Technical Data Linear actuator Power Cylinder Selection
Selection :U Series
Conditions required for selection
Machine to be used and application
Thrust or load N{kgf}
Stroke mm
Speed mm/s
Frequency of use cycles /min
Hours of operation per day, and number of operating days per year
Type of load of machine used
Operating environment
Supply voltage 、Frequency
Selection procedure
Determination of model STEP1
Determine the type (UB or UC) according to the application and operation method.
Determination of model No. STEP2
- (1) Calculate annual traveling distance from the stroke, frequency of operation and hours of operation.
Annual traveling distance km = Actual stroke m×Frequency of use /day ×Number of operating days / year ×10-3
- (2) Calculate the operation factor from the characteristics of load and the machine used, referring to Table 1.
- (3) Multiply thrust or load by operation factor to obtain a corrected thrust.
- (4) Determine the frame No. from the “Expected Traveling Distance” shown below on this page according to the corrected thrust and annual traveling distance, and select an applicable model from the standard model list (click here) based on the stroke, speed, power supply voltage and frequency.
Table 1 Service factor
Load characteristics | Example of machine used | Service factor |
---|---|---|
Smooth operation without impact Low inertia |
Damper, opening/closing of valve Conveyor switching device |
1.0~1.3 |
Operation with light impact Medium inertia |
Opening/closing of hopper gate, various transfer equipment, various lifter elevation | 1.3~1.5 |
Operation with large impact/vibration High inertia |
Heavy object conveyance by carriage, buffer for belt conveyor, inversion opening/closing device for large lid | 1.5~3.0 |
Note )The above operation factor table shows general guidelines, and please apply the appropriate factor depending on actual condition.
Characteristics check STEP3
- (1) Use the Power Cylinder within a frequency of operation below (Table 2).
- (2) Check the load time ratio.
- (3) Check the coasting distance and stop accuracy in Table 3 below.
Table 2 Allowable frequency of operation
Series name/type | LPUB・LPUC | |||||||
---|---|---|---|---|---|---|---|---|
Motor Capacity (kW) | 0.75 | 1.5 | 2.2 | 3.7 | 5.5 | 7.5 | 11 | 15 |
Thrust ・Speed | 6000S | 6000L | 6000M | 6000H | ||||
8000S | 8000L | 8000M | 8000H | |||||
12000L | 12000M | 12000H | ||||||
16000L | 16000M | 16000H | ||||||
22000L | 22000M | 22000H | ||||||
32000L | 32000M | 32000H | ||||||
50000L | 50000M | 50000H | ||||||
cycles (Number of times/min ) | 4 | 4 | 4 | 4 | 3 | 3 | 2 | 2 |
Percentage duty cycle (%ED) | 25%ED |
Note) The above frequencies of operation are values determined by heat generation of the motor. They are not values taking life of the cylinder body into consideration.
Allowable frequency of operation for the Power Cylinder U series is within a range which satisfies the number of starting times and load time ratio in the above table. The load time ratio is expressed by the following equation.
Percentage duty cycle (%ED) = Operation time of one cycle Operation time of one cycle + stop time ×100%
Table 3 Coasting distance and stop accuracy (Reference )
Installation method | Brake internal connection | Brake external connection ※ | |||||||
---|---|---|---|---|---|---|---|---|---|
