Technical Data Drive chain Roller Chain Selection
5. General selection method
Ordinary transmission (forward/reverse), continual revolution transmission
Steps 4・5 Select chain and number of teeth of small sprocket
Use the provisional selection graphs (click here) or the kW ratings tables to obtain a chain and small sprocket number of teeth that satisfy the revolution speed of the high-speed shaft and the transmission kW.
Select a chain with the smallest pitch that has the required kW ratings.
If a single-strand chain does not have sufficient power, select a multi-strand chain. If site restrictions require a short distance between shafts and the smallest possible sprocket outer diameter, use a multi-strand roller chain with a small pitch.
Steps 6 Select number of teeth for large sprocket
Once the number of teeth of the small sprocket has been decided, the number of teeth of the large sprocket is determined by multiplying the number of teeth of the small sprocket by the speed ratio.
The number of teeth of the small sprocket should be at least 15. However, it is not desirable if this causes the number of teeth of the large sprocket to exceed 120.
In this event, the number of teeth of the small sprocket must be reduced; however, it is recommended to use more than 13 teeth.
Steps 7 When the number of links is odd
If the number of links is odd, it is best to avoid using an offset link and instead change the distance between shafts so that the number of links is even.
If the one-pitch offset link of RS roller chain or the four-pitch offset link of Super Chain is used, allow for a decrease of transmission power as explained in the notes in the kW ratings tables.
Provisional Selection Graph
・How to use this table ......(Fig. 2 )
(ex. )Single-strand chain, design kW = 7kW
- 1. Assume that the speed of the small sprocket is 100 rpm.
