Technical Data Linear actuator Linipower Jack Selection
Conditions required for selection
Machine to be used ..... Table or theatre lifter, conveyer line selector etc.
Layout ..... Patterns of multiple jack systems (4, 6 or more units), driving, coupling etc.
Maximum load (W) ..... Load or work weight N{kgf}
Screw Shaft Speed (V) ..... Required speed for jack m/min
Stroke ..... Actual stroke used mm
Screw type ..... Ball screw type (JWB)、High lead ball screw type (JWH)、Trapezoidal screw type (JWM)
Mounting style ..... Standard model (Lift or suspend, with or without rotation prevention )、Travel Nut Type (For lifting orFor suspending )
Installation Conditions ..... Fixed base, shaft end clevis, etc. ・For compression loads, consider buckling.
Expected life ..... Years jack will withstand (for JWB, JWH only )
Selection procedure
1. Calculation of adjusted Load Ws
Calculate the adjusted Load Ws by determining the service factor (Table 1) for specific load characteristic.
Adjusted Load Ws (N{kgf}) = Maximum load W (N{kgf})×Service factor Sf
Table 1 Service factor Sf
Load characteristics | Usage examples | Service factor |
---|---|---|
Smooth operation without impact Small load inertia |
Opening/closing a valve Adjusting a conveyor |
1.0~1.3 |
Operation with light impact Medium load inertia |
Transfer systems Various kinds of lifters |
1.3~1.5 |
Operation with large impact/vibration Large load inertia |
Large transporting carriages, Holding the position of a press roller | 1.5~3.0 |
Note) The above operation factor table shows general guidelines, and please apply the appropriate factor depending on actual condition.
2. Load per jack
Calculate load W per jack, by using the adjusted load Ws obtained above. For a synchronous drive, use a multiple factor (Table 2).
Load / jack W (N{kgf}) = Adjusted Load Ws (N{kgf}) No. of jacks ×Multiple factor fd
Table 2 Multiple factor fd
Number of multiple units ( units ) | 2 | 3 | 4 | 5~8 |
---|---|---|---|---|
Multiple factor | 0.95 | 0.9 | 0.85 | 0.8 |
3. Jack Selection
Follow these steps to make a preliminary jack selection.
Points of preliminary jack selection
- 1.Select (temporary) worm speed ratio by adjusting the screw shaft speed. If difficult to select, examine by H speed.
- 2.Select a stroke for the jack with an extra margin with respect to the operating stroke.
- 3.Select options based on your needs.
4. Verifying Buckling and Screw Shaft Speed
- 1.Allowable Buckling Load
For a compressive load, verify that it does not exceed the allowable buckling load. (Click here )
If it exceeds the allowable value, increase jack size and recalculate. - 2.Allowable screw shaft speed
If using a travel nut, verify that it does not exceed the allowable shaft speed. (Click here )
If it exceeds the allowable value, increase jack size and recalculate.
5. Confirming Required Input speed
Determine the required input speed, using the required screw shaft speed.
N = V ℓ ×R
N:Input speed r/min
V:Screw Shaft Speed m/min
ℓ:Screw lead m
R:Worm Reduction Ratio
6. Verifying Required Input Torque
Calculate required input torque.
T = W×ℓ 2×π×R×η + To
T:Necessary input torque N・m{kgf・m}
W:Lift load N{kgf}
ℓ:Screw lead m
π:Pi (circular ratio) 3.14
R:Worm Reduction Ratio
η:Jack overall efficiency
To:Idling torque without load N・m{kgf・m}
- Note)
For screw lead, gear ratio, overall efficiency and no-load idle torque, see the major specifications page for each product.
Pay attention to the unit of screw lead. Example) 8mm → 0.008m
7. Verifying Input Capacity
SI Unit P = T×N 9550
Gravity unit P = T×N 974
T:Necessary input torque N・m{kgf・m}
P:Required input capacity kW
N:Input speed r/min
8. Allowable Overhang Load
When installing a sprocket, gear, or belt to the input shaft, confirm that any overhang load applied to the shaft decreases to the allowable OHL or less. (Click here )
If it exceeds the allowable value, increase jack size and recalculate.
9. Life check (JWB/JWH only )
Check if wear life is sufficient. (Click here )
When increasing travel distance, increase jack size and recalculate.
※Life cannot be calculated for JWM (trapezoidal screw) type.
10. Selecting Your Options
Select options that best suit your needs.
