Technical Data Drive chain Roller Chain Selection
10. Pin gear drive Pin gear drive
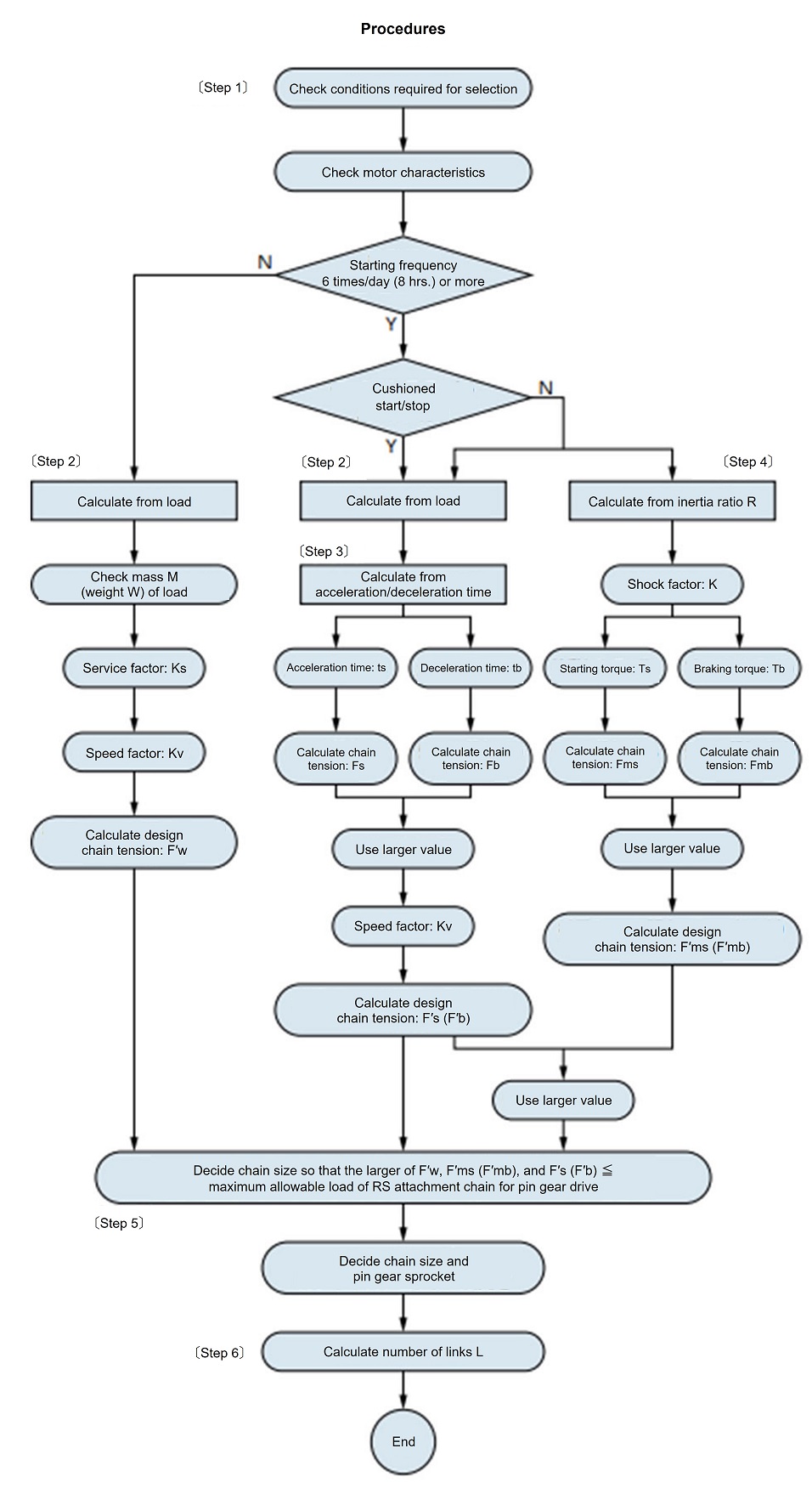
1. Speed considerations
This selection method can be applied when the relative chain speed is 50 m/min or less.
(Examples: 50 m/min or less )
- When a linear application is being considered: :
Switch to a winding method such as a roll drive - When a wrapping application is being considered: :
Change the chain mounting diameter to a smaller value
Relative chain speed m/min |
Pin gear speed factor |
---|---|
Less than 15 | 1.0 |
15 to 30 | 1.2 |
30 to 50 | 1.4 |
2. Sprocket considerations
Use a chain-type pin gear sprocket with 13 or more teeth;
18 teeth are recommended.