Judging from the intersecting point of design kW value of 7 kW (vertical axis) and the speed value of 100 rpm (horizontal axis), RS80 and a sprocket with between 13 and 18 teeth would be appropriate. Therefore, based on the position of the intersection, we can see that a 15T sprocket can be used. - 2. Assume that the speed of the small sprocket is 200 rpm.
Following the same procedure shown in the above example, RS60 and a sprocket with less than 18 teeth or RS60 and a sprocket with more than 13 teeth would be appropriate. This table is used for tentative selections only. The kW ratings tables should be used to confirm the chain sizes. - 3. Please allow for a drop in the kW rating values shown in the each design kW ratings chart when 1-pitch offset links or Super Chain 4-pitch offset links are used.
Fig. 2 RS Standard Roller Chain provisional selection graph
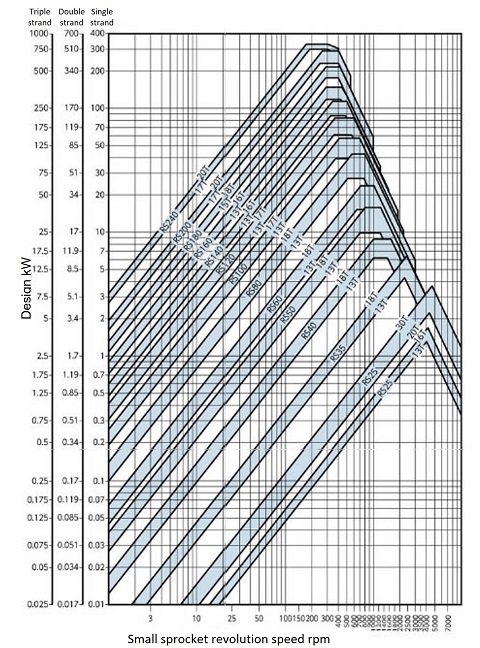
Fig. 3 Heavy Duty RS-HT Roller Chain provisional selection graph
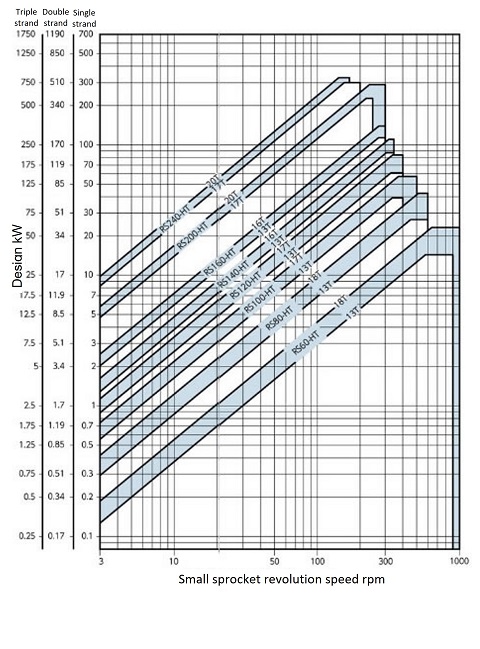
Fig. 4 RS Super Roller Chain provisional selection graph
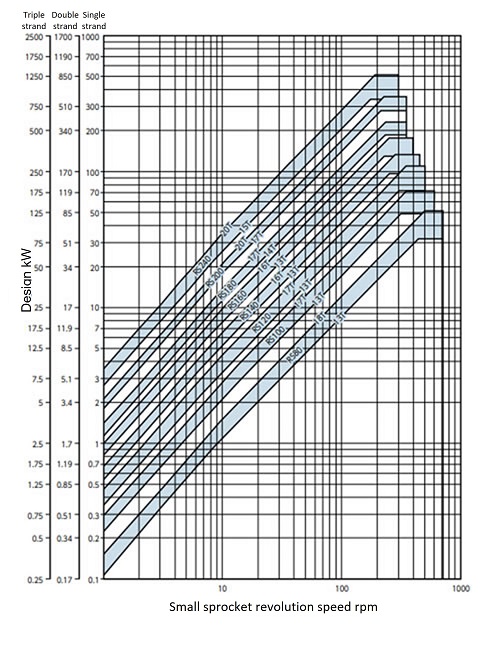
Fig. 5 BS/DIN Standard Roller Chain provisional selection graph
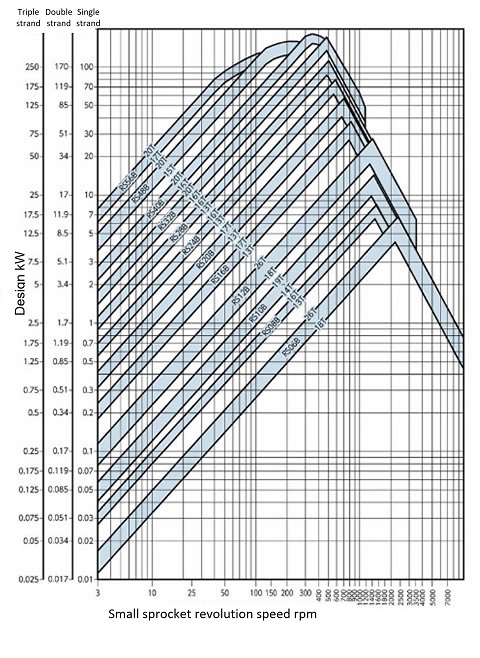
Provisional Selection Graph
・How to use this table ......(Fig. 2 )
(ex. )Single-strand chain, design kW = 7kW
- 1. Assume that the speed of the small sprocket is 100 rpm.
Judging from the intersecting point of design kW value of 7 kW (vertical axis) and the speed value of 100 rpm (horizontal axis), RS80 and a sprocket with between 13 and 18 teeth would be appropriate. Therefore, based on the position of the intersection, we can see that a 15T sprocket can be used. - 2. Assume that the speed of the small sprocket is 200 rpm.
Following the same procedure shown in the above example, RS60 and a sprocket with less than 18 teeth or RS60 and a sprocket with more than 13 teeth would be appropriate. This table is used for tentative selections only. The kW ratings tables should be used to confirm the chain sizes. - 3. Please allow for a drop in the kW rating values shown in the each design kW ratings chart when 1-pitch offset links or Super Chain 4-pitch offset links are used.
