loading under dry conditions (no lubrication).
Note) High loading conditions have been taken into account for the design material.
2-7. Layout of forward/reverse bottom drive for WT2520 series
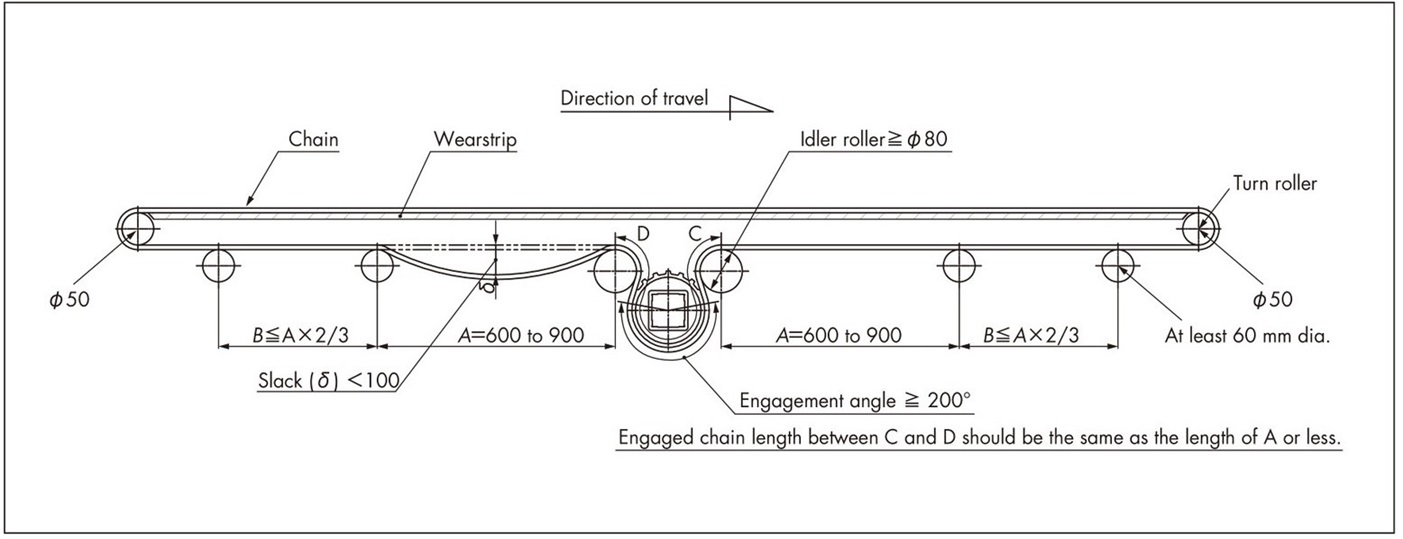
Important points regarding conveyor design
- 1. Select the idler roller that has the largest possible outside diameter (at least 80 mm diameter).
- 2. The idler roller should be freely rotated.
- 3. The shaft used for turn rollers must have sufficient stiffness. (Do not use high-rotation return rollers for these turn rollers.)
- 4. Because the chain will expand and contract due to changes in temperature, cut the chain so that an appropriate amount of slack is formed in the catenary section, or adjust using tensioners.
[Reference :Coefficient of linear expansion of polyacetal chain :12 × 10-5/℃]
- 5. In case of forward/reverse bottom drive, idler rollers receive 1.5 times higher tension load than operation tension, consider choosing more rigid shaft or supporting shaft at more than three places.
2-8. Layout of Abutting Nose Bars
2-8-1. In-line layout of WT0405-W
With a nose bar with a 2.5 mm radius, in-line transfer layout will be possible.
The gap in between can be reduced to 13 mm without mounting a dead plate, which was previously required.
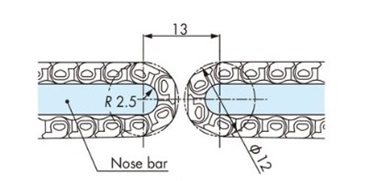
Note) Contact a Tsubaki representative for more information.
2-8-2. In-line layout of WT0700 series
・In-line layout of WT0700 series nose bar
Both conveyor ends can be adjoined in a straight line.
