Technical Data Drive chain Roller Chain Selection
6. Allowable load selection method
Selection based on maximum allowable load
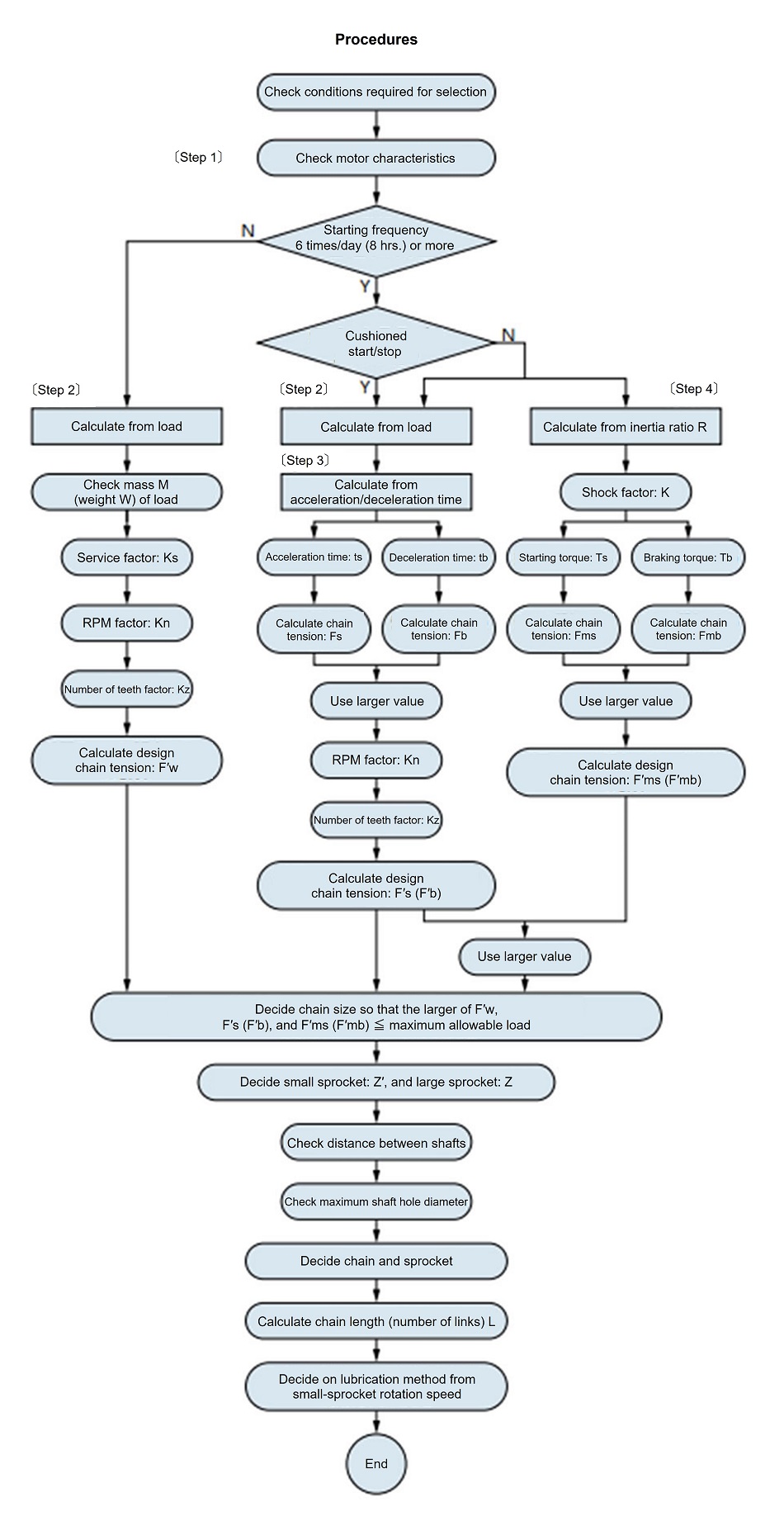
1. Speed considerations
This selection method is used when the roller chain will be used within the range of speeds shown in Table 1. When using at speeds higher than the upper limit shown in the table, use the General Selection Method to select the chain.
Pitch mm |
Speed limit m/min |
---|---|
Under 12.70 | 120 |
12.70 | 100 |
15.875 | 90 |
19.05 | 80 |
25.40 | 70 |
31.75 | 60 |
38.10 | 50 |
44.45 | 50 |
50.80 | 50 |
57.15 | 40 |
63.50 | 40 |
76.20 | 40 |
101.60 | 30 |
127.00 | 30 |
The speed limit for Poly Steel Chain is 70 m/min.