Fig. 2 RS Standard Roller Chain provisional selection graph
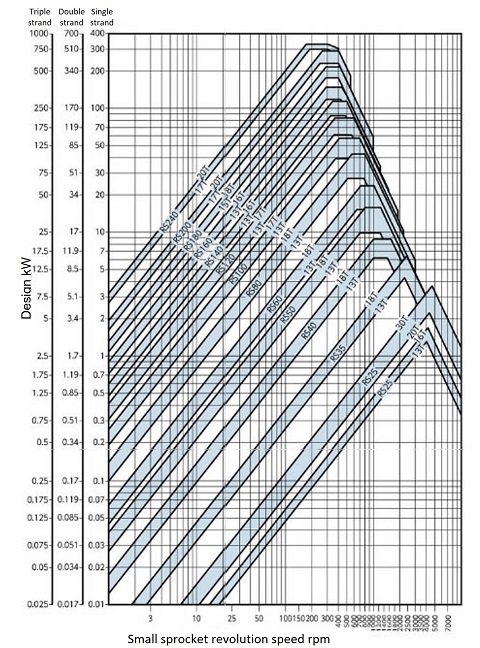
Fig. 3 Heavy Duty RS-HT Roller Chain provisional selection graph
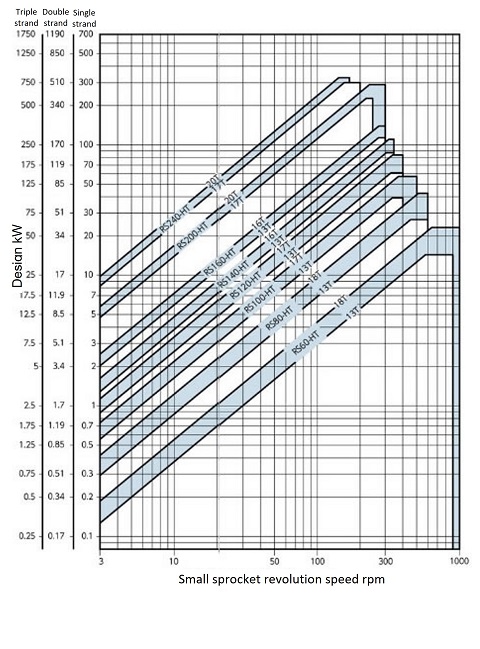
Fig. 4 RS Super Roller Chain provisional selection graph
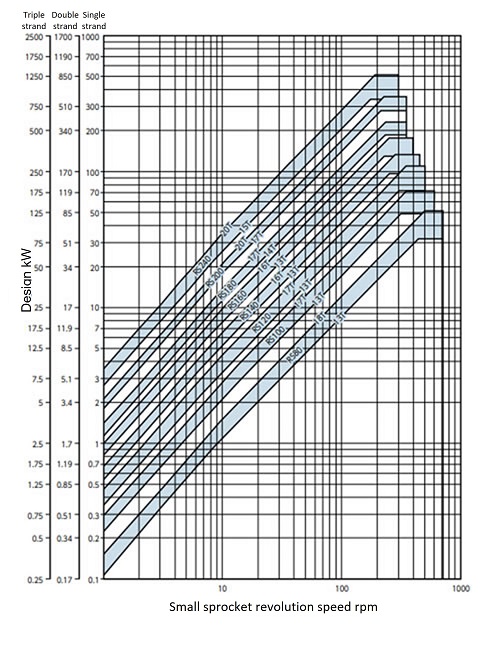
Fig. 5 BS/DIN Standard Roller Chain provisional selection graph
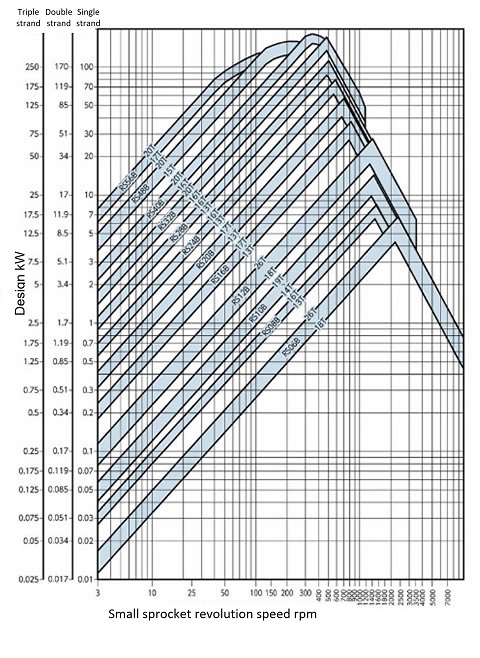
Provisional Selection Graph
・How to use this table ......(Fig. 2 )
(ex. )Single-strand chain, design kW = 7kW
- 1. Assume that the speed of the small sprocket is 100 rpm.