The use of a dead plate helps minimize space in between.
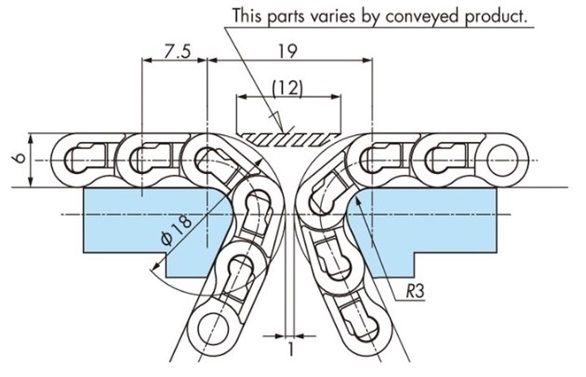
・In-line layout of WT0700 series with nose bar and sprocket
Conveyor ends and sprockets can be adjoined in a straight line.
The use of a dead plate helps minimize space in between.
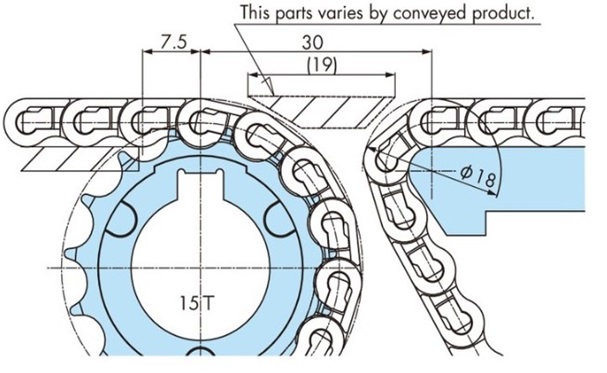
・In-line layout of WT0700 series with nose bar and WT1500 series sprocket
Conveyor ends and sprockets can be adjoined in a straight line.
The use of a dead plate helps minimize space in between.
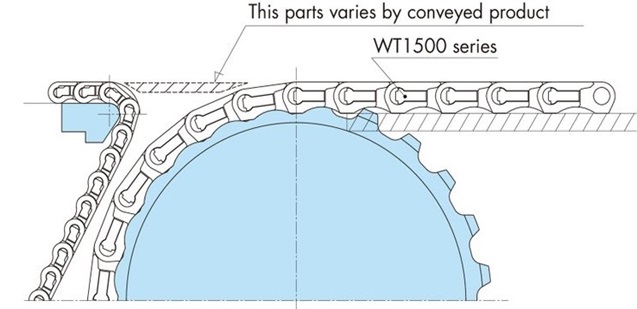
2-8-3. In-line layout of WT1500 series and BTN5
The figure below is an example layout. Mounting positions of dead plates varies depending on installation space, etc.
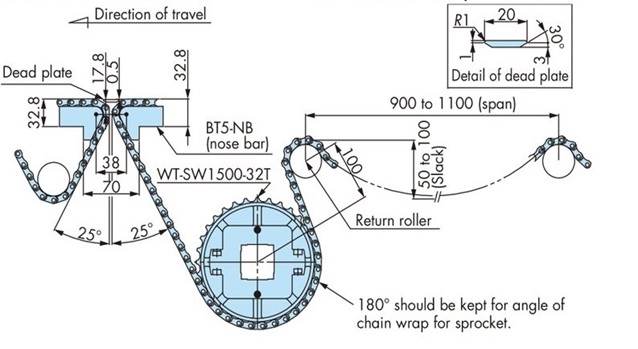
Note)
- 1. Indicated dimensions are just for information, so finely adjust them depending on transfer conditions of the conveyed products.
- 2. Even slight jerking due to the unstable shape of conveyed products may cause trouble. Contact a Tsubaki representative when such products have to be conveyed or chain jerking must be avoided.
The use of WT1500 and WT1510 series or BTN5 allows layouts in which two conveyors connect head-to-tail.
The width of the dead plate used in the space where the two conveyors abut can be as small as 20 mm.
Note)
- 1. The dead-plate gap (marked with ※ in illustration above) will need to be adjusted depending on the objects being conveyed.
