Technical Data Linear actuator Power Cylinder Handling
Cautions for selecting (Eco Series CDS Type )
- ・No anti-rod rotation mechanism is attached to a cylinder with standard specifications. To use the end part freely, select the anti-rod rotation specifications (option).
And when a magnetic sensor (option) is equipped, anti-rod rotation specifications are required. - ・Refer to the allowable number of starting times table (click here) to check that the number of the starts of selected cylinder is within the allowable range.
- ・If this cylinder is used for press or pull contact stopping, the strength of the equipment side must be 300% or more of the rated thrust.
- ・Structurally, this power cylinder is an indoor type. Since there are problems, such as rust formation, store in a good indoor environment. Pay sufficient attention to humidity. Be aware that if it is installed in a place where the temperature changes rapidly, condensation will occur, causing failure or rust.
- ・Do not store or use in a corrosive atmosphere. Also, it cannot be used in a flammable atmosphere.
- ・Do not use in a place where there is no expectation for heat dissipation, such as in a closed container because doing so will cause failure.
Cautions for installation (Eco Series CDS Type )
- ・Install the main body using a trunnion or a flange mount. When it is used with oscillation using a trunnion mount, select an I-type or an U-type end fitting.
- ・If a lateral load is applied, provide a guide so as not to receive the direct lateral load or the bending moment.
- ・It can be installed either horizontally or vertically when mounting with a trunnion mount.
- ・When it is installed with a flange mount, install it in the vertical direction. (Refer to the figure at the right. )
- ・When it is used horizontally for a long stroke, support the bottom part of the frame end as shown in the right figure. At this point, do not fix the frame and the supporting base.
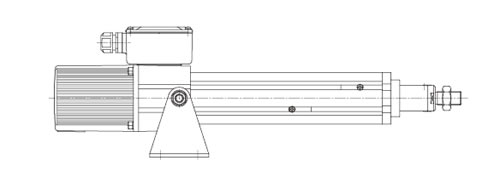
Trunnion mount
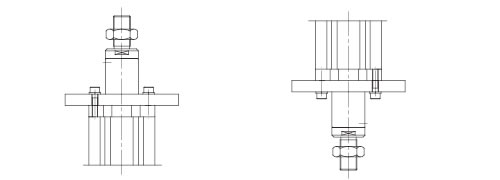
Flange mount
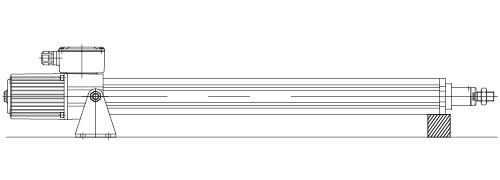
Frame end support (Do not fix. )
Cautions for use (Eco Series CDS Type )
- ・The motor stops when press or pull contact stops, however, on-the terminal block electricity is still being conducted. Never fail to cut off the main power source before working with the terminal box open.
- ・When adjusting the stroke manually, remove the cap bolt of the opposite load side of the motor, and turn the manual shaft with a flat-blade screwdriver or the like. However, use this only as an emergency since it is an operation with the brake working. And when operating manually, make sure to remove the load.
- ・Never use an inverter. This cylinder controls the press contact force by detecting overcurrent with the built-in CDS inside the terminal block and stopping the motor. If an inverter is used, the CDS circuit may be broken.
- ・Megger testing is prohibited for this cylinder. It may break the built in CDS. Remove all the terminals in the terminal block for megger testing of external circuits.
- ・Ensure the change over between extend and retract are at an interval of 0.2 seconds or more.
- ・The temperature around the motor may rapidly increase during operation and immediately after stopping. Do not touch around the motor part.
