Technical Data Linear actuator Linispeed Jack Selection
Conditions required for selection
Machine to be used ..... Table lifter, press-fit machine, etc.
Layout .....
Synchronization of two jacks (individually driven with a motor or both connected with a coupling and driven with one motor, etc.
- Maximum load (W) .....Load or workpiece weight N
- Screw Shaft Speed (V) .....Required speed for jack m/min
- Stroke .....Actual stroke used mm
Mounting style .....Face mount, flange type, etc.
Installation Conditions .....Fixed base, clevis on shaft end, etc.
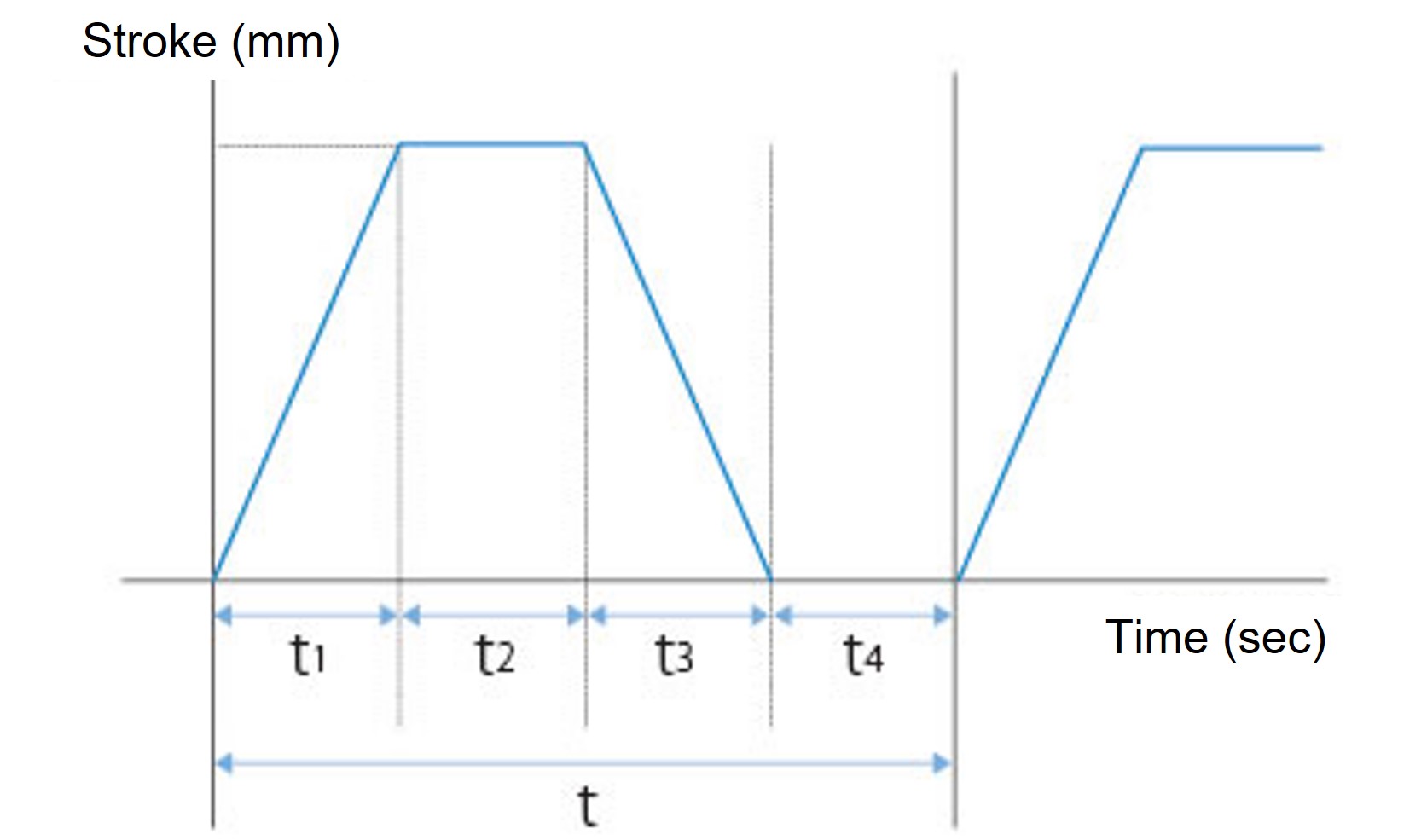
Time cycle
Selection procedure
1. Calculation of adjusted Load Ws
Calculate the adjusted Load Ws by determining the service factor (Table 1) for specific load characteristic.