- 2. Applicable chains are the WT1500, WT1510 series and BTN5 only. It should be noted that WT1505G cannot be adapted to this kind of layout.
・In-line layout of WT1500 and WT1510 series nose bar
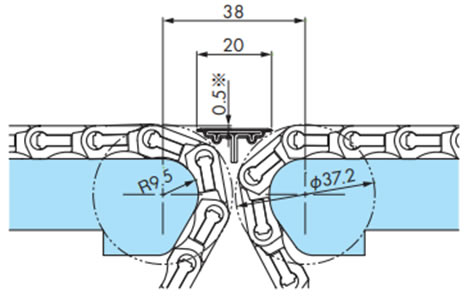
・In-line layout of WT1515VG-W
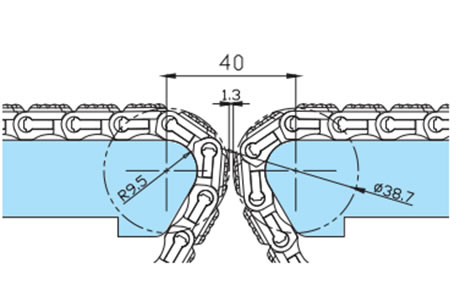
2-9. Layout of Abutting BTC4-M Chains
・For straight transfer with 10T sprockets
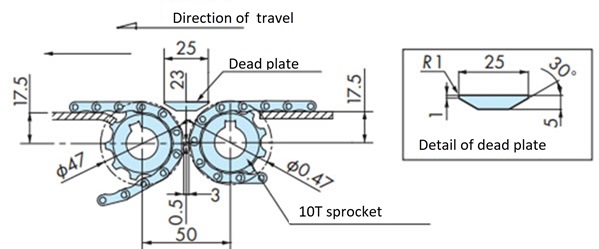
・For straight transfer with round bar (φ18)
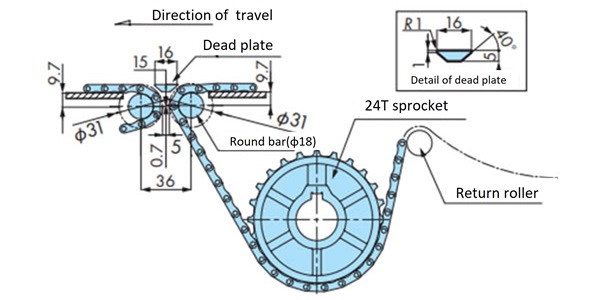
Note) The position level of the dead plate should be finely adjusted according to transfer conditions of the conveyed products.
2-10. In-line layout of WT2520 series
By installing a Φ50 round bar at conveyor ends, transfer space between conveyors can be reduced. The layout is forward/reverse bottom drive.
・In-line layout of WT2525-K/WT2525-M
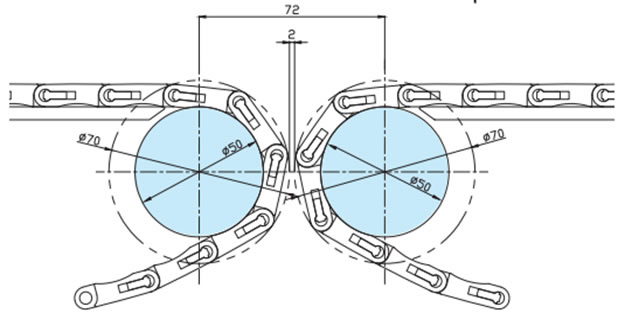
・In-line layout of WT2525VG-K/WT2525VG-M
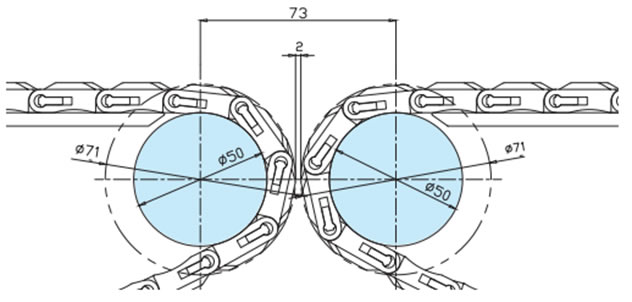
2-11. Layout of Right-Angle Transfers
By using GTO and TOD or nose bar, right angled corners can smoothly be transferred without the use of dead plates.
