Technical Data Cable Carriers (CABLEVEYOR) - Cable carrier selection - Selection of cable carrier steel series
Selection of cable carrier steel series
TK Series/TKH Series
Determine cable carrier model by cable/hose installing space
For TK Series and TKH Series, the stay bores (D) are drilled to the specified dimensions.
Calculate the minimum required width B′of the stay based on the outer diameter/number of cables and hoses, and select a stay with a stay width B ≥ B′.
■Stay dimensions
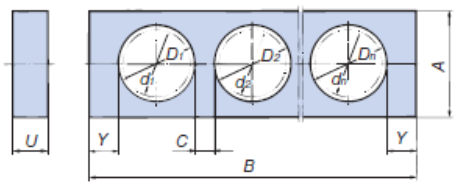
・Calculate stay bore diameter
D:Stay bore diameter ( Φ 8 or larger integer value) d:Cable/hose outer diameter
・Calculate minimum required stay width
B':Minimum required stay width C:4 mm or larger Y:Table on the right
Size | Minimum value of Y |
---|---|
TK070 | 10 |
TK095 | 15 |
TK130 | 18 |
TK180 | 18 |
TKH250 | 25 |
※Refer to the product pages for stay dimensions.
・Select stay
Select dimensions A and B from the results calculated by the aboves and the stay dimensions in the models.
Install the stays every 2 links starting from the second link on the moving end side.
■Unsplit and split stays
TK Series and TKH Series cable carriers have two types of stays: unsplit stays and split stays. Split stays have one end that can be easily removed so that supported materials can be easily added and removed. Split stays are convenient for when there are hoses with sleeves and the movement distance is long and also when there are many supported materials.
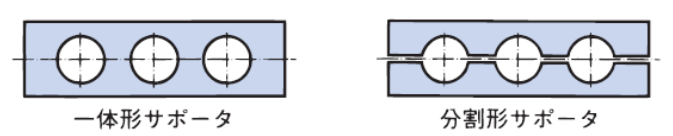
TKS Series
■Frame
Decide the number of dividers by the minimum required or more and by ensuring that one cable or hose goes through one opening if possible. Lay out the cables and hoses by also taking into consideration the distribution of mass across the cable carrier.
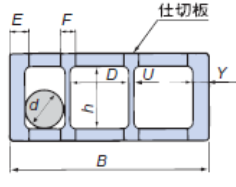
Calculate the minimum required width B′ of the frame based on the outer diameter/number of cables and hoses, and select a frame with a stay width B ≥ B′.
・Calculate the required inner width
D:Required inner width (Round up decimals) d:Cable/hose outer diameter
・Calculate minimum required frame width
B':Minimum required frame width U:Divider thickness Y:Link thickness
・Select the frame
Select the frame from the results calculated by the aboves and frame dimension B in the models.
Number of frames and dividers
Install frames every 2 links.
Number of dividers (m) = n × (number of dividers installed in 1 location)
Size | B | h | Y | U | E | F | Cable/hose maximum diameter d |
---|---|---|---|---|---|---|---|
TKS070 | 100 150 200 | 31 | 10 | 3 | 15 | 13 | 27 |
TKS095 | 46 | 12 | 4 | 17 | 14 | 42 |
Size | Minimum required number of dividers | ||
---|---|---|---|
B=100 | B=150 | B=200 | |
TKS070 | 0 (5) | 1 (8) | 2 (12) |
TKS095 | 0 (4) | 1 (7) | 2 (11) |
Figure in ( ) is the maximum number installable.
Bending radius R/strength selection
Select using the load diagram
The travel length S on the load diagram is applicable when the fixed end of the cable carrier is installed in the center position (middle) of the travel length.
Based on the models on the load diagram, select the strength from the travel length, cable/hose mass, cable/hose outer diameter, and cable/hose allowable bending radius.
Selection example :Selecting TKC Series
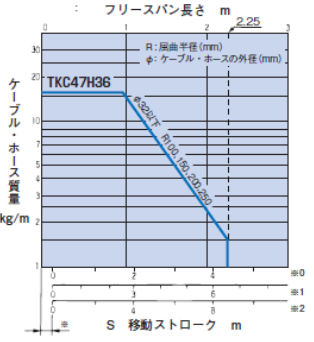
Usage conditions
Travel length :3m
Cable/hose mass :4kg/m
Cable/hose outer diameter :Φ20mm(one )
Cable/hose allowable bending radius :160mm
In the table to the left, find the intersection of horizontal axis 3 m and vertical axis 4 kg/m. Select the TKC47H36 as the product that satisfies this point.