Adjusted Load Ws (kN) = Maximum load W (kN)×Service factor Sf
Table 1 Service factor Sf
Load characteristics | Usage examples | Service factor |
---|---|---|
Smooth operation without impact Small load inertia |
Opening/closing a valve Adjusting a conveyor |
1.0~1.3 |
Operation with light impact Medium load inertia |
Transfer systems Various kinds of lifters |
1.3~1.5 |
Operation with large impact/vibration Large load inertia |
Large transporting carriages, Holding the position of a press roller | 1.5~3.0 |
Note) The above operation factor table shows general guidelines, and please apply the appropriate factor depending on actual condition.
2. Load per jack
Calculate load W per jack, by using the adjusted load Ws obtained above. For a synchronous drive, use a multiple factor (Table 2).
Load / jack W (kN) = Adjusted Load Ws (kN) No. of jacks ×Multiple factor fd
Table 2 Multiple factor fd
Number of multiple units ( units ) | 2 | 3 | 4 | 5~8 |
---|---|---|---|---|
Multiple factor | 0.95 | 0.9 | 0.85 | 0.8 |
3. Linispeed Jack preliminary selection
Tentatively select a model number with an allowable thrust that satisfies the load W per jack.
Select a stroke for the jack with an extra margin with respect to the operating stroke. Select a model number according to the mounting type and shaft arrangement.
Notes
- (1)All loads (static, dynamic or shock) should be within the rated capacity of the jack at sufficient safety levels.
- (2)Usage that exceeds the specified jack stroke may damage the jack. The Linispeed Jack is equipped with shaft and stopper which is designed only to prevent the screw from falling out during installation.
- (3)Do not press stop under any circumstances. This may cause critical damage to jacks.
- (4)When using a flange mount, there is a load direction that requires allowable thrust to be limited to 50%. Please see details here.
4. Expected travel distance
Make sure that the expected travel distance is satisfied. If you want to extend the expected travel distance, increase the jack frame size and recalculate.
Please click here for the details of life calculation.
5. Buckling
For a compressive load, verify that it does not exceed the allowable buckling load. (Click here )
If it exceeds the allowable value, increase jack size and recalculate.
6. Input shaft allowable overhang load
When installing a belt on the input shaft, make sure that it does not exceed the allowable overhang load.
In case it exceeds, increase the jack frame size and recalculate.
7. Confirming Required Input speed
Determine the required input speed, using the required screw shaft speed.
N = V ℓ ×R
N:Input speed r/min
V:Screw Shaft Speed m/min
ℓ:Screw lead m
R:Worm Reduction Ratio
Please refer to the product page for each specs.
The allowable input rotation speed is 3000 rpm
Please make sure that the rotation speed is below this speed.
8. Duty cycle
Please check the percentage of operation time for a single cycle (duty cycle).
Confirm that duty cycle (% ED) is within the allowable range.
For details, please see here.
The Linispeed Jack must be used under the surface temperature of gear housing does not exceed 90°C.
The table below shows approximate duty cycles (% ED) when the surface temperature of the gear housing is 90°C or lower. (These values are not guaranteed. )
Please check the surface temperature of the gear housing when you use.

SJ015H
SJ030H
SJ050H
%ED = Operation time of one cycle Operation time of one cycle + Idle time ×100(%)
The formula for calculating the duty cycle (% ED) from the time cycle table is as follows.
%ED = t1 + t3 t1 + t2 + t3 + t4 ×100(%)
9. Verifying Required Input Torque
Calculate required input torque.
When using a servomotor, please select a model number that satisfies the servomotor's allowable torque.
T = W×ℓ 2×π×R×η + To
T:Necessary input torque N・m
W:Lift load N
ℓ:Screw lead m
π:Pi (circular ratio) 3.14
R:Worm Reduction Ratio
η:Total efficiency or starting efficiency Note)
To:Idling torque without load N・m
※For screw lead, gear ratio, overall efficiency and no-load idle torque, see the major specifications page for each product. Pay attention to the unit of screw lead.
