Technical Data Linear actuator Power Cylinder Selection
Selection :T Series ・Multi Type
Conditions required for selection
Machine to be used and application
Thrust or load N{kgf}
Stroke mm
Speed mm/s
Frequency of use cycles /min
Hours of operation per day, and number of operating days per year
Type of load of machine used
Operating environment
Selection procedure
- 1.Determine the type (B or C) according to the application.
- 2.Calculate the operation factor from the characteristics of load and the machine used.
- 3.Calculate annual traveling distance from the stroke, frequency of operation and hours of operation.
Annual traveling distance km = Actual stroke m×Frequency of use /day ×Number of operating days / year ×10-3
- 4.If the load greatly fluctuates in the middle of stroke, calculate the equivalent load by the following formula.
PM = PMIN + 2×PMAX 3
PM:Equivalent load N{kgf}
PMIN:Minimum load N{kgf}
PMAX:Maximum load N{kgf}
- 5.Multiply equipment maximum load by operation factor, and for multiple operation, divide by multiple factor and number of multiple units to obtain corrected thrust.
Corrected thrust = Equipment maximum load ×Service factor Number of multiple units ×Multiple factor
- 6.Select model No. to be used from the standard models based on the corrected thrust and stroke.
- 7.Calculate life from the load-expected traveling distance diagram and compare it with the annual traveling distance to check the life.
Service factor
Load characteristics | Example of machine used | Service factor |
---|---|---|
Smooth operation without impact Low inertia |
Damper, opening/closing of valve Conveyor switching device |
1.0~1.3 |
Operation with light impact Medium inertia |
Opening/closing of hopper gate, various transfer equipment, various lifter elevation | 1.3~1.5 |
Operation with large impact/vibration High inertia |
Heavy object conveyance by carriage, buffer for belt conveyor, inversion opening/closing device for large lid | 1.5~3.0 |
Note )The above operation factor table shows general guidelines, and please apply the appropriate factor depending on actual condition.
Multiple factor
Number of multiple units ( units ) | 2 | 3 | 4 | 5 | 6 |
---|---|---|---|---|---|
Multiple factor | 1.0 | 1.0 | 1.0 | 0.8 | 0.67 |
Note) Number of multiple units is up to six units.
Load - expected traveling distance
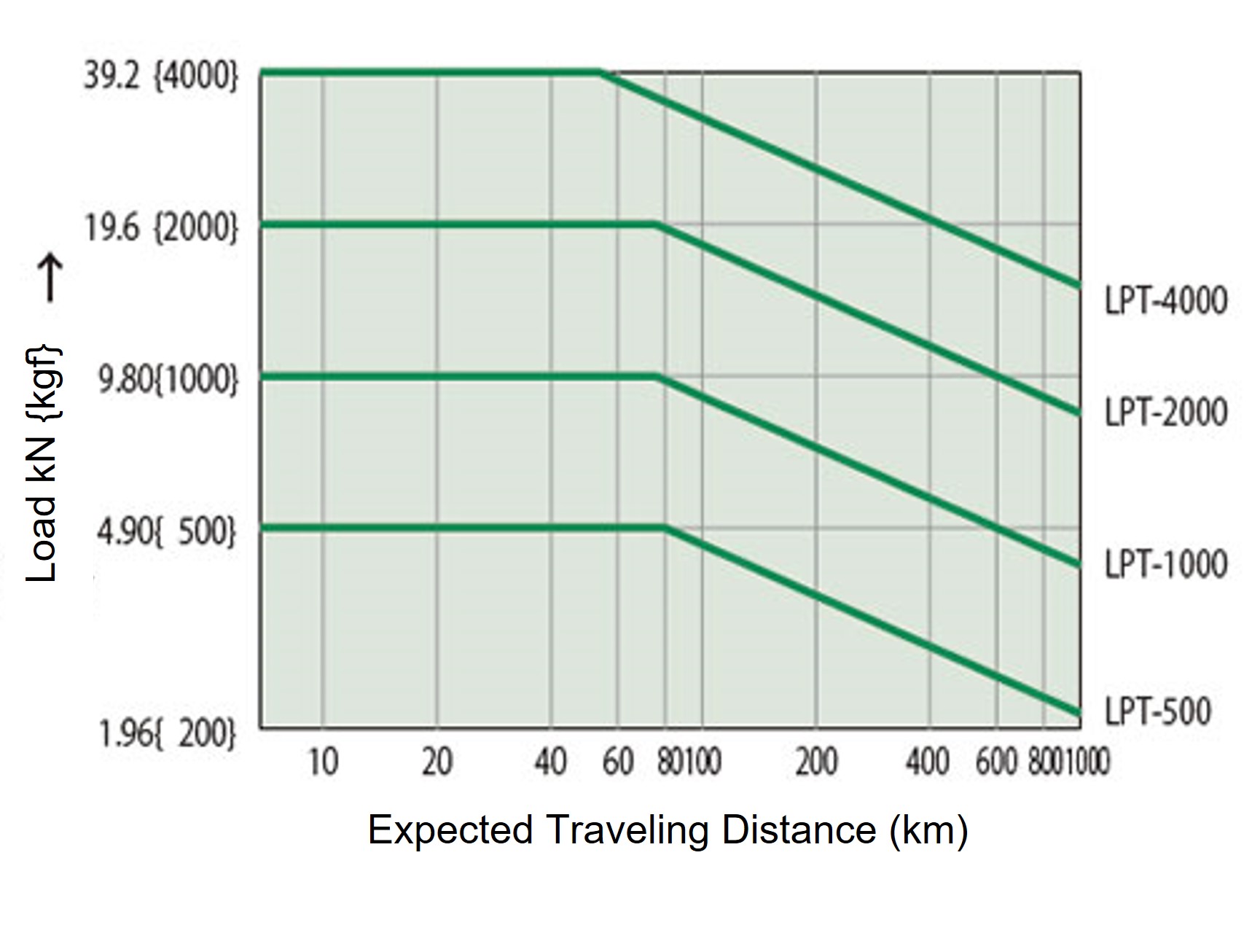
The expected traveling distance has been calculated from L10* life.
