Technical Data Linear actuator Power Cylinder Handling
Eco Series Servo Type Servomotor mounting procedures (when installed by customer )
Motor direct coupling
Prepare a servomotor. (An output shaft with/without keyway can be used. )
Set the servo motor with the coupling mounting hole of the motor flange facing upward. (□45 and □105 frames only )
Cleanly wipe away rust, dust, antirust oil, etc., of the motor shaft.
Loosen the clamp bolt of the coupling.
Remove the plug of the coupling case, turn the input shaft and set the clamp bolt head of the coupling to the position of the plug hole.
*For LPES30, there is a need to insert a torque wrench at an angle as shown below.
Smoothly insert the motor shaft to the coupling.
*If the motor is turned in the direction of rotation, the phase to the clamp bolt may be shifted.
Pay sufficient attention not to insert the motor shaft in a tilted manner.
After inserting the spigot facing part completely, attach it with the motor attaching bolt.
Using a torque wrench, tighten the clamp bolt of the coupling at the specified tightening torque.
Attach the removed plug to the coupling case.
※For details, refer to the instruction manuals.
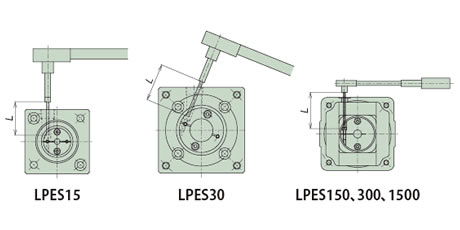
Model No. | Coupling bolt size | Tightening torque N・m{kgf・m} |
L dimensions mm |
---|---|---|---|
LPES15 | M2 | 0.5{0.04} | 30 |
LPES30 | M2.5 | 1.0{0.10} | 40 |
LPES150 | M4 | 3.8{0.39} | 60 |
LPES300 | 70 | ||
LPES1500 | M6 | 12{1.22} | 90 |
With precision planetary reducer
1. When the motor shaft is round
Set the reducer with the motor mounting surface upward.
Cleanly wipe away rust, dust, antirust oil, etc., of the motor shaft.
Remove the plug from the adapter, turn the input shaft, and align the bolt head with the position of the plug hole.
Check that the set bolt has been loosened with a hexagonal spanner, etc.
Smoothly insert the motor shaft in the input shaft hole. At this time, be aware that if the motor shaft is inserted in a tilted manner, galling with the shaft hole, etc., will occur, resulting in failure to mount properly.
After complete insertion of the spigot portion, completely fix the motor to the adapter at an appropriate tightening torque.
Tighten the set bolt of the input shaft with a torque wrench or the like at the tightening torque in the following table. At this time, be aware that if it is tightened at under the specified torque, looseness of the set bolt can lead to problems, such as a slip of the motor shaft. Do not apply Loctite and other anti-loosening agents to the set bolt. Proper tightening torque may not be obtained, resulting in insufficient tightening.
Attach the plug. This completes the motor set up procedure.
Clamp bolt tightening

It is assumed that the clamp fit may slide with an unexpected impact. Give consideration to a separate safety mechanism for elevation drive, etc.
Clamp bolt tightening torque table
Bolt size | M3 | M4 | M5 | M6 | M8 | M10 |
---|---|---|---|---|---|---|
Tightening torque N・m{kgf・m} |
1.9 {0.18} |
4.3 {0.44} |
8.7 {0.89} |
15 {1.50} |
36 {3.70} |
71 {7.20} |
*The bolt tightening torque should be in the range of the above numerical values multiplied by 1.0 ‒ 1.2.
Motor mount bolt tightening torque table
Bolt size | M3 | M4 | M5 | M6 | M8 |
---|---|---|---|---|---|
Tightening torque N・m{kgf・m} |
1.1 {0.11} |
2.5 {0.26} |
5.1 {0.52} |
8.7 {0.89} |
21 {2.10} |
*The bolt tightening torque should be in the range of the above numerical values multiplied by 1.0 ‒ 1.2.
2. Mounting a keyed motor
A keyed motor shaft can be used in clamp type as is the case with a round shaft by removing the key.
Set the motor shaft keyway (D cut), each slit, and set bolt in position as shown in the illustration on the right-hand side.
Other procedures for mounting to the reducer are the same as the round shaft’s case.
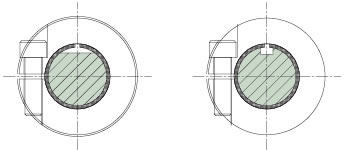
Cautions for selecting (Eco Series Servo Type )
- ・Anti-rod rotation mechanism is not provided with this cylinder. Turning force is generated to the rod owing to the thrust, make sure to perform prevention of rotation on the equipment side.
The turning force placed on the rod at the time of the maximum thrust is as shown in the following table.Model No. LPES15 LPES30 LPES150 LPES300 LPES1500 Rod turning force
N・m{kgf・m}0.16{0.016} 0.32{0.031} 1.60{0.16} 3.19{0.33} 26.6{2.72} - ・Load holding mechanism is not provided with this cylinder in the cylinder main body. If a dangerous situation is anticipated during stoppage and when the product is broken, use a servomotor with a magnetic brake to hold the load, or provide a brake mechanism outside. It is same to use for elevating device or horizontal use and displacement is problem.
- ・Structurally, this power cylinder is an indoor type. Since there are problems, such as rust formation, store in a good indoor environment. Pay sufficient attention to humidity. Be aware that if it is installed in a place where the temperature changes rapidly, condensation will occur, causing failure or rust.