Judging from the intersecting point of design kW value of 7 kW (vertical axis) and the speed value of 100 rpm (horizontal axis), RS80 and a sprocket with between 13 and 18 teeth would be appropriate. Therefore, based on the position of the intersection, we can see that a 15T sprocket can be used. - 2. Assume that the speed of the small sprocket is 200 rpm.
Following the same procedure shown in the above example, RS60 and a sprocket with less than 18 teeth or RS60 and a sprocket with more than 13 teeth would be appropriate. This table is used for tentative selections only. The kW ratings tables should be used to confirm the chain sizes. - 3. Please allow for a drop in the kW rating values shown in the each design kW ratings chart when 1-pitch offset links or Super Chain 4-pitch offset links are used.
Fig. 2 RS Standard Roller Chain provisional selection graph
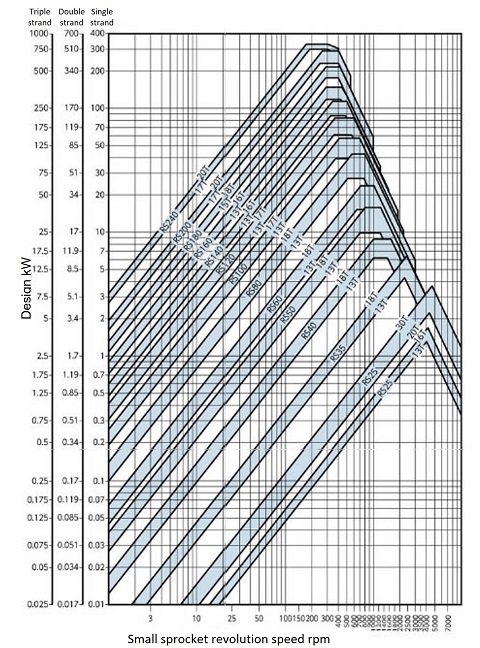
Fig. 3 Heavy Duty RS-HT Roller Chain provisional selection graph
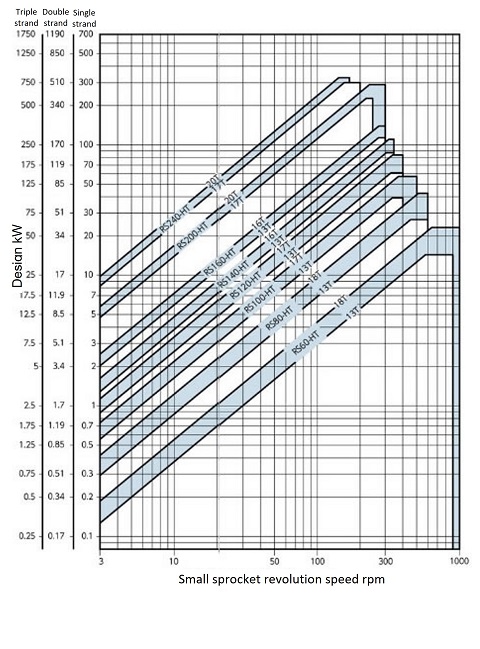
Fig. 4 RS Super Roller Chain provisional selection graph
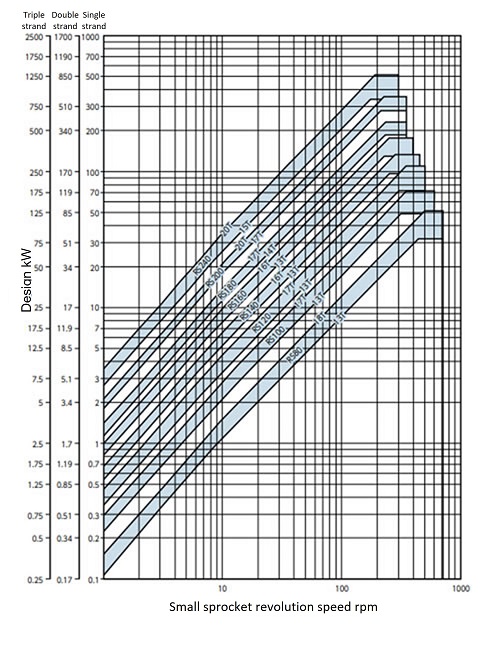
Fig. 5 BS/DIN Standard Roller Chain provisional selection graph
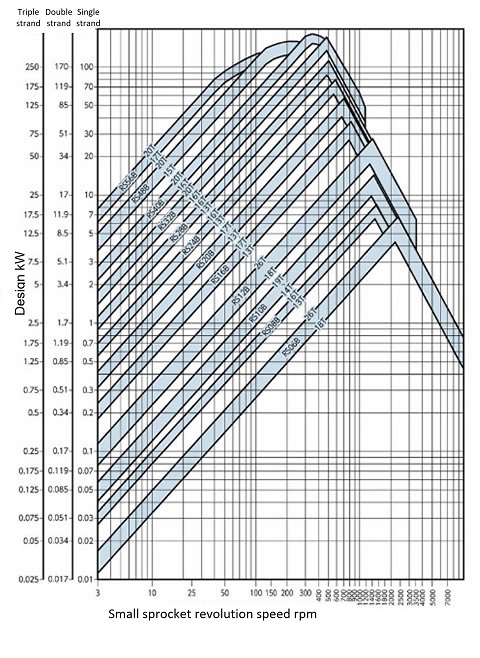
Service factor Ks
The kW ratings are based on conditions of minimal load fluctuation. Depending on the degree of load fluctuation, it may be necessary to correct the kilowatt ratings using the service factor Ks.
Use Table 2 below to determine the appropriate service factor based on the type of machine and the source of power.
The design kW value is obtained by multiplying the kilowatt ratings by the service factor.
Type of impact | Example of machine used | Motor type | ||
---|---|---|---|---|
Motor or turbine | internal combustion engine | |||
With hydraulic drive | Without hydraulic drive | |||
Smooth | Belt conveyors with little load fluctuation, chain conveyors, centrifugal pumps, centrifugal blowers, ordinary textile machines, and ordinary machines with little load fluctuation. | 1.0 | 1.0 | 1.2 |