Lifting load | Suspended load | Lifting load | Suspended load | ||||||
Model No. | Coasting distance | Stopping Precision | Coasting distance | Stopping Precision | Coasting distance | Stopping Precision | Coasting distance | Stopping Precision | |
LPUB6000
LPUC6000 |
S | 0.6 | ±0.2 | 0.8 | ±0.2 | 0.5 | ±0.1 | 0.6 | ±0.1 |
L | 2.7 | ±0.6 | 4.4 | ±1.2 | 1.8 | ±0.4 | 3.4 | ±0.9 | |
M | 4.5 | ±1.0 | 7.4 | ±2.0 | 2.7 | ±0.5 | 5.5 | ±1.5 | |
H | 7.6 | ±1.7 | 12.2 | ±3.2 | 4.6 | ±0.9 | 9.0 | ±2.4 | |
LPUB8000
LPUC8000 |
S | 1.9 | ±0.4 | 2.9 | ±0.7 | 1.3 | ±0.2 | 2.2 | ±0.5 |
L | 3.6 | ±0.8 | 5.8 | ±1.6 | 2.2 | ±0.4 | 4.3 | ±1.1 | |
M | 5.6 | ±1.2 | 8.4 | ±2.1 | 3.4 | ±0.7 | 6.1 | ±1.5 | |
H | - | - | - | - | 5.4 | ±1.0 | 8.7 | ±2.0 | |
LPUB12000
LPUC12000 |
L | 2.1 | ±0.5 | 3.0 | ±0.8 | 1.3 | ±0.2 | 2.2 | ±0.5 |
M | 3.5 | ±0.8 | 5.1 | ±1.3 | 2.1 | ±0.4 | 3.6 | ±0.9 | |
H | - | - | - | - | 3.6 | ±0.7 | 5.9 | ±1.4 | |
LPUB16000
LPUC16000 |
L | 2.8 | ±0.6 | 4.0 | ±1.0 | 1.7 | ±0.3 | 2.8 | ±0.7 |
M | - | - | - | - | 2.6 | ±0.5 | 4.0 | ±0.9 | |
H | - | - | - | - | 3.9 | ±0.7 | 8.6 | ±2.4 | |
LPUB22000
LPUC22000 |
L | - | - | - | - | 1.3 | ±0.3 | 2.0 | ±0.4 |
M | - | - | - | - | 2.0 | ±0.4 | 4.2 | ±1.0 | |
H | - | - | - | - | 2.7 | ±0.5 | 4.4 | ±1.1 | |
LPUB32000
LPUC32000 |
L | - | - | - | - | 1.3 | ±0.3 | 2.0 | ±0.4 |
M | - | - | - | - | 2.0 | ±0.4 | 4.2 | ±1.0 | |
H | - | - | - | - | 2.7 | ±0.5 | 4.4 | ±1.1 | |
LPUB50000
LPUC50000 |
L | - | - | - | - | 1.3 | ±0.3 | 2.0 | ±0.4 |
M | - | - | - | - | 2.0 | ±0.4 | 4.2 | ±1.0 | |
H | - | - | - | - | 2.7 | ±0.5 | 4.4 | ±1.1 | |
※Click here for the wiring of the brake external connection.
Type of load
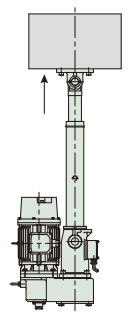
Lifting load
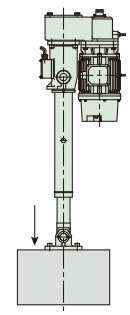
Suspended load
Vertical operation
Note) Anti-rod rotation is required for actual operation.
Coasting distance :This indicates a distance from a time when the limit switch or the stop button is operated until the cylinder stops. This coasting distance varies depending on how the load is applied and the operation circuit.
Stopping Precision :This indicates variation of the stop position when stop is repeated.
Guide for life
Use the traveling distance of the cylinder (nut) as guide to select the Power Cylinder U series with expected life.
Traveling distance of cylinder (nut)
The life of a ball screw is determined by flaking of the rolling surface caused by its fatigue. Check the rough life with this chart of expected traveling distance.
However, in case of great impact or where lubrication or maintenance is not performed properly, the expected traveling distance becomes substantially shorter.
Expected traveling distance (km) = Actual load stroke (m)×Frequency of use (/day )×Number of operating days / year ×10-3×Expected number of years
The chart on the right-hand side is based on L10 life. L10 life expresses in traveling distance a life that can be reached by 90% or more of all ball screws. If you select a power cylinder based on the life, select model No. from this chart.
If the load greatly fluctuates in the middle of stroke, calculate the equivalent load (PM) by the following formula.
PM = PMIN + 2×PMAX 3
PM:Equivalent load N{kgf}
PMIN:Minimum load N{kgf}
PMAX:Maximum load N{kgf}
For further expected traveling distance, please consider the N version (click here).