2. Impact considerations
For transmission with large impacts and other extreme conditions, in particular large-load transmission and transmission where a thrust load may operate, use F-type connecting links or two-pitch offset links.
3. Strength of connecting links and offset links
When using M-type connecting links or offset links for roller chains shown in Tables 2 and 3, multiply the maximum allowable load by the percentage given in the tables.
RS roller chain | RS15, RS25, RS37, RS38, RS41, BF25-H |
80% |
RS roller chain BS/DIN standard | RF06B, RS56B, RS56B |
80% |
Cold Resistant Roller Chain KT Series | all sizes | 80% |
Offset link | |||
---|---|---|---|
1-pitch | 2-pitch | 4-pitch | |
RS roller chain | 65% | 100% | - |
RS roller chain BS/DIN standard | 60% | 60% | - |
Super chain | - | - | 85% |
RS roller chain NP Series | 65% | - | - |
RS roller chain NEP/APP Series | 65% | - | - |
Low-noise chain | 65% | - | - |
4. Sprocket considerations
When heavy-duty drive chain is used, chain tension will increase. For this reason, commercially available cast iron sprockets may not have sufficient rim or hub strength. Use S35C or equivalent material. RS sprockets have the strength capable of handling heavy-duty drive chain. For heavy duty drive chain, use sprockets with hardened teeth.
Please also refer to the calculation formulas (click here) and factors (click here) used for chain selection, as well as calculating moment of inertia (click here).
Selection example using the allowable load selection method
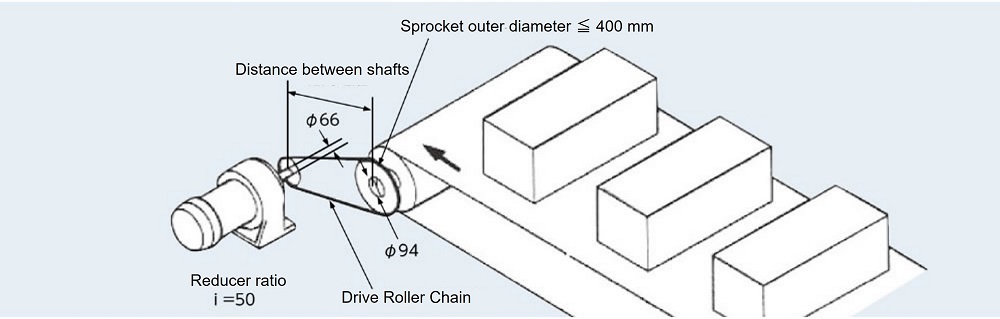
Conditions
Machine to be used | Conveyor drive |
Weight of conveyed goods M | 6000kg |
Load speed Vℓ | 30m/min |
Conveyor roller diameter | 380mm |
Belt thickness | 10mm |
Conveyor roller rotation torque | 3.3kN・m{337kgf・m} |
Motor |
|
Reducer reduction ratio | 1/50 (i = 50) |
Drive shaft diameter | Shaft diameter Φ66mm |
Driven shaft diameter | Shaft diameter Φ94mm |
Distance between shafts | 500mm |
Driven sprocket diameter | ≦400mm |
Starting frequency | 10 times /day |
Type of impact | Moderate shock |
Soft start/stop | None |
SI Unit |
---|
Steps 1 Check motor characteristics・Braking torque ・Starting torque ・Maximum (stalling) torque ・Braking torque ・Motor moment of inertia Steps 2 Calculate from loadDriven shaft revolution Drive shaft revolution Chain reducer ratio = 23.9 36 = 1 1.51 If the driven sprocket PCD d2 = 400mm Tentatively select the chain. With moderate shock .......Service factor Ks = 1.3 Tentative design chain tension = Fw × Ks = 16.5 × 1.3 = 21.5(kN) Tentatively select RS120-1 with a maximum allowable load of 30.4 kN. 31T from driven sprocket < 400mm Number of teeth of drive sprocket = 31 1.51 = 21T PCD d = 255.63(mm) Chain speed =
P × Z'× n
1000
=
38.1 × 21 × 36
1000
Small sprocket RPM 36r/min・RPM Kn = 1.03 Number of teeth of small sprocket 21T....Number of teeth factor Kz = 1.10 Chain load Fw = Conveyor roller rotation torque × 1000 ×
2
d2
Design chain tension F'w = Fw × Ks × Kn × Kz RS120-1 (Max. allowable load: 30.4kN) can be used. Check the conveyance speed (Selection criteria 30m/min) Vℓ = n2 ×
(Conveyor roller diameter + 2 × Belt thickness ) × π
1000
Steps 3 Calculate from acceleration/deceleration timeThe small sprocket (reducer output shaft sprocket) was decided as RS120 21T from the calculations in Step 2.Thus, calculate using the same pitch and number of teeth. If the acceleration/deceleration time is known, use that value for the calculation. The following is calculated assuming it is unknown. Working torque Tm = Ts + Tmax 2 = 0.116 + 0.122 2 = 0.119(kN・m) Load torque Tℓ = Fw ×
d
2 × 1000 × i
= 17.5 ×
255.63
2 × 1000 × 50
Motor shaft conversion Moment of inertia on the load side Iℓ Motor moment of inertia Im = 0.088(kg・m2)
Acceleration time of the motor
Deceleration time of the motor As tb < ts, chain tension during deceleration Fb is larger than chain tension during acceleration Fs. Thus, use the following. Deceleration Chain tension during deceleration
Design chain tension Considering RS140 18T (outer diameter 279 mm d1 = 255.98) and 27T (outer diameter 407 mm d2 = 382.88) with similar PCD results conflict with the driven sprocket outer diameter≦ 400 mm, they cannot be used.
