Technical Data Drive chain Handling Roller Chains
4.Layout and Installation of Roller Chain
4.1 Speed ratio and chain wrap
A roller chain transmission speed ratio up to 7:1 is normally suitable; however, at very slow speeds a ratio up to about 10:1 is possible. The chain wrap between the small sprocket and chain must be 120° or more.
For lifting applications, the angle must be 90° or more.
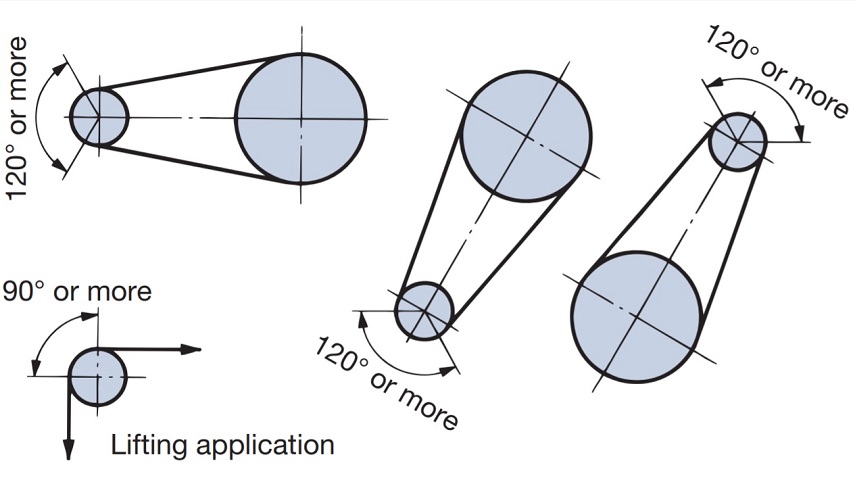
Fig. 13. Chain wrap
4.2 Distance between shafts
The minimum distance can be as short as desired as long as the teeth of the two sprockets are not in contact. The optimum center-to-center distance between the shafts is 30 to 50 times the pitch of the roller chain.
However, if the load is variable, a distance of 20 times or less is suitable.
4.3 Amount of slack
1. Unlike V or flat-belt transmission, there is no need to apply an initial tension in roller chain transmission.
Roller chain is normally used with a suitable amount of slack. If too much tension is applied to roller chain, the oil film between the pins and bushes will break, causing increased wear and damage on the roller chain and bearings.
If there is too much slack in the roller chain, the chain will vibrate and ride up the sprocket, damaging both chain and sprocket.
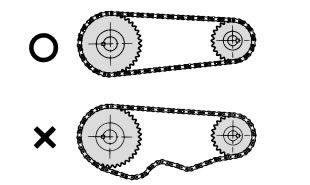
Fig. 14. Slack example
2. If possible, the lower side should be the slack side in roller chain transmission.
The amount of slack is appropriate when the distance SS' that the chain can be moved perpendicularly by hand at the center of the slack side is 4% of the span AB.
(ex. :For example, when the span is 800 mm, the amount of slack should be 800 mm x 0.04 = 32 mm. )
In the following situations, this should be 2%:
- ・When the transmission is vertical or close to vertical
- ・When the distance between the shafts is more than 1m
- ・When frequent starts are made with a heavy load
- ・When sudden reverse motion takes place
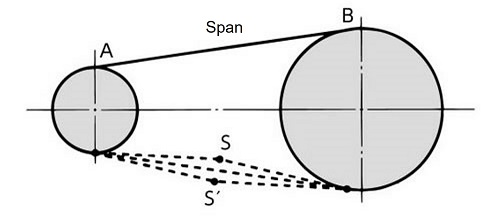
Fig. 15. Amount of slack
3. Roller chain will stretch slightly during the first few dozen hours of use as the contact surfaces wear in about 0.05%.
This may require adjustment of the slack.
A tensioner can be used if the layout is designed for it. If you do not have a tensioner, move the shafts to adjust the amount of slack. Once the chain is worn in, very little stretching will occur.
4.4 Horizon precision and parallelism of the shafts
The installation precision of the sprocket has an effect on the smoothness of roller chain transmission. It also affects roller chain life.
1. Verify horizontal precision with a level.
Adjust the precision to within ±1300.
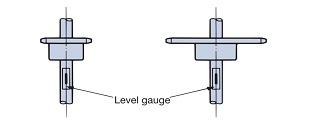
Fig. 16. Horizontal precision of the shafts
2. Use a scale to correct the degree of parallelism of the shafts.
Adjust the shafts so that they are parallel to within ±1300 ≥ A - BL.