Reference circuit diagram
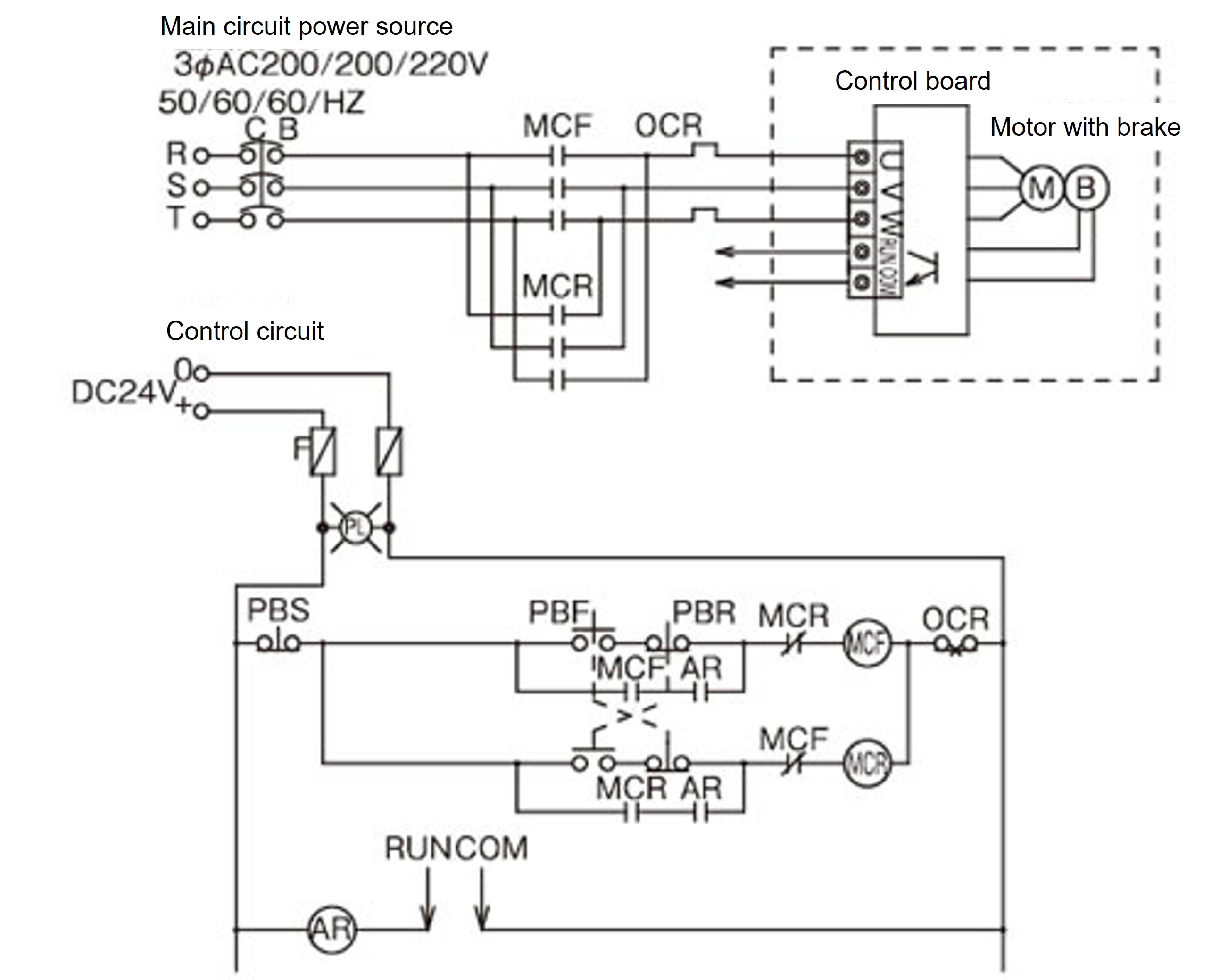
NOTE:
- 1.This is a single acting circuit diagram. In this circuit diagram, both straight and parallel are extended by PBF.
- 2.The cylinder extends with the PBF and automatically stops with the press contact force at the stroke end or when hitting a wall in the middle of a stroke, etc. For retract, the cylinder retracts with the PBR and stops in the same manner as the extend side. Provide a circuit for allowing MCF and MCR to be turned OFF every time the cylinder stops.
- 3.RUN and COM terminals can take out the output signal of the cylinder action.
Open collector output MAX.50mA DC30V
Use a coil current of 50mA DC or less for the relay AR. - 4.Use an electromagnetic contactor with a contact capacity of SC-0 made of a Fuji Electric or equivalent.
- 5.Brake/motor current value (Brakes are internally wired. )
Model No. Rated motor current value (A) Locked motor current value (A) 200V 50Hz 200V 60Hz 220V 60Hz 200V 50Hz 200V 60Hz 220V 60Hz LPE025HT(HK) 0.6 0.6 0.6 1.0 0.9 1.0 LPE050LT(LK) 0.6 0.6 0.6 1.0 0.9 1.0 LPE050HT(HK) 1.1 1.1 1.1 2.1 1.9 2.1 LPE100LT(LK) 1.2 1.3 1.2 2.1 1.9 2.1
Note) The rated current value includes a brake current value(0.11A) and is for the motor terminal blocks U’s or W’s. So, the current value is different from that on the motor nameplate.