Technical Data Drive sprocket Before Use
Construction, Material, Tooth Tips, Bores
1. Construction
RS sprockets are manufactured in four types in conformance with JIS standards.
Model code | A Type (flat plate ) |
B type (Single hub ) |
C type (Dual hub ) |
SD Type (single dual ) |
---|---|---|---|---|
Construction |
![]() |
![]() |
![]() |
![]() |
Multi-strand Heavy Duty Chain (Super-H, RS-HT, etc.) Note 1 | For using two single-strand chains at the same time | |||
HB type | HC type | |||
Usage by structure | Used when mounting on a rotating body, such as the center member of Torque Limiter. | Most versatile use. | For use with large driven sprockets or when key surface pressure is insufficient with B type. | For using two single-strand chains at the same time. |
Notes
1.The total tooth width (transverse pitch) of multi-strand Heavy Duty chains (HB/HC types) differs from the standard.
2. Material
RS sprockets are available in the following material as standard.
Material | Material |
---|---|
Carbon steel | *Carbon steel for machine structural use |
Rolled steel | *Roller steel for general structural use |
Stainless Steel | *Austenitic stainless steel |
Plastic | *Engineering plastic (Engineering plastic ) |
Sintered alloy | *Iron-Based Sintered Alloy (used for some RS25 sprockets ) |
3. Teeth specifications
Package | |
---|---|
hardened teeth specifications | Use sprockets with hardened teeth when tooth strength and wear resistance need to be increased. All Tough Tooth sprockets use hardened teeth. |
Teeth unhardened | Teeth are not hardened. The teeth on RS sprockets in the large tooth range are not heat treated. |
4. Bores
The following three types of bores for attaching the sprocket to a shaft are available for RS sprockets.
Series | Appearance | Package |
---|---|---|
Standard pilot bore |
![]() |
|
Fit bore |
![]() ![]() |
|
Lock Sprocket |
![]() |
|
5. Handling Roller Chains and Sprockets
5.1 Tooth hardening
When a sprocket is used under the following conditions, the sprocket teeth must be hardened.
- 1. When there is a small number of teeth (24 or less), and the speed is 1/8 or higher of the maximum rotation speed indicated on the kilowatt ratings tables.
- 2. Small sprockets when speed ratio is greater than 4:1.
- 3. When a large load is used at low speed.
- 4. When using under conditions that will cause the teeth to wear.
5.2 Number of teeth
As many teeth as possible should be used on the sprocket on the high-speed shaft side to help ensure smooth drive transmission.
Generally, 15 or more teeth should be used. However, when the speed ratio is high and the number of teeth on the low-speed sprocket exceeds 120, chain engagement problems can occur when there is even slight chain wear.
In this case, decrease the number of teeth on the highspeed sprocket, but the number of teeth should still be kept to 13 or higher.
However, if the sprocket will be used at extremely low speed and not subjected to shock, a sprocket with 12 or fewer teeth can be used.
5.3 Precautions related to additional processing
1. shaft bore machining
- ・Maximum shaft bore processing dimensions
The maximum finished shaft bore size should be at or below the size shown in the specifications for each model number.
Please contact a Tsubaki representative if using standards other than the JIS standards key. - ・Finishing standards
When finishing, verify the standards for the tooth outer diameter DO and the hub outer diameter DH.
Also, verify that the deflection on the tooth root a and the deflection on the end surface of the tooth b are at or below the values shown below.
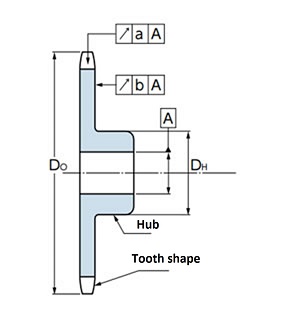
Root Diameter (df) | 90 or less | > 90 but ≤ 190 | > 190 but ≤ 850 | > 850 but ≤ 1180 | Greater than 1180 |
---|---|---|---|---|---|
Deflection at tooth root a | 0.15 | 0.0008df+0.08 | 0.76 | ||
Face runout b | 0.25 | 0.0009df+0.08 | 1.14 |
2. Sprocket welding
When welding a hub to Type A sprockets for use, the welding can cause deformation or deflection of the tooth and surface, making it impossible to maintain product quality. As such, welding should be avoided.
With Type A Strong Series sprockets, welding can also decrease the hardness of the sprockets, so again, welding should be avoided.
3. Processing on the hub outer diameter
Do not perform any additional processing to the outer diameter of the hub. If processing needs to be performed, please first contact a Tsubaki representative.
5.4 Sprocket surface treatment
When a surface treatment will be applied to standard sprockets such as plating, blackening, or other surface treatments, strictly adhere to the following:
- ・Anti-rust oil and/or anti-rust paint have been applied to the sprocket, and must be completely removed.
