Technical Data Drive chain Roller Chain Selection
2.Service Factors
Multi-strand coefficient
The load borne by multi-strand roller chain is unequal across the width of the chain, and thus it cannot be expected that the transmission capacity will be equal to the capacity of a single-strand roller chain multiplied by the number of strands.
For this reason, the transmission capacity of multi-strand roller chain is obtained by multiplying the transmission capacity of single-strand roller chain by a multi-strand factor.
Number of roller chain strands | Multi-strand coefficient |
---|---|
Double-strand | 1.7 |
Triple-strand | 2.5 |
Quadruple-strand | 3.3 |
Quintuple-strand | 3.9 |
Sextuple-strand | 4.6 |
Service factor Ks
The kW ratings are based on conditions of minimal load fluctuation. Depending on the degree of load fluctuation, it may be necessary to correct the kilowatt ratings using the service factor Ks.
Use Table 2 below to determine the appropriate service factor based on the type of machine and the source of power.
The design kW value is obtained by multiplying the kilowatt ratings by the service factor.
Type of impact | Example of machine used | Motor type | ||
---|---|---|---|---|
Motor or turbine | internal combustion engine | |||
With hydraulic drive | Without hydraulic drive | |||
Smooth | Belt conveyors with little load fluctuation, chain conveyors, centrifugal pumps, centrifugal blowers, ordinary textile machines, and ordinary machines with little load fluctuation. | 1.0 | 1.0 | 1.2 |
Moderate | Centrifugal compressors, marine engines, conveyors with moderate load fluctuation, automatic furnaces, dryers, pulverizers, general machine tools, compressors, general construction machines, general paper mill machines. | 1.3 | 1.2 | 1.4 |
Large | Presses, crushers, construction and mining equipment, vibration machines, oil well rigs, rubber mixers, rolls, roll gangs, general machines with reverse or large-impact loads | 1.5 | 1.4 | 1.7 |
RPM factor Kn and number of teeth factor Kz
Table 3 RPM factor Kn and number of teeth factor Kz
Speed r/min | RPM Kn |
---|---|
Less than 27 | 1.00 |
27 or more, less than 37 | 1.03 |
37 or more, less than 50 | 1.07 |
50 or more, less than 70 | 1.10 |
70 or more, less than 100 | 1.14 |
100 or more, less than 150 | 1.19 |
150 or more, less than 300 | 1.27 |
300 or more, less than 500 | 1.34 |
500 or more, less than 1000 | 1.44 |
1000 or more, less than 2000 | 1.54 |
2000 or more, less than 4000 | 1.65 |
Number of teeth | Number of teeth factor Kz |
---|---|
9 or more, less than 12 | 1.16 |
12 or more, less than 15 | 1.14 |
15 or more, less than 18 | 1.12 |
18 or more, less than 24 | 1.10 |
24 or more, less than 30 | 1.08 |
30 or more, less than 38 | 1.06 |
38 or more, less than 47 | 1.04 |
47 or more, less than 60 | 1.02 |
60 or higher | 1.00 |
Shock factor K
This coefficient is determined by the ratio of the converted moments of inertia between the prime mover and the load on the same shaft (ratio of I, GD2), and the amount of backlash in the transmission device.
When the inertia ratio R is greater than 10, use R = 10. When the inertia ratio R is less than 0.2, use R = 0.2.
If I or GD2 of the prime mover or load is unknown, use the value of R in Figure 1.
Fig. 1 Shock factor K
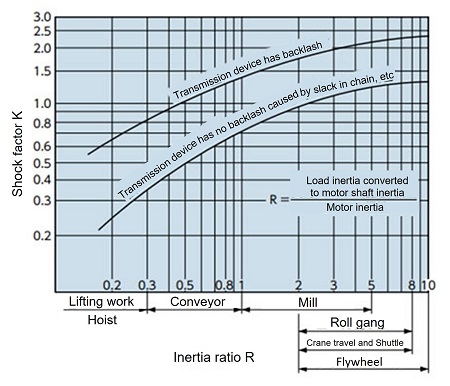
Imbalance load factor Ku
When using two or four chains for lifting or shuttle traction drive, the chain load will not be uniform.
This must be accounted for by multiplying the following imbalance load coefficient Ku to adjust the left-and-right load imbalance.
(ex. ) For four lifting strands, the imbalance load factor for one strand
Ku = 0.6 × 0.6 = 0.36
two | 0.6 |
---|---|
four | 0.36 |