- ・Do not store or use in a corrosive atmosphere. Also, it cannot be used in a flammable atmosphere.
- ・Do not use in a place where there is no expectation for heat dissipation, such as in a closed container because doing so will cause failure.
Cautions for installation (Eco Series Servo Type )
- ・Use a trunnion mount or a flange mount (possible only for LPES150 or smaller) to install the main body.
When used with oscillation, select an I-type or a U-type end fitting. If a lateral load is applied, provide a guide so as not to receive the direct lateral load or the bending moment. - ・It can be installed either horizontally or vertically when mounting with a trunnion mount.
- ・When it is installed with a flange mount, install it in the vertical direction. (Refer to the figure at the right. )
※When considering use of a flange mount for a type of LPES300 or larger, please contact us.
※Flange mounting is not possible with bellows. - ・For use in a static condition without swinging the cylinder, select ① Flange mount or ② Trunnion mount + foot mount. It can be installed either horizontally or vertically. (□ 45 frame only )
- ・When it is used horizontally for a long stroke, support the bottom part of the frame end as shown in the figure below.
At this point, do not fix the frame and the supporting base.

Frame end support
(Do not fix. )
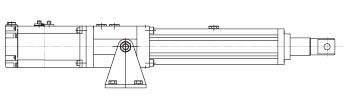
Trunnion mount
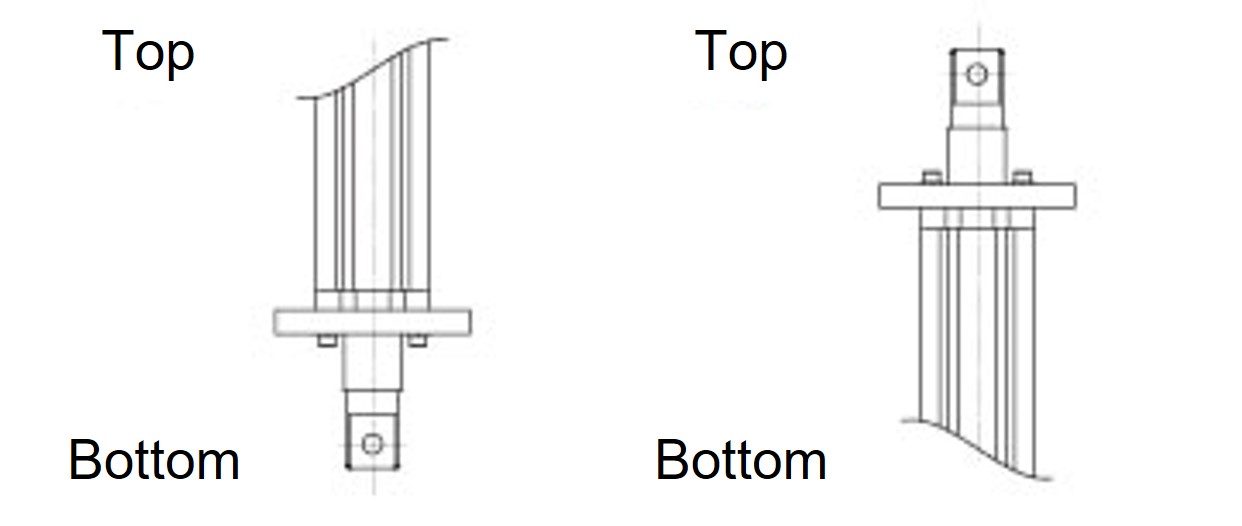
Flange mount
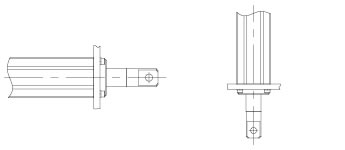
(1)Flange mount
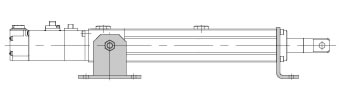
(2)Trunnion mount +foot mount
Cautions for use (Eco Series Servo Type )
- ・Overload protection mechanism is not provided with this cylinder in the cylinder main body, so provide protection against overvoltage, overcurrent, overload of the servo driver (servo amplifier). Additionally, manufacture the opposite side equipment of the power cylinder with a strength sufficient to withstand the maximum torque of the servomotor.
- ・Manual operation shaft is not provided with this cylinder for a structural reason, so adjust the cylinder position by operating the servo driver (servo amplifier) at very low speed.
- ・Daphne Eponex SR No.2 is applied to the screw shaft of this cylinder at the time of shipment, however, periodic lubrication is required.
Refer to the table at the right for the lubrication cycle of grease.
The application amount of the grease is 10 – 15g per stroke of 100mm.
And as grease for maintenance, JWGS100G is available (sold separately) from our company.
(Click here. )※On the rod periphery, apply grease according to the lubrication cycle so that an oily film does not run out.
Use the same grease as the one used for the screw.※Determine the lubrication cycle according to the situation of operation.
Frequency of use Lubrication cycle 1001 times/day or more Every 1 to 3 months 501 to 1000 cycles/day Every 3 to 6 months 101 to 500 cycles/day Every 6 months to 1 year ~100 cycles/day or less Every 1 to 1.5 years
Ideal for maintenance of Linipower Jack and Power Cylinder!
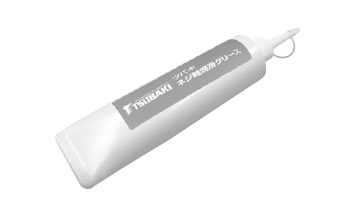
(100g filled )
Model No. :JWGS100G