- ・Output Option ・Installation Option
- ・Position Sensor Option ・Input Option
- ・Accessory Option
(Refer to drawing library for each product )
11. Determining the jack body model number
Determine the actual Linipower Jack number that meets the above conditions.
Parts Options
Motor
Determine the required drive unit capacity for synchronous drive Pt value.
1. Overall Torque Tt
Add the torque required for each jack T1 to 4 on the drive unit side to determine the overall Torque Tt.
[Required Torque per Jack ]
T1~4 = T (Gearbox efficiency ) No. of gearbox
[Required Torque for the Drive Unit ]
Tt = T1 + T2 + T3 + T4
T1~4:Required torque for each jack on the drive unit side N・m{kgf・m}
T:Required input torque per jack N・m{kgf・m}
Gearbox efficiency :Assume 0.9
Tt:Required Torque for the Drive Unit N・m{kgf・m}
For a four unit system (Figure 1), T1 to 4 = T0.92.
Fig. 1
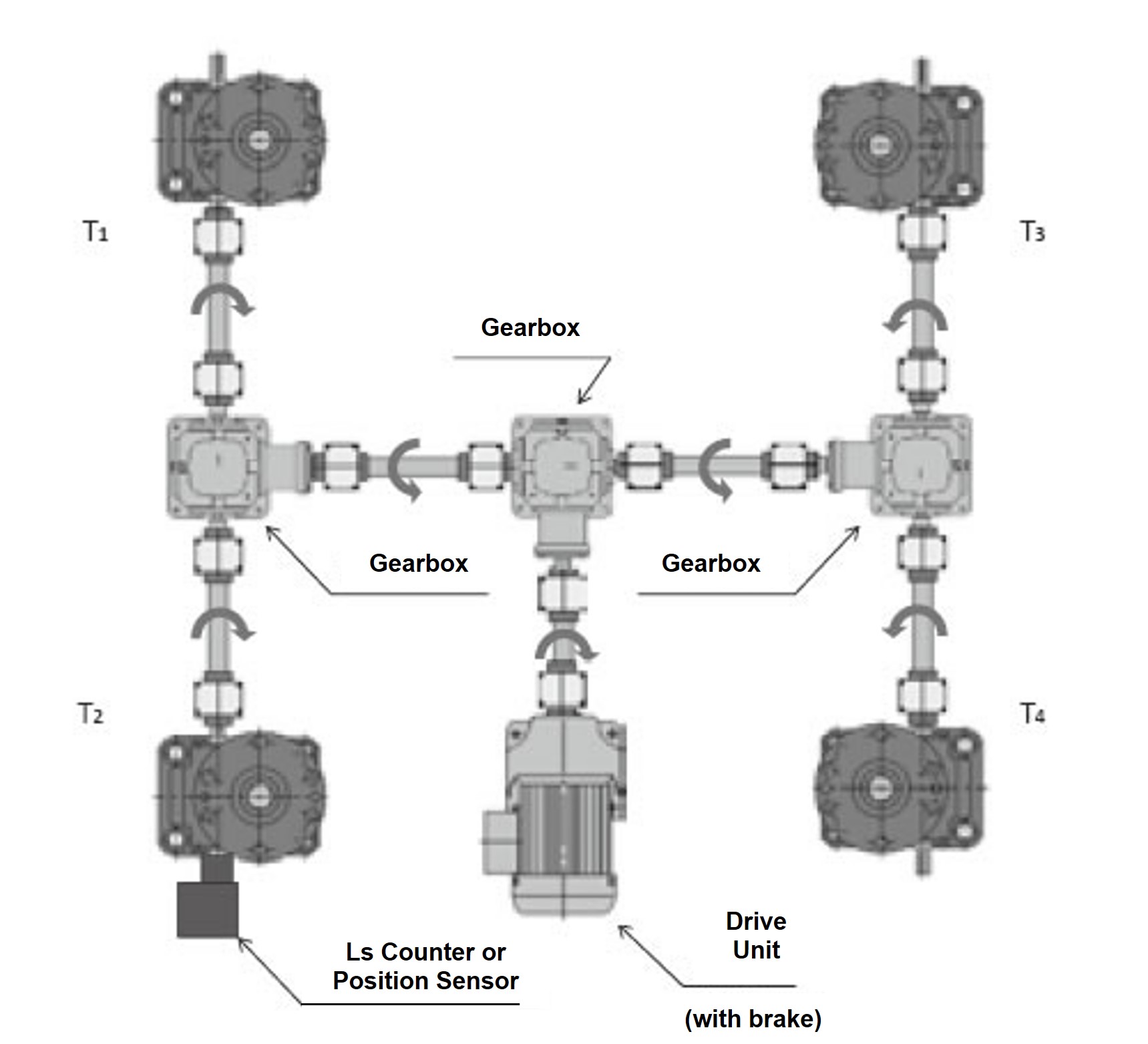
2. Verifying allowable input shaft torque
Be certain that the required input torque calculated is within the allowable input shaft torque.
