Technical Data Synchronous Belts / Belt Sprockets Selection
Selection/Example of selection based on inertial load
Parameters required for selection
The following items are parameters required for selection. Determine each condition.
- (1)Rotating equipment
Shape, dimensions, mass, revolution, acceleration (deceleration) time, shaft diameter, center distance, run hours per day, start-stop frequency, speed ratio, use or nonuse of an idler and other conditions. - (2)Linear motion equipment
Belt Sprocket pitch circle diameter, mass of a linear motion equipment, supporting method, coefficient of friction of supporting mechanism, moving speed, acceleration (deceleration) time, shaft diameter, center distance, run hours per day, start-stop frequency, speed ratio, use or nonuse of an idler and other conditions.
Calculation of moment of inertia
Calculate the moment of inertia as follows:
- (1) Rotating equipment
・Solid cylinder
I = 1 8 mD2・Hollow cylinder
I = 1 8 m(D2 + d2)・Rectangular cross section
I = 1 12 m(a2 + b2)・Eccentric rotating equipment
I = 1 8 mD2 + me2 - (2) Linear motion equipment
I = 1 4 mDp2
- (3) Ball screw drive
I = 1 4 m L π 2
- (4) Total moment of inertia
∑I = (I1 + I2 + ....)R2
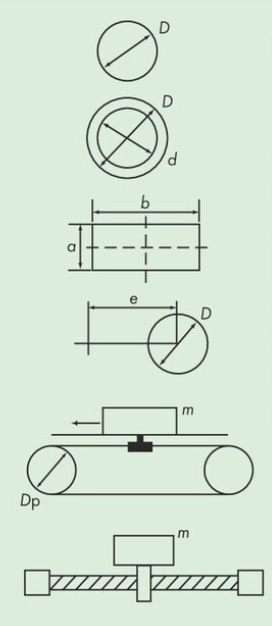
※Total the moment of inertia of all moving bodies (including the driven belt sprocket) that are driven by the belt by the equation shown on the left side.
- I:Moment of inertia of a body kg・m2
- ∑I:Total moment of inertia
- m:Mass of a rotating or Linear motion equipment kg
- D:Outside diameter of a rotating equipment m
- d:Inside diameter of the hollow of a rotating equipment m
- a:Length of a side of the rectangular cross section m
- b:Length of a side of the rectangular cross section m
- e:Distance of eccentricity m
- Dp:Belt Sprocket pitch circle diameter m
- L:Lead of screw m
- R:Reduction ratio (Number of teeth of drive belt sprocket / number of teeth of driven belt sprocket)
Calculation of acceleration (deceleration) torque
Calculate the acceleration (deceleration) torque as follows:
Pa = ∑I × (n2 - n1) 9.55 × ta
- Pa:Acceleration (deceleration) torque N・m
- n1:Revolution before acceleration (deceleration) r/min
- n2:Revolution after acceleration (deceleration) r/min
- ta:Acceleration (deceleration) time s
Calculation of continuous load torque
Calculate the continuous load torque as follows:
(1) Horizontal movement
Pc = 4.9 × mµDp
(2) Vertical movement
Pc = 4.9 × mDp
- Pc:Continuous load torque N・m
- µ:Coefficient of friction of moving body supporting mechanism
Determination of design torque
Calculate the design torque as follows: For Ko and Ka , use values in the following tables:
Pt = (Pa + Pc) × (Ko +Ki + Ks) × Ka × Ke※
Service factor
Operation hours per day h | <3 | 3~10 | 10< |
---|---|---|---|
Ko | 1.2 | 1.3 | 1.5 |
Starting frequency factor
Frequency of start-stop per day | ≦10 | 11~100 | 101~999 | 1000≦ |
---|---|---|---|---|
Ka | 1.1 | 1.2 | 1.3 | 1.5 |
- Pt:Design torque N・m
- Pa:Acceleration (deceleration) torque N・m
- Pc:Continuous load torque N・m
- Ko:Service factor Left-side figure
- Ki:Factor when idler is used ...Table 2
- Ks:Factor for speed increase ...Table 3
- Ka:Starting frequency factor Left-side figure
- Ke:Operation environment coefficient 1.2
※When the Ultra PX Belts HA Type (oil- and water-resistant type) is used in operation that is exposed to oil and water, and when the PX Belt Water Resistant Type is used in operation that is exposed to water, multiply 1.2 as the Operation environment coefficient (Ke).