Example) 25mm ---> 0.025m
Note) Be sure to check the required input torque at the starting efficiency when the equipment is just turned on.
10. Verifying Input Capacity
P = T×N 9550
T:Necessary input torque N・m
P:Required input capacity kW
N:Input speed r/min
11. Input shaft torsional torque
The number of jacks that can be connected in a single line is limited by the strength of the shaft. Please confirm the allowable input shaft torque.
Example) When jacks are arranged in a straight line as in the figure shown below, the driving source will transmit the input torque required for both jacks to the input shaft.
This doubled torque should not exceed the allowable input torque.
※Please make sure that the torque of these two jacks do not exceed the allowable input shaft torque.
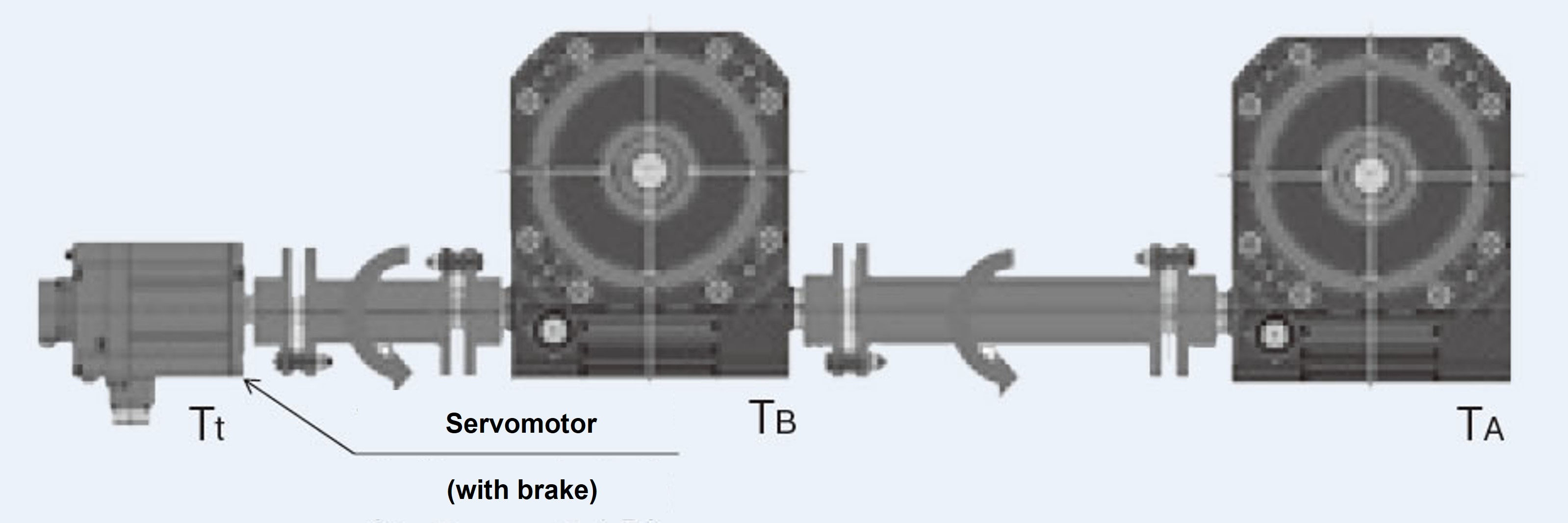
TA: Required input torque for Jack A
TB: Required input torque for Jack B
Required torque at the motor Tt = TA + TB < Allowable Torque on Input Shaft
For more details regarding allowable input shaft torque, please refer to each product pages.
12. Selecting Your Options
Select options that best suit your needs.
- ・Output Option
- ・Position Sensor Option
13. Select the Linispeed Jack model
Select the appropriate Linispeed Jack model.
Selection example
Conditions required for selection
Machine to be used ..... Four jack in synchronized operation for lifting, operating at room temperature (30°C) under low dust conditions.