3. Examples of chain-type pin gear drive
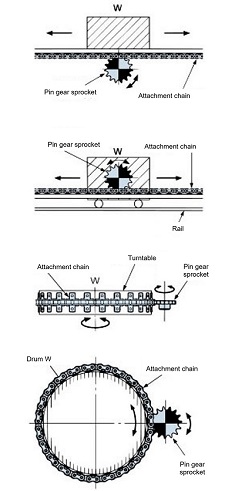
Please also refer to the calculation formulas (click here) and factors (click here) used for chain selection, as well as calculating moment of inertia (click here).
Pin gear drive selection example
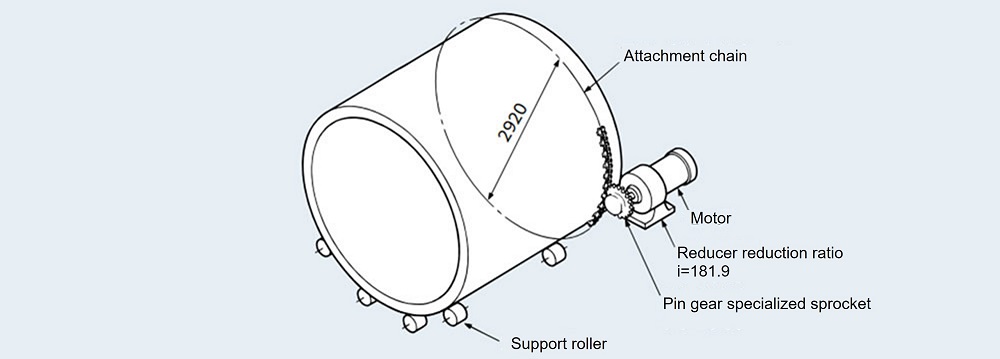
SI Unit |
---|
Steps 1 Check machine and motor characteristics
Steps 2 Calculate from loadRevolution speed of the pin gear drive sprocket n = 1750 ×
1
181.9
Relative chain speed V =
220 × π × 9.6
1000
= 6.6 (m/min) Some impact assumed from cutting machine Load is calculated from the torque on the drive side as the mass of the load is unknown. Rated torque of the motor
Pin gear drive sprocket shaft torque Chain working tension F = 2T d 1000 = 2 × 1.49 220 1000 = 13.6 (kN)
Design chain tension F'w = F × Ks × Kv = 13.6 × 1.3 × 1.0 Steps 3 Calculate from acceleration/deceleration timeWorking torque Tm =
Ts + Tb
2 × 100
× Tn =
290 + 305
2 × 100
× 0.00819 As the load is unknown, the rated torque of the motor is Tn = Tℓ and the load torque Tℓ = 0.00819(kN·m)
Acceleration time ts =
(Im + Iℓ) × n1
9550 × (Tm - Tℓ)
=
(0.00425 + 0.00072) × 1750
9550 × (0.0244 - 0.00819)
Motor braking torque Tb = 0.00819 × 1.8 = 0.0147 (kN・m)
Deceleration time tb =
(Im + Iℓ) × n1
9550 × (Tb + Tℓ)
Moment of inertia for the motor shaft converted load IIℓ = 0.00072 (kg・m2) Fw = F= 13.6 (kN) [value from Step 2 ] tb < ts, so find the chain tension during deceleration. Motor shaft angular velocity ω = 2π × n1 = 2π × 1750 = 11000 (rad)
Motor shaft angular deceleration ωb =
ω
60 × tb
=
11000
60 × 0.040
Chain tension during deceleration Fb =
Iℓ × ωb × i
1000 ×
d
(2 × 1000)
+ Fw Design chain tension during deceleration
F'b = Fb × Kv = 19.1 × 1.0 Steps 4 Calculate from inertia ratio RInertia ratio R = Iℓ Im = 0.00072 0.00425 = 0.17 According to Table 4, impact factor K = 0.23 (There is no play in the drive transmission equipment as R < 0.2, R = 0.2.) Chain tension at start-up Fms =
Ts × i
d
2 × 1000
× 100
× Tn Chain tension at stop Fmb =
Tb × i
d
2 × 1000
× 100
× Tn × 1.2 As Fms > Fmb, Steps 5 Comparison of (1), (2), and (3)Comparing (1), (2), and (3), an attachment chain for pin gears that meets 19.1kN of the maximum working load (2) is selected. The maximum allowable load for RS120 attachment chain with pin gear use is 20.6 kN, which is acceptable. A sprocket with 18 teeth (PCD = 222.49 mm) is selected as tentative from the pitch circle diameter of the pin gear sprocket approximate. Φ220. Steps 2, 3, and 4 are calculated again here. [Steps 2] F = 2T d 1000 = 2 × 1.49 222.49 1000 = 13.4 (kN) F'w = F × Ks × Kv = 13.4 × 1.3 × 1.0 = 17.4 (kN) [Steps 3] Fb =
Iℓ × ωb × i
1000 ×
d
(2 × 1000)
+ Fw Design chain tension during deceleration F'b = Fb × Kv = 18.8 × 1.0 = 18.8 (kN) [Steps 4] Fms =
Ts × i
d
2 × 1000
× 100
× Tn Design chain tension F'ms = Fms × K × Kv = 38.8 × 0.23 × 1.0 = 8.92 (kN) Either design chain tension is within the maximum allowable load, so a chain with pin gear attachments and a pin gear sprocket can be used. [Steps 6] Calculating number of links L Calculating number of links L Corresponding standard length for 242 links (38.1 × 242 = 9220.2mm) |