Chain reduction ratio becomes 2618 from the required 3623.9, and conveyance speed = 30 × 3623.9 × 2618 = 31.3m/min, but upon examination 26T (outer diameter 393mm d2 = 368.77) RS140-1 cannot be used because its maximum allowable load is 40.2 kN. RS140-SUP-1 can be used because its maximum allowable load is 53.9 kN. Since the sprocket bore diameter of 18T is up to 89 mm, and for 26T is up to 103 mm, it can be used with a drive shaft diameter of 66 mm and driven shaft diameter of 94 mm. With the distance between shafts at 500 mm, a sprocket with 18T (d1=255.98) and 26T (d2=368.77) can be used. Number of links will be 46 links. Steps 4 Calculate from inertia ratio RInertia ratio R = Iℓ Im = 0.044 0.088 = 0.5 There is clearance in the drive equipment····Shock factor K = 1.0 Starting torque Ts = 0.116(kN・m) Chain tension from starting torque Braking torque Tb = 0.116(kN・m) Chain tension from braking torque Since Fmb>Fms, use the larger Fmb. Design chain tension
Comparing (1),(2), and (3), (3) has the largest design chain tension. Since F′mb=61.7 (kN), RS120-3 (maximum allowable load 76.0 kN) or RS120-SUP-2 (maximum allowable load 66.7 kN) is usable. With the distance between shafts at 500mm, a sprocket with 21T (d1=255.63) and 31T (d2=376.60) can be used. Number of links will be 54 links. Considering RS160 15T (outer diameter 269mm d1 = 244.33) and 23T (outer diameter 400mm d2 = 373.07) with similar PCD, (3) F'mb = 64.6 (kN) will be largest. RS160-1 cannot be used because its maximum allowable load is 53.0 kN. RS160-SUP-1 can be used because its maximum allowable load is 70.6 kN. Since a sprocket bore diameter with 15T is up to 95mm, and 23T is up to 118mm, it can be used for a drive shaft diameter of 66mm, and driven shaft diameter of 94mm. With the distance between shafts at 500mm, a sprocket with 15T (d1 = 244.33) and 23T (d2 = 373.07) can be used. Number of links will be 40 links. |
{Gravity unit } |
---|
Steps 1 Check motor characteristics・Braking torque ・Starting torque ・Maximum (stalling) torque ・Braking torque ・GD2 of the motor Steps 2 Calculate from loadDriven shaft revolution Drive shaft revolution Chain reducer ratio = 23.9 36 = 1 1.51 If the driven sprocket PCD d2 = 400mm Tentatively select the chain. With moderate shock .......Service factor Ks = 1.3 Tentative design chain tension = Fw × Ks = 1690 × 1.3 = 2200(kgf) Tentatively select RS120-1 with a maximum allowable load of 3100 kgf. 31T from driven sprocket < 400mm Number of teeth of drive sprocket = 31 1.51 = 21T PCD d = 255.63(mm) Chain speed =
P × Z'× n
1000
=
38.1 × 21 × 36
1000
Small sprocket RPM 36r/min・RPM Kn = 1.03 Number of teeth of small sprocket 21T....Number of teeth factor Kz = 1.10 Chain load Fw = Conveyor roller rotation torque × 1000 ×
2
d2
Design chain tension F'w = Fw × Ks × Kn × Kz RS120-1 (Max. allowable load: 3100kgf) can be used. Check the conveyance speed (Selection criteria 30m/min) Vℓ = n2 ×
(Conveyor roller diameter + 2 × Belt thickness ) × π
1000
Steps 3 Calculate from acceleration/deceleration timeThe small sprocket (reducer output shaft sprocket) was decided as RS120 21T from the calculations in Step 2.Thus, calculate using the same pitch and number of teeth. If the acceleration/deceleration time is known, use that value for the calculation. The following is calculated assuming it is unknown. Working torque Tm = Ts + Tmax 2 = 11.9 + 12.5 2 = 12.2(kgf・m) Load torque Tℓ = Fw ×
