Technical Data Small Size Conveyor Chains Handling
Mounting
1. Sprocket attachment
Proper installation of the sprockets is critical to smooth operation of a conveyor, and it also affects chain life.
The installation should be properly carried out in accordance with the procedures described below.
(1)Check the levelness of the shafts with a level.
Adjust to within a tolerance of ± 1/300 .
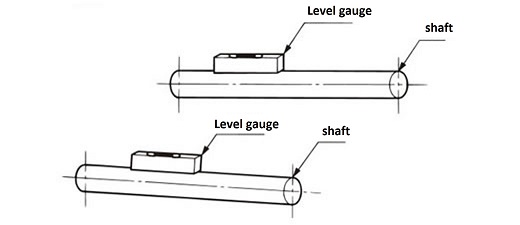
Fig. 1.Horizontal precision of the shafts
(2)Check the parallelism of the shafts with a scale.
Adjust the shafts so that the parallelism as calculated with formula (A - B)/L is to within ± 1/100.
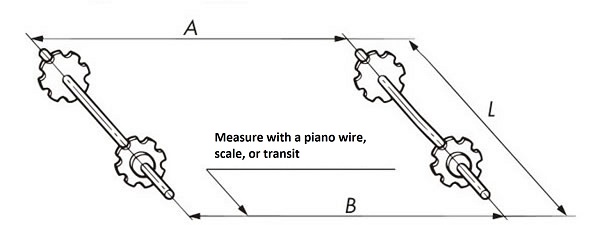
(3)Align the sprocket axis to match.
- Tolerance relative to center distance: Up to 1 m :Within 1mm
- 1 to 10 m :within {Distance between shafts (mm)}/1000
- 10 m or longer :Within 10mm
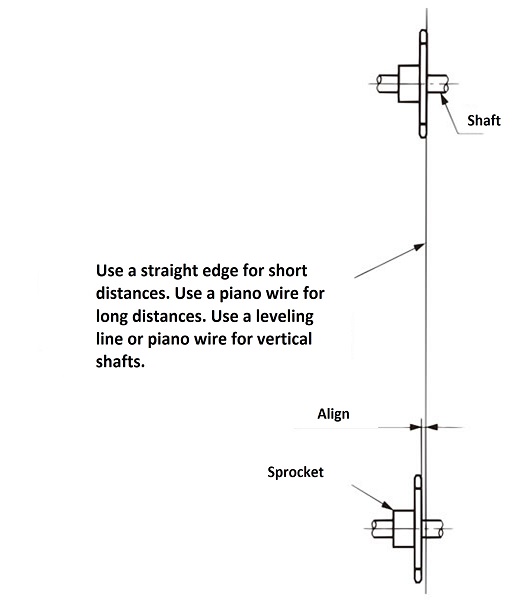
Fig. 3.Sprocket alignment
(4)After processes (1) to (3) have been completed, lock each of the sprockets to the shaft(s) by means of keys or Tsubaki POWER-LOCKS.
Lock the sprockets that are installed and used on the same shaft so that the teeth of both sprockets align in terms of phase.
2. Centering
Because the conveyor chain runs on a guide rail, the precision of the guide rail must be especially high and the conveyor properly centered.
In cases like vertical bucket elevators where there are no guide rails, if the conveyor is not precisely centered, the chain will wobble and weave. This will have a significant impact on the life of the conveyor chain.
3. Rail
In general, rails wear faster than chain.
While it is important that the rail material be matched to the chain material, in general, rolled steel for general structures (SS400) or plastic material (ultra-high molecular weight polyethylene) is recommended.
- (1)Wear is a complex phenomenon and is influenced by a variety of factors, including corrosion, lubrication, load speed, and operating time. Deducing the precise relationship between chain life and rail material is difficult.
- (2)Chain life is influenced by the rail. For new installations, verify the wear state by selecting rail material that is slightly softer than the chain. The smoother the finish on the rail surface, the better.
- (3)Operating conditions must be taken into consideration when selecting materials. In environments involving mechanical impact and other special conditions, there may be cases when plastic should not be used.
- (4)Precautions before putting rails into operation
- 1. Lubricate all rail connecting parts, chamfer edges, and eliminate uneven levels and gaps. (Fig. 4)
- 2. After welding rail, remove spatter or scale.
- 3. During the trial run, run the conveyor unloaded. Lubricate the chain and check the condition of chain and rails.
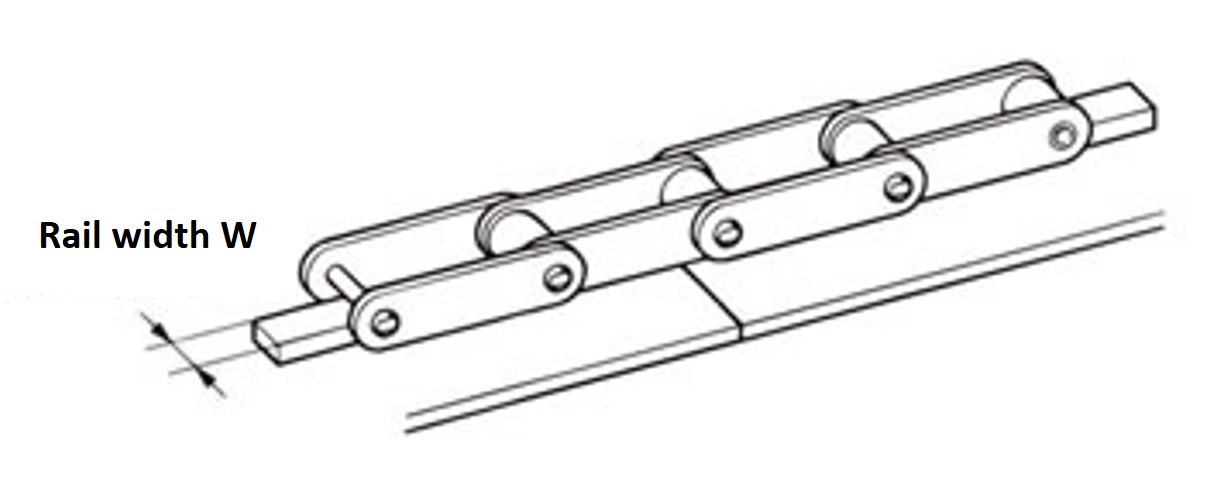
Rail width W:Generally the sprocket tooth width.
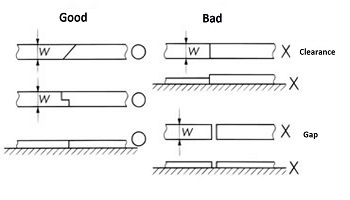
Spaces are required to account for heat expansion of the rail.
Fig. 4.Rail Joints
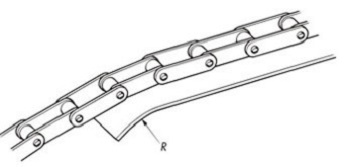
To ensure that the chain moves smoothly, bend the guide rail to a radius of R at the points where the chain engages and disengages the rail.
Fig. 5.Chain Entrance/Exit from Guide Rail