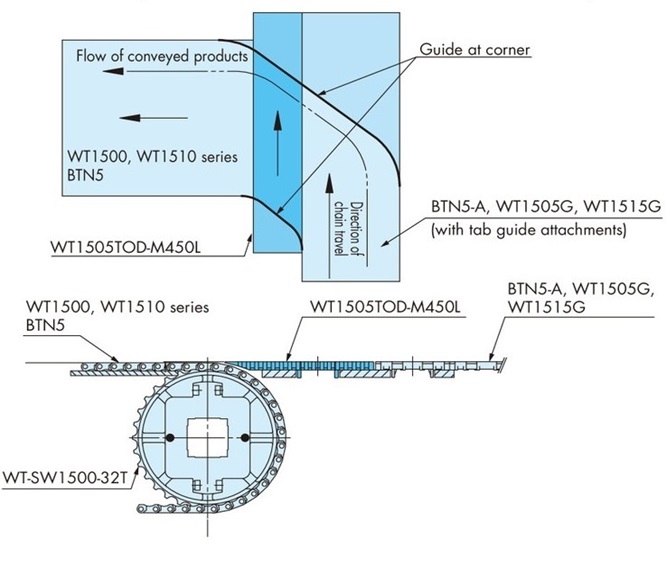
・Dimensions for mounting the chains are given below.
Insertion Conveyor (WT1505TOD/WT1500)
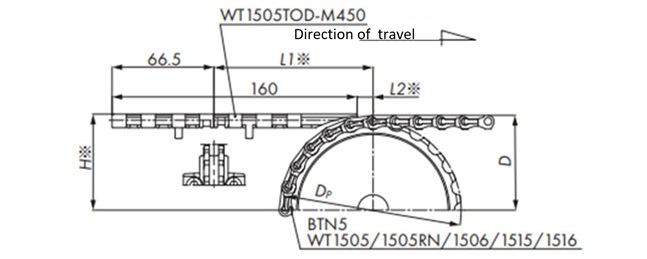
Number of teeth | Dimensions mm | ||||
---|---|---|---|---|---|
Dp | D | H※ | L1※ | L2※ | |
24 | 114.9 | 61.4 | 62.2 | 103.9 | 10.4 |
32 | 153.0 | 80.5 | 81.3 | 104.9 | 11.4 |
33 | 157.8 | 82.9 | 83.7 | 105.0 | 11.5 |
Note) The dead-plate gap (marked with ※ in illustration above) will need to be adjusted depending on the objects being conveyed.
Insertion Conveyor (WT2505TOD/WT2500)
・For WT2505TOD-M450
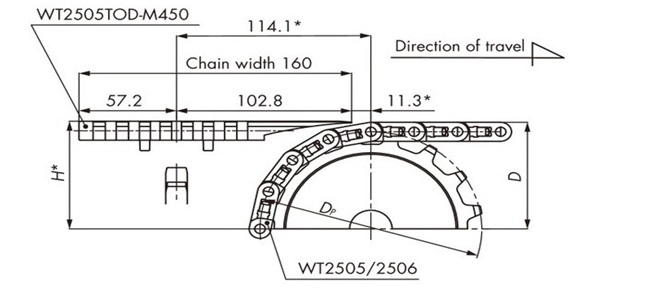
Number of teeth | Dimensions mm | ||
---|---|---|---|
Dp | D | H※ | |
16 | 130.2 | 71.4 | 72.1 |
18 | 146.3 | 79.5 | 80.3 |
21 | 170.4 | 91.6 | 92.5 |
31 | 251.1 | 131.8 | 132.6 |
Note) The dead-plate gap (marked with ※ in illustration above) will need to be adjusted depending on the objects being conveyed.