Example)
If jacks are arranged in a linear structure as shown in Fig. 2, the drive unit input shaft transfers the total input torque required for both jacks.
This doubled torque should not exceed the allowable input torque.
Fig. 2
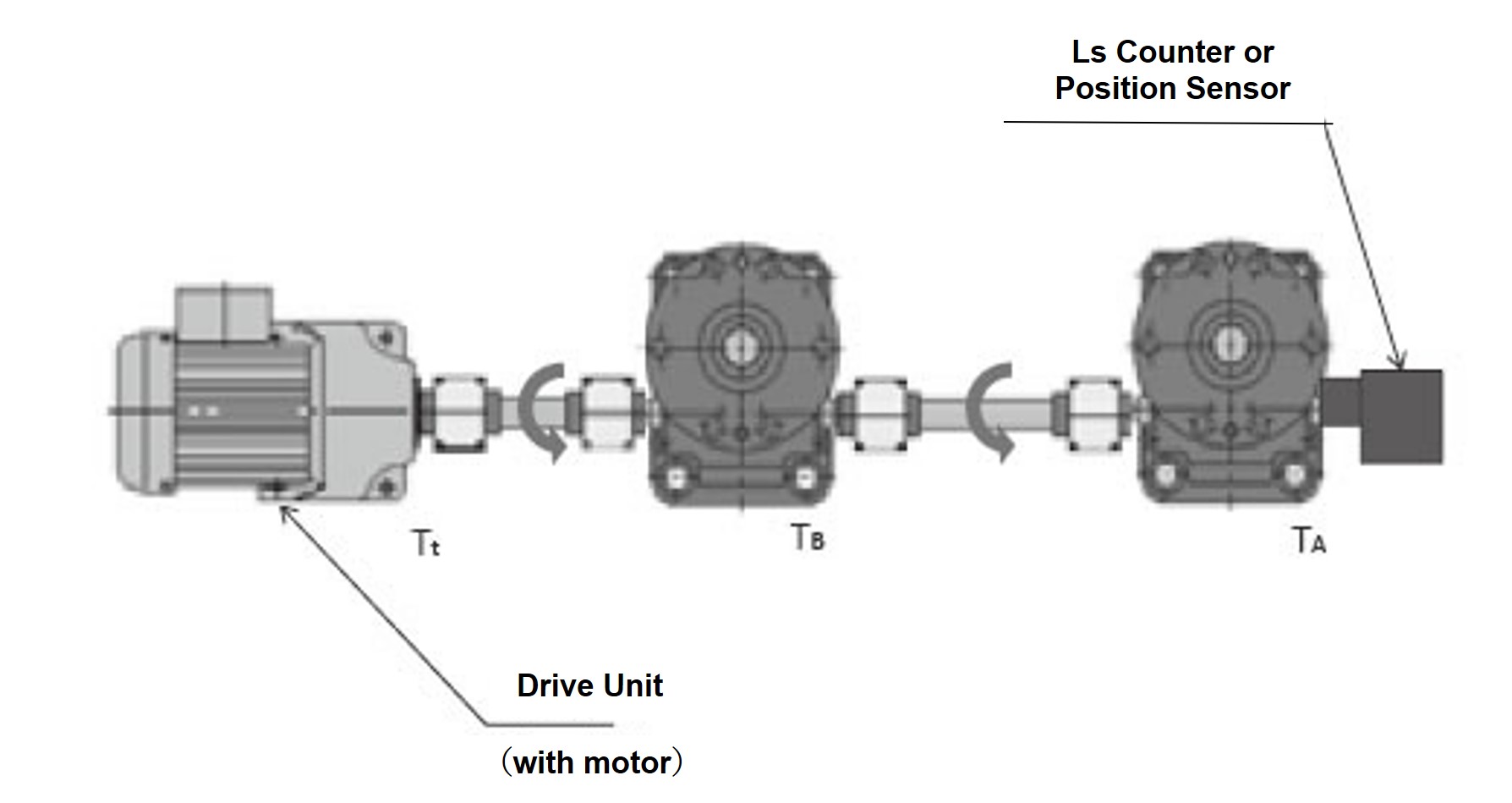
Required input torque for Jack A TA
Required input torque for Jack B TB
Required torque at the motor Tt = TA + TB < Allowable Torque on Input Shaft
3. Determine the required drive unit capacity Pt
Determine Pt with input speed N and overall Torque Tt calculated at the above 1.