{Gravity unit } |
---|
Steps 1 Check machine and motor characteristics
Steps 2 Calculate from loadRevolution speed of the pin gear drive sprocket n = 1750 ×
1
181.9
Relative chain speed V =
220 × π × 9.6
1000
= 6.6 (m/min) Some impact assumed from cutting machine Load is calculated from the torque on the drive side as the mass of the load is unknown. Rated torque of the motor
Pin gear drive sprocket shaft torque Chain working tension F = 2T d 1000 = 2 × 152 220 1000 = 1380 (kgf)
Design chain tension F'w = F × Ks × Kv = 1380 × 1.3 × 1.0 Steps 3 Calculate from acceleration/deceleration timeWorking torque Tm =
Ts + Tb
2 × 100
× Tn =
290 + 305
2 × 100
× 0.835 As the load is unknown, the rated torque of the motor is Tn = Tℓ and the load torque Tℓ = 0.835kgf·m
Acceleration time ts =
(GD2m + GD2ℓ) × n1
375 × (Tm - tℓ)
=
(0.017 + 0.00288) × 1750
375 × (2.48 - 0.835)
Motor braking torque Tb = 0.835 × 1.8 = 1.50 (kgf・m)
Deceleration time tb =
(GD2m + GD2ℓ) × n1
375 × (Tb + Tℓ)
Motor shaft converted load GD2 GD2ℓ = 0.00288 (kgf・m2) Fw = F = 1380 (kgf) [value from Step 2 ] tb < ts, so find the chain tension during deceleration. Motor shaft angular velocity ω = 2π × n1 = 2π × 1750 = 11000 (rad)
Motor shaft angular deceleration ωb =
ω
60 × tb
=
11000
60 × 0.040
Chain tension during deceleration Fb =
GD2ℓ / 4 × ωb × i
d
(2 × 1000)
× G
+ Fw Design chain tension during deceleration
F'b = Fb × Kv = 1940 × 1.0 Steps 4 Calculate from inertia ratio RInertia ratio R = GD2ℓ GD2m = 0.00288 0.017 = 0.17 According to Table 4, impact factor K = 0.23 (There is no play in the drive transmission equipment as R < 0.2, R = 0.2.) Chain tension at start-up Fms =
Ts × i
d
2 × 1000
× 100
× Tn Chain tension at stop Fmb =
Tb × i
d
2 × 1000
× 100
× Tn × 1.2 As Fms > Fmb, Steps 5 Comparison of (1), (2), and (3)Comparing (1), (2), and (3), an attachment chain for pin gears that meets 1940 kgf of the maximum working load (2) is selected. The maximum allowable load for RS120 attachment chain with pin gear use is 2100 kgf, which is acceptable. A sprocket with 18 teeth (PCD = 222.49 mm) is selected as tentative from the pitch circle diameter of the pin gear sprocket approximate. Φ220. Steps 2, 3, and 4 are calculated again here. [Steps 2] F = 2T d 1000 = 2 × 152 222.49 1000 = 1370 (kgf) F'w = F × Ks × Kv = 1370 × 1.3 × 1.0 = 1780 (kgf) [Steps 3] Fb =
GD2ℓ/4 × ωb × i
d
(2 × 1000)
× G
+ Fw Design chain tension during deceleration F'b = Fb × Kv = 1930 × 1.0 = 1930 (kgf) [Steps 4] Fms =
Ts × i
d
2 × 1000
× 100
× Tn Design chain tension F'ms = Fms × K × Kv = 3960 × 0.23 × 1.0 = 911 (kgf) Either design chain tension is within the maximum allowable load, so a chain with pin gear attachments and a pin gear sprocket can be used. [Steps 6] Calculating number of links L Calculating number of links L Corresponding standard length for 242 links (38.1 × 242 = 9220.2mm) |
Selection results
Chain Model No. | RS120-2LK1+242L-JR |
Sprocket model No. | RS120-1□18TQ-G (Enter hub model in the blank. ) |
Please also refer to the calculation formulas (click here) and factors (click here) used for chain selection, as well as calculating moment of inertia (click here).