・For WT2505TOD-M750
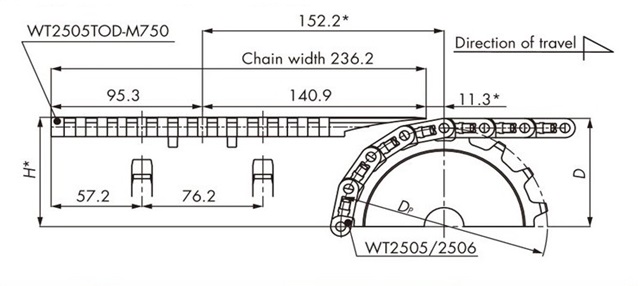
Number of teeth | Dimensions mm | ||
---|---|---|---|
Dp | D | H※ | |
16 | 130.2 | 71.4 | 72.1 |
18 | 146.3 | 79.5 | 80.3 |
21 | 170.4 | 91.6 | 92.5 |
31 | 251.1 | 131.8 | 132.6 |
Note) The dead-plate gap (marked with ※ in illustration above) will need to be adjusted depending on the objects being conveyed.
Discharge Conveyor (WT1505GTO/WT1505GTORN/WT1500)
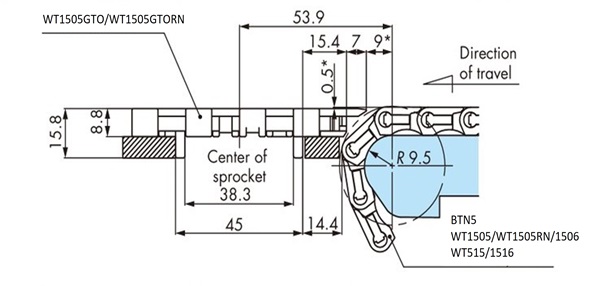
Note) The dead-plate gap (marked with ※ in illustration above) will need to be adjusted depending on the objects being conveyed.
2-12. Right-Angle Transfer with WT1500 and WT1505G
Insertion Conveyor (WT1500/WT1505G/WT1515G)
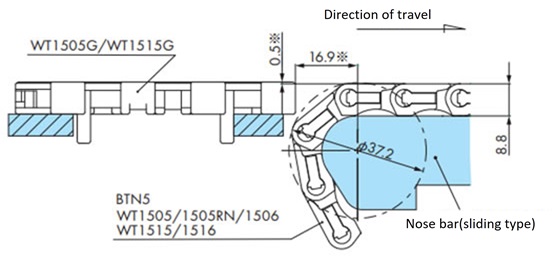
Note) The dead-plate gap (marked with ※ in illustration above) will need to be adjusted depending on the objects being conveyed.
Discharge Conveyor (WT1500/WT1505G/WT1515G)
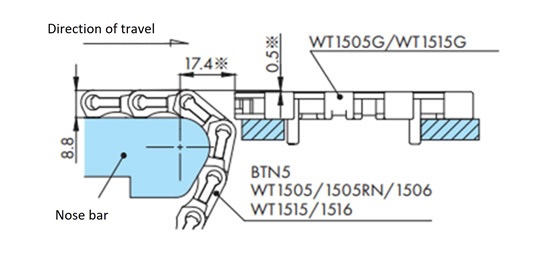
Note) The dead-plate gap (marked with ※ in illustration above) will need to be adjusted depending on the objects being conveyed.
2-13. Take-up for inclined conveyors
With inclined conveyors, the chain’s own weight can cause it to come off the driven sprocket. Therefore, installing a take-up device is recommended.
Take-up of inclined movement (horizontal + inclined + horizontal)
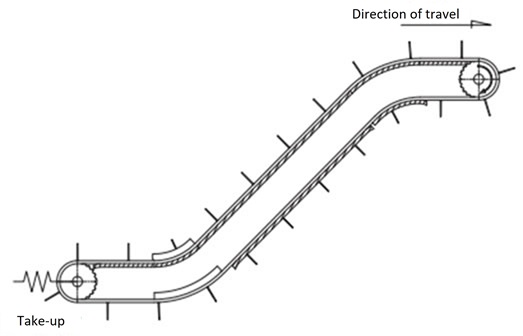
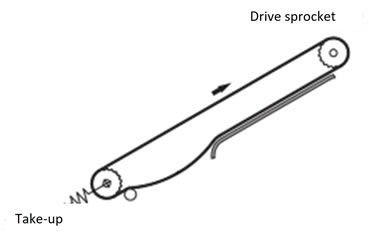
2-14. Return-way in flight type chain
Roller support reference example
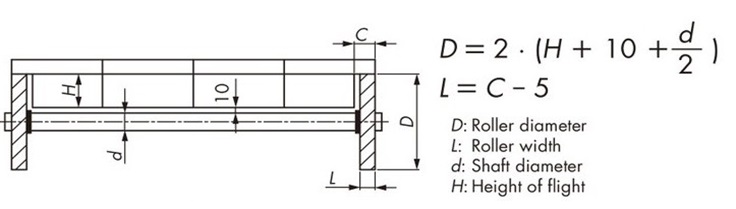
The number of return roller supports must be increased depending on the chain width to receive chain slack.