Moderate | Centrifugal compressors, marine engines, conveyors with moderate load fluctuation, automatic furnaces, dryers, pulverizers, general machine tools, compressors, general construction machines, general paper mill machines. | 1.3 | 1.2 | 1.4 |
Large | Presses, crushers, construction and mining equipment, vibration machines, oil well rigs, rubber mixers, rolls, roll gangs, general machines with reverse or large-impact loads | 1.5 | 1.4 | 1.7 |
Selection example using the general selection method
Steps 1 Required conditions
- Machine to be used :Mixer
- Type of impact :Moderate shock
- Motor type :Motor
- Rated power :11kW 1800r/min
- High-speed shaft :Shaft Bore Diameter Φ45 90r/min
- Low-speed shaft :Shaft Bore Diameter Φ60 30r/min
- Distance between shafts :350mm
- others :Space to place the chain 700mm
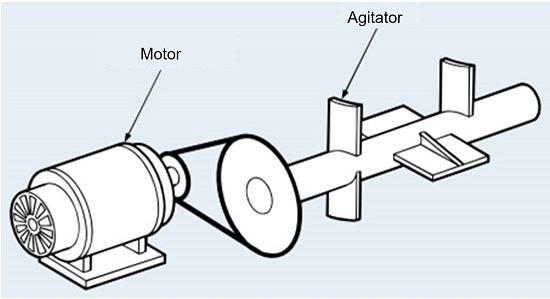
Steps 2 Determine the service factor
Service factor Ks = 1.3 from Table 2 Service Factor
Type of impact | Example of machine used | Motor type | ||
---|---|---|---|---|
Motor or turbine | internal combustion engine | |||
With hydraulic drive | Without hydraulic drive | |||
Smooth | Belt conveyors with little load fluctuation, chain conveyors, centrifugal pumps, centrifugal blowers, ordinary textile machines, and ordinary machines with little load fluctuation. | 1.0 | 1.0 | 1.2 |
Moderate | Centrifugal compressors, marine engines, conveyors with moderate load fluctuation, automatic furnaces, dryers, pulverizers, general machine tools, compressors, general construction machines, general paper mill machines. | 1.3 | 1.2 | 1.4 |
Large | Presses, crushers, construction and mining equipment, vibration machines, oil well rigs, rubber mixers, rolls, roll gangs, general machines with reverse or large-impact loads | 1.5 | 1.4 | 1.7 |
Steps 3 Determine the design kW
Design kW = 11 kW X 1.3 = 14.3 kW
Steps 4・5 Determine the chain and the number of teeth for the sprocket
Decide on the chain number and number of teeth of the small sprocket derived from the speed of the high speed shaft, at 90 rpm, and the design kW (14.3 kW).