※From this point on, continue with the selection process as described in “Determination of belt size and number of teeth of belt sprockets.”
An example of selection calculation (Based on InertiInertial load)
Parameters required for selection
The parameters required for selection are as follows:
Item | Description |
---|---|
(Machine tool table drive ) | |
Belt Sprocket pitch circle diameter | 50mm or less |
Mass of linear motion equipment | 50kg |
Supporting method and coefficient of friction of supporting mechanism | LM guide, coefficient of friction μ=0.1 |
Moving speed | 1000r/min |
Acceleration (deceleration) time | 0.3s |
Shaft diameter | 20mm |
Distance between shafts | 1400mm |
Hours of use and frequency of start-stop per day | 12 hours/day, 1000 times/day |
Reduction Ratio | 1:1 |
Use or nonuse of idler | なし |
Other conditions | なし |
Calculation of moment of inertia
First, obtain the moment of inertia. For the linear motion equipment, the following equation applies. Based on the above conditions, tentatively select the belt sprocket “30P5M”(number of teeth 30 , Dp= = 47.75 mm)
I = 1 4 mDp2 = 1 4 × 50 × 0.047752 = 0.0285kg・m2
Calculation of acceleration (deceleration) torque and continuous load torque
Obtain the acceleration (deceleration) torque and continuous load torque as follows:
Acceleration (deceleration) torque Pa = I × (n2 - n1) 9.55 × ta = 0.0285 × (1000 - 0) 9.55 × 0.3 = 9.95N・m
Continuous load torque Pc = 4.9 × mµDp = 4.9 × 50 × 0.1 × 0.04775 = 1.17N・m
Determination of design torque
Obtain the design torque by multiplying a total of the acceleration (deceleration) torque and continuous load torque by each correction factor.
Pt = (Pa + Pc) × (Ko + Ki + Ks) × Ka = (9.95 + 1.17) × (1.5 + 0 + 0) × 1.5 = 25.02N・m
After the determination of the design torque, follow general selection (Selection based on torque).
Determination of belt size and No. of teeth of belt sprockets
- (1) Tentatively determine a belt size from Widths applicable to the tentative selection table. Here, tentatively select “UP5M” from the design torque (25.02 N・m) and motor revolution (1000 r/min).
- (2) In consideration of the belt sprocket pitch circle diameter, speed ratio, shaft diameter and other conditions, select a belt width and the number of teeth of the belt sprocket from the standard transmission torque table.
Here, select 30 teeth (Dp=47.75 mm) of UP5M25 (belt width 25 mm). Refer to the dimensions of each belt sprocket.
Determination of belt length and center distance
- (1) Calculate an approximate belt length (L').
L' = 2C + 1.57 (Dp + dp) + (Dp - dp)2 4C = 2 × 1400 + 1.57 (47.75 + 47.75) + (47.75 - 47.75)2 4 × 1400 = 2950mm
The belt which is closest to this approximate length is “3050UP5M” (610 teeth) from the list of Belt Length.
- (2) Calculate the center distance (C).
B = L - 1.57 (Dp + dp) = 3050 - 1.57 (47.75 + 47.75) = 2900
C = B + B2 - 2(Dp - dp)2 4 = 2900 + 29002 - 2(47.75 - 47.75)2 4 = 1450mm
Correction for the number of meshing teeth
Obtain the number of teeth of the belt that mesh with the small belt sprocket and determine the meshing correction factor.
Since the speed ratio is 1:1, the number of meshing teeth is a half of 30 teeth, which is 15 teeth. Thus, the meshing correction factor is 1.0.
Determination of belt width
Finally determine the belt width that satisfies the design torque.
Kw ≧ Pt Pr × Km × KL = 25.02 9.37 × 1.0 × 1.2 = 2.23
Thus, the belt that satisfies the width factor is UP5M25 (belt width 25 mm).
Selection results
- Belt :BG3050UP5M25-HC
- Belt Sprocket :PT30P5M25AF or BF
- Distance between shafts :1450mm
After deciding on the belt sprocket model number, you can select the belt sprocket coupling method.
Please also refer to the calculation formula used for belt selection.