d
2 × 1000 × i
= 1790 ×
255.63
2 × 1000 × 50
Motor shaft conversion GD2 of the load side GD2 of the motor GD2m = 0.352(kgf・m2) Acceleration time of the motor
Deceleration time of the motor As tb < ts, chain tension during deceleration Fb is larger than chain tension during acceleration Fs. Thus, use the following. Deceleration Chain tension during deceleration
Design chain tension Considering RS140 18T (outer diameter 279 mm d1 = 255.98) and 27T (outer diameter 407 mm d2 = 382.88) with similar PCD results conflict with the driven sprocket outer diameter≦ 400 mm, they cannot be used.
Chain reduction ratio becomes 2618 from the required 3623.9, and conveyance speed = 30×3623.9×2618 = 31.3m/min but upon examination 26T (outer diameter 393mm d2=368.77) RS140-1 cannot be used because its maximum allowable load is 4100 kgf. RS140-SUP-1 can be used because its maximum allowable load is 5500 kgf. Since the sprocket bore diameter of 18T is up to 89 mm, and for 26T is up to 103 mm, it can be used with a drive shaft diameter of 66 mm and driven shaft diameter of 94 mm. With the distance between shafts at 500 mm, a sprocket with 18T (d1=255.98) and 26T (d2=368.77) can be used. Number of links will be 46 links. Steps 4 Calculate from inertia ratio RInertia ratio R = GD2ℓ GD2m = 0.176 0.352 = 0.5 There is clearance in the drive equipment····Shock factor K = 1.0 Starting torque Ts = 11.9(kgf・m) Chain tension from starting torque Braking torque Tb = 11.9(kgf・m) Chain tension from braking torque Since Fmb>Fms, use the larger Fmb. Design chain tension
Comparing (1),(2), and (3), (3) has the largest design chain tension. Since F′mb = 6330 (kgf), RS120-3 (maximum allowable load 7550 kgf) or RS120-SUP-2 (maximum allowable load 6800 kgf) is usable. With the distance between shafts at 500mm, a sprocket with 21T (d1=255.63) and 31T (d2=376.60) can be used. Number of links will be 54 links. Considering RS160 15T (outer diameter 269mm d1 = 244.33) and 23T (outer diameter 400mm d2 = 373.07) with similar PCD, (3) F'mb = 6620 (kgf) will be largest. RS160-1 cannot be used because its maximum allowable load is 5400 kgf. RS160-SUP-1 can be used because its maximum allowable load is 7200 kgf. Since a sprocket bore diameter with 15T is up to 95mm, and 23T is up to 118mm, it can be used for a drive shaft diameter of 66mm, and driven shaft diameter of 94mm. With the distance between shafts at 500mm, a sprocket with 15T (d1 = 244.33) and 23T (d2 = 373.07) can be used. Number of links will be 40 links. |
Selection results
Conditions | Steps | Model No. | Sprocket | No. of links | Lubrication method |
---|---|---|---|---|---|
Starting frequency less than 6 times | Steps 2 | RS120-1 | 21T×31T | 54 links | AII |
Staring frequency 6 times or more with cushioned start |
Steps 3 | RS120-2 | 21T×31T | 54 links | AII |
RS140-SUP-1 | 18T×26T | 46 links | B | ||
Staring frequency 6 times or more without cushioned start |
Steps 3 Steps 4 |
RS120-3 | 21T×31T | 54 links | AII |
RS120-SUP-2 | B | ||||
RS160-SUP-1 | 15T×23T | 40 links | B |
- Note) 1.Refer to the kilowatt ratings tables for the lubrication method of each chain size and type.
- 2.All shaft distances need to be adjusted.
Please also refer to the calculation formulas (click here) and factors (click here) used for chain selection, as well as calculating moment of inertia (click here).