- ・If a hardened tooth sprocket will be subjected to a treatment that may cause hydrogen embrittlement, for example, electrolytic plating, sufficient measures must be taken to prevent this from occurring.
New JIS standard key
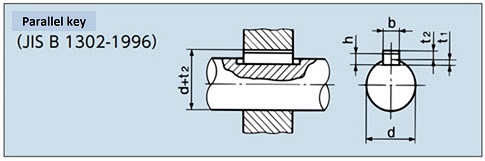
Shaft Bore Diameter d |
Designated key diameter Width × Height b×h |
Keyway Depth | |
---|---|---|---|
Shaft t1 | Hub d + t2 | ||
6 or higher 8 or lower | 2×2 | 1.2 | d + 1.0 |
8 〃 10 〃 | 3×3 | 1.8 | d + 1.4 |
10 〃 12 〃 | 4×4 | 2.5 | d + 1.8 |
12 〃 17 〃 | 5×5 | 3.0 | d + 2.3 |
17 〃 22 〃 | 6×6 | 3.5 | d + 2.8 |
20 〃 25 〃 | (7×7) | 4.0 | d + 2.3 |
22 〃 30 〃 | 8×7 | 4.0 | d + 3.3 |
30 〃 38 〃 | 10×8 | 5.0 | d + 3.3 |
38 〃 44 〃 | 12×8 | 5.0 | d + 3.3 |
44 〃 50 〃 | 14×9 | 5.5 | d + 3.8 |
50 〃 55 〃 | (15×10) | 5.0 | d + 5.3 |
50 〃 58 〃 | 16×10 | 6.0 | d + 4.3 |
58 〃 65 〃 | 18×11 | 7.0 | d + 4.4 |
65 〃 75 〃 | 20×12 | 7.5 | d + 4.9 |
75 〃 85 〃 | 22×14 | 9.0 | d + 5.4 |
80 〃 90 〃 | (24×16) | 8.0 | d + 8.4 |
85 〃 95 〃 | 25×14 | 9.0 | d + 5.4 |
95 〃 110 〃 | 28×16 | 10.0 | d + 6.4 |
110 〃 130 〃 | 32×18 | 11.0 | d + 7.4 |
125 〃 140 〃 | (35×22) | 11.0 | d + 11.4 |
130 〃 150 〃 | 36×20 | 12.0 | d + 8.4 |
140 〃 160 〃 | (38×24) | 12.0 | d + 12.4 |
150 〃 170 〃 | 40×22 | 13.0 | d + 9.4 |
160 〃 180 〃 | (42×26) | 13.0 | d + 13.4 |
170 〃 200 〃 | 45×25 | 15.0 | d + 10.4 |
200 〃 230 〃 | 50×28 | 17.0 | d + 11.4 |
230 〃 260 〃 | 56×32 | 20.0 | d + 12.4 |
260 〃 290 〃 | 63×32 | 20.0 | d + 12.4 |
290 〃 330 〃 | 70×36 | 22.0 | d + 14.4 |
330 〃 380 〃 | 80×40 | 25.0 | d + 15.4 |
380 〃 440 〃 | 90×45 | 28.0 | d + 17.4 |
440 〃 500 〃 | 100×50 | 31.0 | d + 19.5 |
Old JIS key
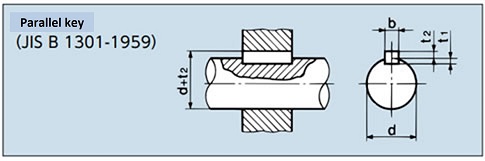
Shaft Bore Diameter d |
Designated key diameter Width × Height b×(t2+t1) |
Keyway Depth | |
---|---|---|---|
Shaft t1 | Hub d + t2 | ||
10 or higher 13 or lower | 4×4 | 2.5 | d + 1.5 |
13 〃 20 〃 | 5×5 | 3.0 | d + 2.0 |
20 〃 30 〃 | 7×7 | 4.0 | d + 3.0 |
30 〃 40 〃 | 10×8 | 4.5 | d + 3.5 |
40 〃 50 〃 | 12×8 | 4.5 | d + 3.5 |
50 〃 60 〃 | 15×10 | 5 | d + 5 |
60 〃 70 〃 | 18×12 | 6 | d + 6 |
70 〃 80 〃 | 20×13 | 7 | d + 6 |
80 〃 95 〃 | 24×16 | 8 | d + 8 |
95 〃 110 〃 | 28×18 | 9 | d + 9 |
110 〃 125 〃 | 32×20 | 10 | d + 10 |
125 〃 140 〃 | 35×22 | 11 | d + 11 |
140 〃 160 〃 | 38×24 | 12 | d + 12 |
160 〃 180 〃 | 42×26 | 13 | d + 13 |
180 〃 200 〃 | 45×28 | 14 | d + 14 |
200 〃 224 〃 | 50×31.5 | 16 | d + 15.5 |
224 〃 250 〃 | 56×35.5 | 18 | d + 17.5 |