Layout .....Two jacks are connected w / a coupling and driven by a servomotor with brake, and lift with two of these layouts. (Fig. 1)
Operation cycle .....See Fig. 2
- ・Maximum load (W):28kN/4
- ・Screw Shaft Speed (V):180mm/s(10.8m/min)
- ・Stroke :540mm
Mounting style .....Flange mount / cover side
Installation Conditions .....Fixed base -Fixed at shaft end (with table-type end fitting )
Expected life .....30 cycles x 2 times / hour x 8 hours / day x 250 days / year x 3 years usage
Fig. 1 Layout
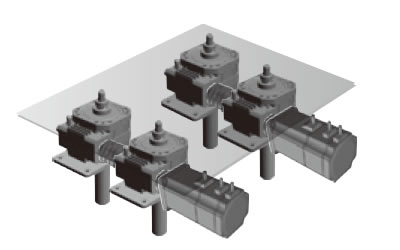
Lifting/Lowering using two aligned jacks (four jacks in total)
Fig. 2 Time cycle
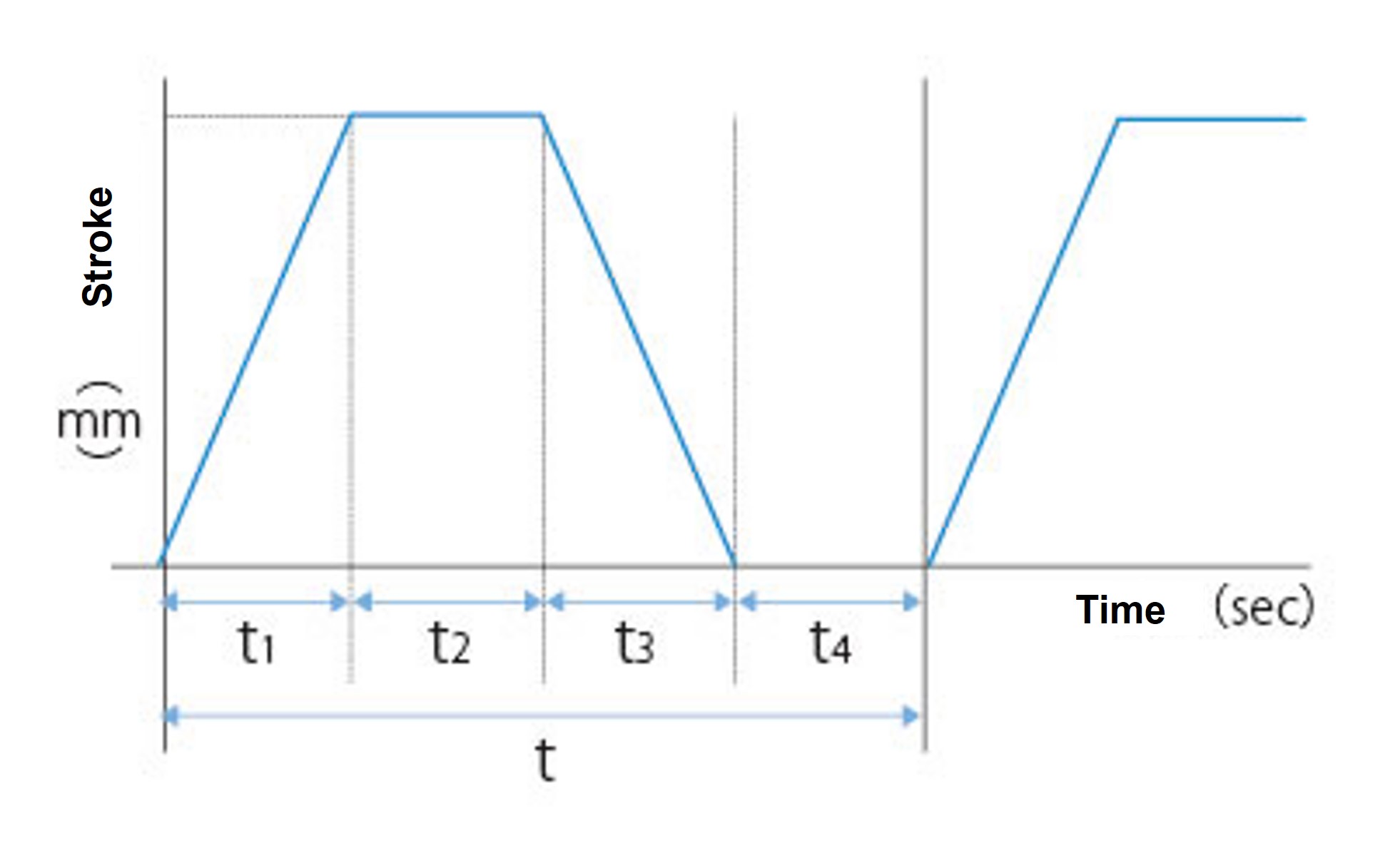
Time for each cycle | |
---|---|
t1 | 3sec |
t2 | 2sec |
t3 | 3sec |
t4 | 6sec |
t | 14sec |
-
1. Based on maximum load, the adjusted load Ws (service factor sf = 1.3) can be calculated as:
Ws = 28×1.3 = 36.4kN
-
2. The load W per jack (multi operational coefficient fd = 0.85) is:
W = 36.4 / 4 / 0.85 = 10.7kN
-
3. SJ015H model is tentatively selected by load per jack.
Considering that a 540 mm stroke is used, select 600 mm stroke.
-
4. Calculate the expected traveling distance according to the frequency of use.
Expected traveling distance = 0.54×2×30×2×8×250×10-3×3 = 388.8km
See here on expected life time of the screw shaft and then evaluate the appropriate jack frame size by looking at the intersection between the expected travel distance and the load.
Model SJ030H will satisfy the expected travel distance. ...OK
-
5. As a compressive load is to be applied, the allowable buckling load is calculated according to the formula (see here). Safety factor sf = 4.
Pcr = 20×104(30.72/775)2 = 295.8kN
sf = 295.8/10.7 > 4 ...OK
6. It is not necessary to consider the input shaft overhang load as it is directly driven by a servomotor with brake.
-
7. Determine the required input speed, using the required screw shaft speed.
N = 10.8 / 0.025×6 = 2592 r/min
Please make sure the units used for the screw shaft speed and screw lead.
(180mm/s --->10.8m/min、25mm --->0.025m) -
8. Check the duty cycle from the time cycle table as follows:
%ED = (3 + 3) / 14×100 = 43%ED
See here to confirm the allowable duty cycle.
From the input rotational speed of 2592 rpm and ambient temperature of 30°C, the allowable duty cycle is 50% ED.
50%ED > 43%ED ...OK
×(Drag to move. )The Linispeed Jack must be used under the surface temperature of gear housing does not exceed 90°C.
The table below shows approximate duty cycles (% ED) when the surface temperature of the gear housing is 90°C or lower. (These values are not guaranteed. )
Please check the surface temperature of the gear housing when you use.
SJ015H
-
9. Calculate the required input shaft torque on the jack.
Required input shaft torque during normal operation:
T = 10.7×1000×0.025 / 2 / π / 6 / 0.87 + 6 = 14.2N・m
For the screw lead, reduction ratio, total efficiency, and Idling torque without load, please refer to each product page.
Please consider the total efficiency on each input rotation speed. Pay attention to the unit of screw lead. (25mm --->0.025m)
Required input shaft torque during start:
T' = 10.7×1000×0.025 / 2 / π / 6 / 0.65 + 6 = 16.9N・m
For more details regarding starting efficiency, please refer to each product page.
-
10. Calculate the required input shaft torque from the servomotor with brake to drive two jacks.
Required torque on the servomotor:
Tm = 14.2×2 = 28.4N・m
Required starting torque required on the servomotor:
T'm = 16.9×2 = 33.8N・m
When selecting the servomotor, please consider a model with brake that satisfies 3000 rpm rated rotation speed, 28.4 N·m rated torque, and required starting torque.
Reference )Required capacity on servomotor
P = 28.4×3000 / 9550 ≒ 9kW
-
11. Two jacks are aligned, twice the torque of a single jack is applied to the input shaft of the jack on the driven side.
Please make sure that jack input shaft torque does not exceed the allowable input shaft torque for SJ030H.Torque for two jacks = 16.9 + 16.9 < 65N・m ...OK
-
12. Jack Options
Shaft end (End fitting ) --->With table type end fitting
Small amounts of dust --->Bellows (special specifications) as necessary
-
13. Based on the above, Linispeed Jack SJ030H-TCT6M is selected.