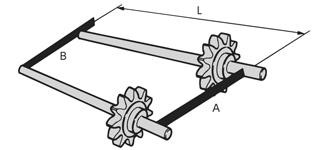
Fig. 17. Parallelism of the shafts
3. Using a straightedge or Easy-Laser, adjust the two sprockets so that they are parallel. Adjust to within the following values based on the distance between the shafts.
- Up to 1 m :±1mm
- 1~10m:± Distance between shafts (mm)1,000
- 10m or more :±10mm
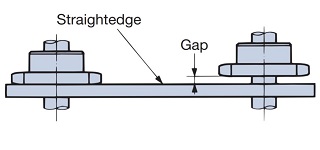
Fig. 18. Sprocket alignment
Secure each sprocket to the shaft with a power lock, lock sprocket, or key.
If needed use a collar, set bolt, or other adjustment component.
4.5 Layout
1. General layout
Ideally, the line connecting the sprocket centers in the roller chain transmission equipment should be close to level. In a layout that is close to vertical, the roller chain may stretch and fall off the sprocket. Thus, an idler or tensioner should be used. If possible keep the angle of inclination within 60°.
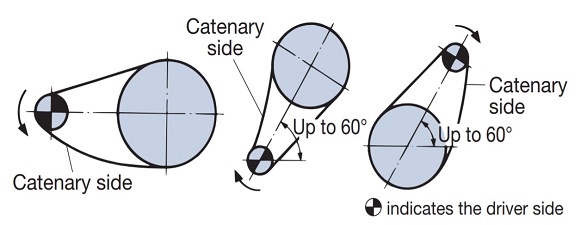
Fig. 19. General layout
2. Layouts requiring caution
・When the slack is on the upper side
When the center-to-center distance between the shafts is short, move the shafts to adjust the distance and slightly increase the tension.
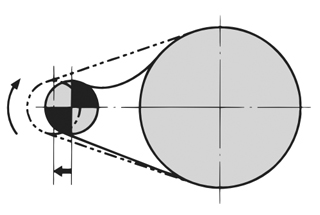
Fig. 20. Layout when the center-to-center distance is short
When the center-to-center distance is long, insert an intermediate idler under the slack part to support the roller chain.
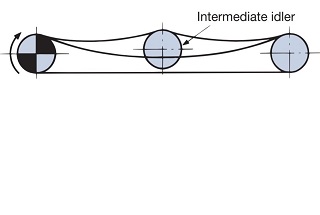
Fig. 21. Layout when the center-to-center distance is long
・When the chain speed is fast and the load varies
Roller chain may vibrate if the natural vibration frequency of the chain, shock frequency of the driven machine, or chordal action of the chain (vertical pulsation of the chain due to the polygon effect) synchronize.
In this event, use a guide shoe (made of NBR or ultra-high polymer polyethylene) or other device to stop the vibration.
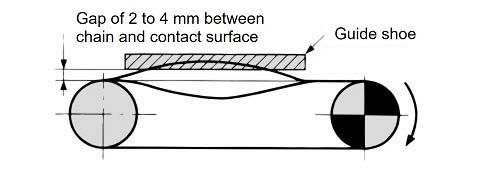
Fig. 22. Guide shoe to prevent vibration
・When the centerline is vertical
Install a tensioner that can automatically eliminate excess slack to ensure the sprockets engage. This is particularly necessary when the drive shaft is on the bottom.
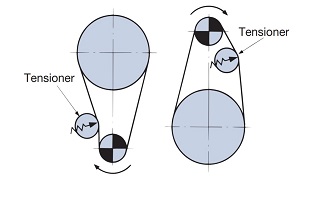
Fig. 23. Layout for vertical transmission
4.6 Curved chain installation
1. Installing the guide
Compared to RS roller chain, a curved chain has a greater degree of freedom. For this type of chain, install a guide on the chain so that it engages straight onto the sprocket.
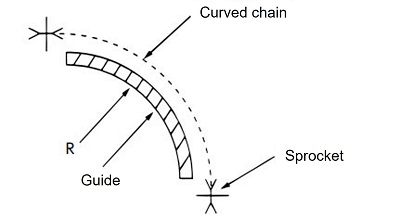
Fig. 24. Guide
2. Minimum lateral bending radius (r)
Install the guide so that its minimum lateral bending radius is equal to or greater than the specifications shown below.
Product name | Min. lateral bending radius (r) |
---|---|
RS40-CU-1 | 350 |
RS50-CU-1 | 400 |
RS60-CU-1 | 500 |
RS80-CU-1 | 600 |
RS40-LMCCU-1 | 400 |
RS50-LMCCU-1 | 500 |
RS60-LMCCU-1 | 600 |
Product name | Min. lateral bending radius (r) |
---|---|
RS40-CUSS-1 | 400 |
RS50-CUSS-1 | 500 |
RS60-CUSS-1 | 600 |
RS80-CUSS-1 | 800 |