Expected traveling distance
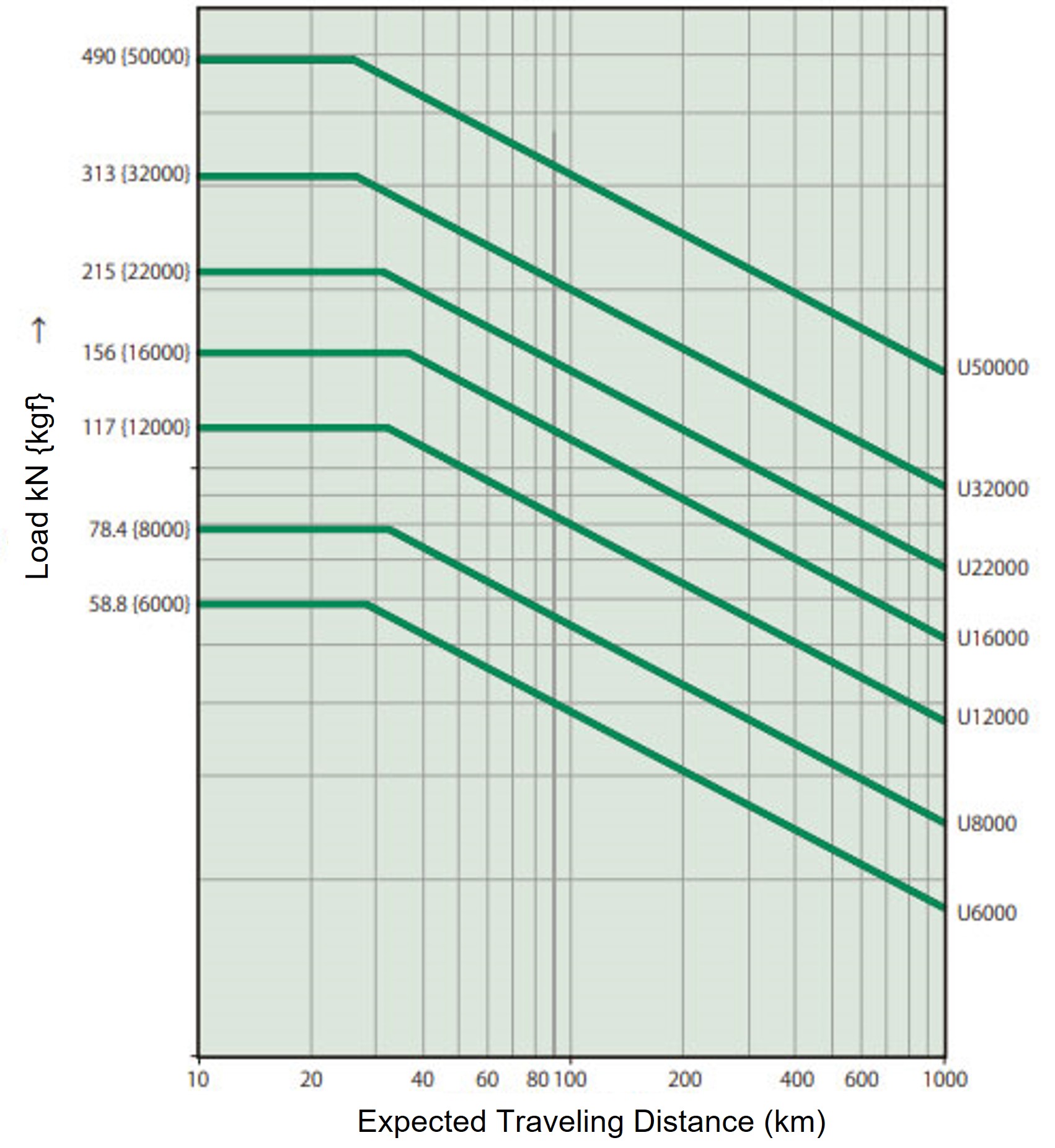
Selection example
Operation method :Hopper gate open/close (Stop at middle two points, press and stop at extend limit and retract limit )
Required thrust :41.2kN{4200kgf}
Stroke :1000mm
Speed :1000mm/s in approximately 45 seconds
Frequency of use :One reciprocation/60 minutes (1 reciprocation/hour )
Operating hours :8 hours/day, 250 days operation/year Durable years approximately 5 years
Load characteristics :Operation with light impact, loaded when extend and retract
Operating environment :Outdoor installation, dusty, temperature 0℃ to 35℃
Power Supply :220V 60Hz
Determination of type
With press and stop, internal stop → Select C type
Determination of model No.
- 1.Service factor :1.3
- 2.Corrected thrust :41.2kN{4200kgf}×1.3 = 53.6kN{5460kgf}
- 3.Model No. : LPUC 6000 L10 K2 J
K2...Stop at two middle points
J......With Bellows (Much dust )
Characteristics check
- 1.cycles
- cycles :2 times/60min<4 times/min
- Percentage duty cycle :
1000mm 22mm/sec ※ ×2 times (1 reciprocation) 60 min ×60sec ×100 = 2.5% < 25%※Speed calculation 1000mm / 45sec = 22mm / sec
- 2.Number of total press (pull) stop times:2 times/1 reciprocation, durable years: 5 years (250 days/year)
- 2×1×8×250×5=2 x 104 times<10 x 104 times
Life check
- 1.Annual traveling distance :1.0×2×1 time /Time ×8 hours / day ×250 days / year ×10-3 = 4km
- 2.Expected traveling life :4km×5 years = 20km
- 3.Equivalent load :PM = 53.6 + 2×53.6 3 = 53.6kN{5460kgf}
※This calculated value satisfies the expected traveling life of LPUC 6000 according to the above load-expected traveling life diagram.
Cautions for selecting :U Series
Brake holding force
Load holding force while the Power Cylinder U series stops is more than the rated thrust, therefore, power cylinder can hold the load more than rated thrust. This holding force is generated by brake motor. The brake is of a spring braking type that performs braking operation by spring force during stoppage, and brake torque has 150% or more of the motor rated torque.