※L10 life is a life which 90% or more of a group of the same ball screws which are operated under the same condition expire without flaking.
Selection of driving source :T Series ・Multi Type
As a driving motor, motors with a speed reducer, DC motors, servo motors or ball change motors are available. The motor to be used rotates in reverse by load because the Power Cylinder is highly efficient. Make sure to use a motor with a brake. Use a brake of a spring close type and with brake torque 150% or more.
Select a driving motor according to the following equation.
Calculate necessary input torque and use a motor which satisfies the calculated torque value.
For specifications of the Power Cylinder, refer to the major specifications page for each product.
T = W×ℓ 2×π×R×η×1000 + To
T:Necessary input torque N・m{kgf・m}
W:Load (Load ) N{kgf}
ℓ:Screw lead mm
R:Gear Ratio = 2
η:Total Efficiency = 0.855
To:Idling torque without load N・m{kgf・m}
Note) Note that, if any motor of a larger capacity than necessary is used, when it is locked in the course of the stroke, impact load acts on the Power Cylinder due to rotation energy of the motor, resulting in breakage. Wire connection should be carried out according to brake external connection.
Cautions for selecting :T Series ・Multi Type
Allowable number of press (pull) stop times
When push/pull stopping at high frequency
When using the Power Cylinder at a frequency of ten or more times a day, refer to the total stop times for every type in the following table.
Type | LPTC500 ~ LPTC4000 | ||
---|---|---|---|
Speed (mm/s) |
LPTC500 | ~30 | ~60 |
LPTC1000 | ~30 | ~60 | |
LPTC2000 | ~30 | ~60 | |
LPTC4000 | ~30 | ~42 | |
Reference total stop numbers (×104 times ) |
30 | 10 |
- Note)
1.When the Power Cylinder is used for push (pull) stopping, brake external wiring is recommended. - 2.When the Power Cylinder is used more frequent turn in above table, it is recommended to stop with the stroke adjusting LS. Please contact us if press (pull) stop or internal stop is required due to the equipment.
- 3.When the Power Cylinder is used with press (pull) stop, strength of the mating equipment shall be 250% or more of the rated thrust.
When multiple operation run or stroke position control is performed
When the rod must not move even if an overload acts from the load side while it is stopped.
For the C type, a spring mechanism is built in the operating part, therefore, when a large load is applied from the load side, the spring deflects and the rod moves by the degree of deflection.
When the load is eliminated, the rod returns to the original position.
- ・The B type of the multi series is not equipped with an overload protecting function. If an overload protection function is required on the cylinder main body, select the C type.
- ・When installing a sprocket, a gear or a pulley on the input or output shaft, check that an overhang load acting on the shaft is less than the allowable overhang load.
Allowable O. H. L. ≧ T×f×Lf R
OHL:Overhang load (N{kgf})
T:Load torque (N・m{kgf・m})
f:Transmission element factor
Lf:Factor by load acting position
R:Pitch circle radius of sprocket, gear, V pulley (m)
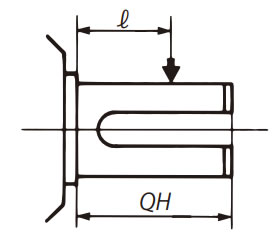
QH:Length of shaft
ℓ:Load acting position
Transmission element factor (f)
Sprocket | 1.00 |
---|---|
Gears | 1.25 |
V-Belt | 1.50 |
Flat belt | 2.50 |
Factor by load acting position (Lf)
ℓ/QH | 0.25 | 0.38 | 0.5 | 0.75 | 1 |
---|---|---|---|---|---|
Lf | 0.8 | 0.9 | 1 | 1.5 | 2 |
Table 1
Power cylinder model | LPT500 | LPT1000 | LPT2000 | LPT4000 |
---|---|---|---|---|
Allowable overhang load N{kgf} | 803{82} | 1303{133} | 2251{230} | 4005{409} |