Note) Additional machining of the flight is required to avoid interference with the flight section.
Reference diagram
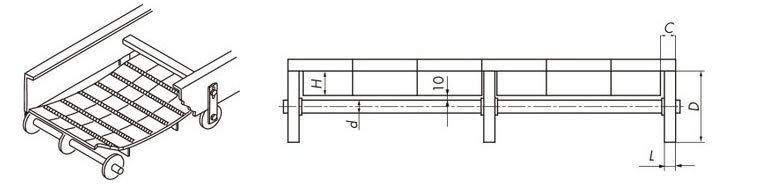
2-15. Special formation of float-preventive attachments (tabs)
In the WT1515T-F-W type, the formation of the float-preventive attachment (tab) is different when the chain width is 100 mm or 150 mm.
Chain width 100mm
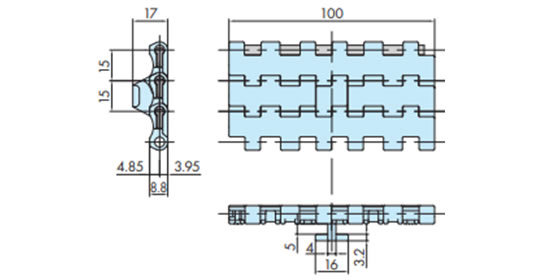
Chain width 150mm
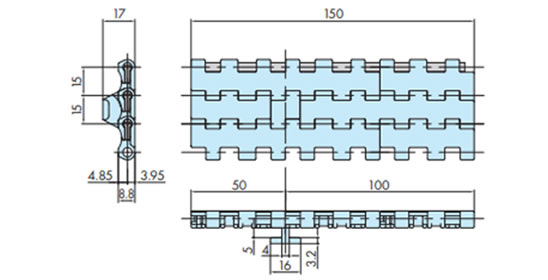
2-16. Installation of transfer plate
The figure below is a preferable layout for transfer plate installation.
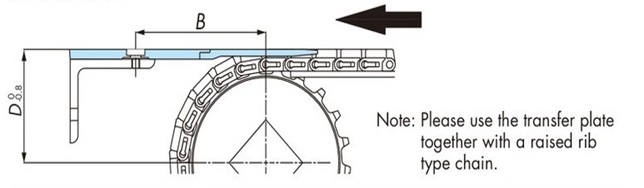
Chain Type | Transfer plate Tsubaki model no. | B mm | D mm |
---|---|---|---|
WT1907-K | WT-TP1907-L114 | 70 | Dp2 + 9.9 |
WT-TP1907-L190 | 100 | ||
WT3827-K | WT-TP3827-L152 | 82 | Dp2 + 12.7 |
WT5707-K | WT-TP5707-L220 | 82 | Dp2 + 15.5 |
Dp:Pitch Diameter
The figure on the right shows how to secure transfer plates with a dedicated cap and a screw.
Having taken thermal expansion into account, secure the screw on the plate in accordance with the guidelines below, which are separated by operating temperature.
- 1) Stable room temperature (20˚C)
The screws of transfer plates with number 2 and 3 are to be secured in the center of the slot.
- 2) Low temperature
The screws of transfer plates with number 2 and 3 are to be secured nearing the center of the chain.
- 3) High temperature
The screws of transfer plates with number 2 and 3 are to be secured nearing the edge of the chain.
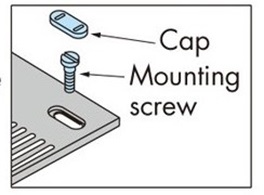