Cable/hose allowable bending radius (r) < Cable carrier bending radius (R)
Decide on R = 200 that satisfies these conditions. Therefore, TKC47H36W80R200 is the product from the above conditions.
Confirm speed and acceleration
The allowable travel speeds for each model and installation method are shown below. Confirm that the operating conditions do not exceed the allowable values. (Contact a Tsubaki representative if the allowable values are accidentally exceeded.)
TKP | TKC | TKMK/ TKMT |
TKR | TKQ | TK | TKH | TKS | TKI | TKV | |
---|---|---|---|---|---|---|---|---|---|---|
Standard | 300 | 300 | 300 | 300 | 600 | 60 | 60 | 60 | 120 | 150 |
Support Rollers | 150 | 150 | 150 | 150 | 150 | 60 | 60 | 60 | - | - |
Support plate | - | 60 | - | - | - | - | - | - | - | - |
Horizontal | 60 | 60 | 60 | - | - | 30 | 30 | 30 | - | - |
Vertical arrangement (hanging) | 300 | 300 | 300 | 300 | 600 | 60 | 60 | - | - | - |
Vertical arrangement (standing) | 300 | 300 | 300 | 300 | 600 | 60 | 60 | - | - | - |
Bottom movement | 300 | 300 | 300 | 300 | 600 | 60 | 60 | 60 | - | - |
Combination | 300 | 300 | 300 | 300 | 600 | 60 | 60 | 60 | - | - |
Gliding arrangement | * | * | * | - | - | - | - | - | - | - |
Traveling roller | - | - | - | - | - | 30 | - | - | - | - |
Vertical circular travel arrangement | 60 | - | - | - | - | 60 | - | - | - | - |
Horizontal circular travel arrangement | 30 | 30 | - | - | - | 30 | - | - | - | - |
※Refer to the catalog for gliding arrangement (* mark).
※– means not applicable.
※Contact us for TKUA series.
TKP | 2G |
---|---|
TKC | 3G |
TKR | 2G |
TKQ | 4G |
TK | 1m/sec2 |
TKS | 1m/sec2 |
TKH | 1m/sec2 |
TKI,TKV | 3G |
TKMK,TKMT | Contact a Tsubaki representative |
If acceleration is extremely large, the service life may be reduced in a very short amount of time. Confirm that the operating conditions do not exceed the values in the above table. (Contact a Tsubaki representative if the allowable values are accidentally exceeded.)
-Reference - TKMK Series, TKMT Series Bending radius, Cross-sectional dimension comparison
Bending radius and inner width dimension may differ between open type and closed type. Refer to the table below.
Size | Bending radius | Inner width | Inner height |
---|---|---|---|
TKMK47H28 | 55, 75, 100, 160, 200, 250 | 24, 56, - , 104, 152, 192 | 28 |
TKMT47H26 | - , 75, 100, 160, 200, 250 | - , 56, 80, 104, 152, 192 | 26 |
TKMK65H42 | 75, 95, 115, 145, 220, 300 | 66, 106, - , 154, 194, 258 | 42 |
TKMT65H38 | - , 95, 115, 145, 220, 300 | 66, 106, 130, - , 194, 258 | 38.5 |
TKMK95H58 | 140, 170, 200, 290, 380 | 114, - , 162, 210, 258, 306, 402, 514 | 58 |
TKMT95H54 (Plastic cover type ) | 140, 170, 200, 290, 380 | 114, 130, 162, - , 258, 306 | 54.5 |
TKMT95H54 (Aluminum cover type ) | 140, 170, 200, 290, 380 | 100-400 (every 1 mm) | 54.5 |
TKMK125H72 | 180, 220, 260, 340, 380, 500 | - , 151, - , 247, 359, 407, 455, 503 | 72 |
TKMT125H68 | - , 220, 260, 340, 380, 500 | 135, - , 183, 247 | 68.5 |