SI Unit Pt = Tt×N 9550
Gravity unit Pt = Tt×N 974
Pt:Total required torque at the drive unit kW
Tt:Required Torque for the Drive Unit N・m{kgf・m}
N:Input speed for the jack r/min
Selection of other equipment
Gear Box
Select based on input speed and allowable torque.
Please refer to the Tsubaki Miter Gear Box single catalog.
Coupling
Select based on allowable torque and maximum shaft diameter.
Please refer to the Tsubaki coupling single catalog.
Selection example of Linipower Jack
Example :
Four jack synchronous drive for lifting (see layout below), operating at room temperature under low dust conditions.
Guide installed on the equipment to prevent side load, fixed base-Guided shaft end/Fixed shaft end, with 3-phase 220v/60Hz motor.
Operation cycle : (2 times/hour) X (8 hours/day) X (300 days/year) X (3 years usage)
- (1)Maximum load :98.0kN{10tf}/4 cylinders
- (2)Required speed :5mm/s(0.3m/min)
- (3)Operating stroke :260mm
Four Jack Drive System

※See above for T1-4
SI Unit |
---|
|
{Gravity unit } |
---|
|
Selecting Parts
A. Selecting a Drive Unit
1. Required torque for each jack on the drive unit side T1(2.3.4)
Since 4 jacks follow the same route,
SI Unit Tt = T1×4 = 83.5N・m
Gravity unit Tt = T1×4 = 8.52kgf・m
2. Inspecting the Rated Input Torque
In this case, inspection is not necessary because 2 or more jacks are not arranged in a linear structure.
3. Total required torque at the drive unit Pt
From the input speed 180r/min,
1800 180 = 10Based on this data we select GMTR220-42L10B, TSUBAKI 2.2kW gearmotor with a brake unit.
Please refer to the Tsubaki compact gearmotor catalog for details.
B.1.Select a gear box based on the required input torque of 15.4N・m{1.57kgf・m}, and input speed of 180r/min.
1-1.Gear box on each side of the jack must tolerate the combined torque of 2 jacks.
20.9×2
0.9
= 46.4N・m
2.13×2
0.9
= 5.11kgf・m
Thus we selected gear box ED4M.
(Make sure the direction of the gear box shaft rotation is correct. )
1-2.Gearbox by the gear motor required torque for 4 jacks.
20.9×4
0.92
= 103N・m
2.13×4
0.92
= 8.69kgf・m
From this, we find that the gear box ED6M is most suitable
Gear box by the jack
- Left side :ED4M 1-LR-O-Y
- Right side :ED4M 1-LR-Y
Gear box by the gearmotor
- ED6M 1-LR-Y
(Please refer to Tsubaki Miter Gear Box Catalog for details. )
B.2.Select couplings based on your requirements.
(Please refer to the Tsubaki coupling catalog for details. )
The following is an example process for selecting the right couplings.
2-1Select couplings used between each jack and their adjacent gear box based on the required input torque per jack, 16.9N・m {1.73kg・fm}, input shaft diameter (Φ20 for JWB050USH), and the gear box shaft diameter (Φ19 for ED4M).
Required number is 2×2×2=8.
2-2Select couplings used between the gear boxes based on the required torque for the nearest pair of jacks,
20.9×2 0.9 = 50.1N・m 2.13×2 0.9 = 5.11kgf・mand the diameter of each gear box shaft: one by the jack (Φ19 for ED4M), and the other by the gearmotor (Φ25 for ED6M).
Required number is 2×2=4.
2-3Select couplings used between each gear box and the gearmotor based on the total required torque for the four jacks,
20.9×4 0.92 = 85.2N・m 2.13×4 0.92 = 8.69kgf・mand the diameters of the gearbox (Φ25 for ED6M) and the gear motor output shafts (Φ42 for GMTR220-42L10B). Required number is 2.