-
(1)17T for RS100-1 is derived from the provisional selection graph (click here) and the kilowatt ratings table.
Since the speed ratio is 1/3, the number of teeth will be 17T and 51T for RS100.
But, with an outer diameter of 17T at 189 mm and 51T at 534 mm, these are not adequate because they do not fit in the required space.
∵ 189 + 534 > 700 -
(2)Checking multi-strand chains:
19T and 57T for RS80-2 is derived with double strand chain, and the outer diameter of its sprockets are 167 mm and 476 mm, which is within space limitations.
Check RS80 kilowatt ratings table for the kW ratings of 19T for RS80-2.
The kW ratings for the small sprocket number of teeth (19T) is 5.06 kW at 50 rpm, and 9.44 kW at 100 rpm. By calculating proportionally using the differences in their tables, drive kW for 90 rpm is 8.56 kW. -
(3)This 8.56 kW is the kilowatt rating of single-strand chain, and the kilowatt rating of double-strand chain that will be used is derived from the multi strand factor in Table 1.
8.56kW × 1.7 = 14.6kW×(Drag to move. )Multi-strand coefficient
The load borne by multi-strand roller chain is unequal across the width of the chain, and thus it cannot be expected that the transmission capacity will be equal to the capacity of a single-strand roller chain multiplied by the number of strands.
For this reason, the transmission capacity of multi-strand roller chain is obtained by multiplying the transmission capacity of single-strand roller chain by a multi-strand factor.
Table 1 Multi-strand coefficient Number of roller chain strands Multi-strand coefficient Double-strand 1.7 Triple-strand 2.5 Quadruple-strand 3.3 Quintuple-strand 3.9 Sextuple-strand 4.6 - (4)This kW rating, 14.6 kW, satisfies the design kW (14.3 kW).
Steps 6 Check the bore diameter
Check the bore diameter on the dimension table. Maximum bore diameter for RS80-2-19T is 66 mm, and it can be used for the required bore diameter of 45 mm.
Maximum bore diameter for RS80-2-57T is 89 mm, and it can be used for the 60 mm.
Steps 7 Determine the distance between shafts
With a distance between shafts of 350 mm, (167 + 476)2 < 350, and it will fit into the required space.
Number of the links is calculated as
Ordinary transmission between two shafts
- (1)When the number of teeth and distance between shafts has been decided for both sprockets:
L = Z + Z' 2 + 2C + Z - Z' 6.28 2 C
- (2)When the number of links of chain and the number of teeth has been decided:
C = 1 8 2L - Z - Z' + (2L - Z - Z')2 - 8 9.86 (Z - Z')2Even if the fractional part of the value found for L (below that of the decimal point) is small, round it up to the nearest integer and add a link.
An offset link must be used when an odd number of links exist. However, if possible, change the number of teeth on the sprocket or the distance between shafts so that an even number of links may be used.
- L:Chain length (No. of links )
- Z:Number of teeth of large sprocket
- Z':Number of teeth of small sprocket
- C:Center distance in pitches
L = 57 + 192 + 2 × 35025.4 + 57 - 196.28235025.4 = 68.2
In order to have an even number of links, raise the value to the right of the decimal point to an integer to get 70.
Steps 8 Check lubrication method
Since the small sprocket is RS80-2-19T at a speed of 90 rpm, according to the kilowatt ratings table, drip lubrication will be used.
Note) Selection of roller chains for lifting applications or shuttle traction applications
When using balance weights, it is assumed that motor capacity will be reduced and only braking force will increase.
In this case, for applications where maximum allowable load is indicated, also make a chain selection using the Allowable Load Selection Method. Then choose the roller chain that provides the greater margin of safety.
Please also refer to the calculation formula (click here) used for chain selection.