※Select a power cylinder of a sufficient thrust, allowing for a safety rate so that the loads used (static and dynamic) do not exceed the rated thrust.
Stoppage by Brake
This method operates and stops the brake by the limit switch or operation of the stop button, and allows for positioning on multi-stages such as the upper limit, lower limit and middle of the stroke. Coasting distance and stop accuracy vary depending on operating speed and load.
When accurate positioning is required, or operation speed is high, brake individual turnoff is recommended. Take coasting distance to set the limit switch position and the output stop signal.
Reference values are shown in Table 3 above.
Allowable number of pressing stops for C type
When push/pull stopping at high frequency
When using the Power Cylinder at a frequency of ten or more times a day, refer to the total stop times for every type in the following table.
Type | LPUC6000~LPUC32000 | ||
---|---|---|---|
Speed | S,L | M | H |
Reference total stop numbers (×104 times) | 10 | 3 | ※ |
- Note)
1.When the Power Cylinder is used for push (pull) stopping, brake external wiring is recommended. - 2.When the Power Cylinder is used more frequent turn in above table, it is recommended to stop with the stroke adjusting LS.
- 3.When the Power Cylinder is used with press (pull) stop, strength of the mating equipment shall be 250% or more of the rated thrust.
- 4.When the power cylinder is stopped, use an inverter to decelerate.
※Since life is affected by the amount of deflection of the disk spring, the more it is decelerated, the more the standard total number of stops can be increased.
Example: If the power cylinder is used at H speed, the standard total number of stops is up to 100,000 stops if it is stopped at a speed equivalent to S speed.Contact us for details. - 5.UC50000 cannot use the push (pull) stop in permanent use.
Allowable mass for horizontal drive
The safety device will not work at the start for opening/closing of the damper or the hopper gate, normal reverse, inclination and elevation, however, when a load inertia is large due to horizontal movement of carriage, the safety device may work to impair smooth operation at the start. For the allowable mass m of each model, see Table 4.
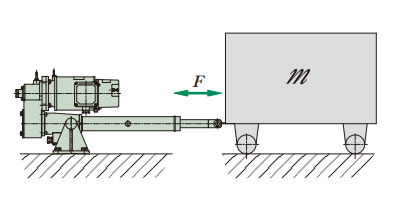
- Trolley mass :mkg
- Coefficient of friction :μ
- Trolley traveling resistance := μm ≦ Rated Thrust
Table 4 Allowable mass m
Power cylinder model | LPUB6000 LPUC6000 |
LPUB8000 LPUC8000 |
LPUB12000 LPUC12000 |
LPUB16000 LPUC16000 |
LPUB22000 LPUC22000 |
LPUB32000 LPUC32000 |
LPUB50000 LPUC50000 |
|
---|---|---|---|---|---|---|---|---|
Speed | L | 42000 | 51000 | 170000 | 204000 | 305000 | 680000 | 960000 |
M | 35000 | 40000 | 123000 | 160000 | 230000 | 490000 | 1080000 | |
H | 25000 | 32000 | 74000 | 100000 | 307000 | 670000 | 720000 |
Note) No consideration required at low (s) speed.
Multiple operation
As shown in Fig. 1, transfer or elevation can be carried out by sharing load on multiple power cylinders with less speed fluctuation due to variation in load.
For selection, please read carefully on the right.
Fig. 1 Linkage operation by multiple power cylinders
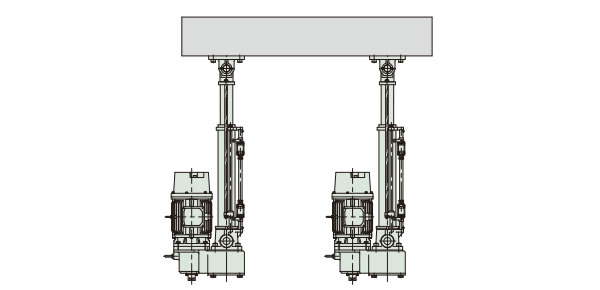
Control method
Turn on the power for all of the cylinders at same time, and stop with the limit switches installed on each power cylinder. Avoid using a single limit switch to control all of cylinders, as this will result in a cumulative error in stroke.
Accuracy
Variation in speed of each power cylinder during operation is generated due to variation in load, and is generally approximately 5%. For variation at stop, refer to the stop accuracy in Table 3 above. When synchronizing power cylinders, use the multi-series.
Thrust per one cylinder Required thrust N{kgf} Number of power cylinders to be used ×Multiple factor
Table 5 Multiple factor
Number of power cylinders to be used | 2 cylinders | 3 cylinders | 4 cylinders | 5 cylinders | 6 cylinders |
---|---|---|---|---|---|
Multiple factor | 0.8 | 0.7 | 0.6 | 0.55 | 0.5 |