Technical Data Linear actuator Linispeed Jack Handling
This section describes the general handling of Linispeed jacks.
For details, please refer to the instruction manual included with the product.
Mounting
Jack mounting surface
The mounting surface of the jack is painted for rust prevention purposes. If painting is not required on the mounting surface, please contact us.
Mounting Direction [The position of each plug differs according to the mounting type. ]
Check that the mounting type and the mounting position of each plug (pressure vent and drain plug) are correct.
(For details, please check the external dimensions on the major specifications page of each product. )
The reducer unit is shipped with oil sealed in it. To prevent oil leakage during transportation, the grease port is closed with a plug, so please replace the plug with the included pressure vent before use. If the unit is operated with the plug in place, the internal pressure may increase and oil may leak from the oil seal area.
Installation location
Do not place any obstructions around the jack that may block ventilation. Cooling may be inhibited, resulting in burns or fire due to abnormal heating. To install a screw shaft or cover to the base, avoid drilling large holes so as not to reduce the surface area of contact between the jack and the base.
Grease or oil may scatter or fall. For equipment such as food manufacturing machines that does not tolerate oily air, install an oil pans or other damage prevention device to prevent grease or oil from splashing or falling.
Mounting Bolt
Tighten bolts into the 4 mounting holes in the gear case. (No mounting bolts provided. )
See Table below for bolt sizes. In normal cases, use mounting bolts with strength class 10.9 or higher.
Mounting bolt size, mounting hole size
Model | Face mount | Flange mount |
---|---|---|
SJ015H | M10 | Φ11 |
SJ030H | M12 | Φ14 |
SJ050H | M16 | Φ18 |
Connection with motor
When installing a motor and reducer unit in addition to the jack body, prepare a robust counter making allowance for a safety factor to prevent alignment accuracy at installation from being reduced even if the maximum load is applied. Make sure that the transmission shaft connected to the input shaft is aligned accurately.
Using a floating shaft may result in malfunction due to vibration depending on rotation speed, therefore, sufficiently consider rigidity of the shaft and backlash of the coupling.
Shaft End
When attaching the end fitting to the end of the screw shaft, apply an adhesive agent to the end of screw shaft to prevent a loosening. It is possible for the shaft end to become detached by the rotational torque applied to the shaft. To avoid this, use one of the following adhesives:
-
(1)Tightening Agents
Use the following brands or their equivalent. Read instructions and safety precautions provided with each product before applying
Tightening Agents
Company name Brand Henkel #262、271 Three Bond #1307N - (2)Fixing with set screw
After tightening the end fitting, fix with the attached set screw (hexagon socket head screw) as a locking device.
Setting the Limit Switch
Take jack coasting amount into consideration to set the stroke adjusting limit switch. Consider maximum possible inertia before setting the limit switch. This means calculating the maximum coasting distance affected by specific load and installation conditions. Also, install a mechanical stopper within the stroke range in case of emergencies.
Setting the Position Detection Unit
An optional position detection unit (internal LS, potentiometer or rotary encoder) is not factory adjusted for its stroke. Make sure to adjust stroke prior to use. When adjusting the internal LS, operate the jack manually or by inching with sufficient care so as not to exceed the stroke range of the jack. If the jack exceeds its stroke limit, the screw shaft may fall off or the bellows may be damaged.
Notes
- ⚠ (1)Do not perform manual operation from the input shaft with load applied. The input shaft may be rotated by the load, which is dangerous.
- ⚠ (2)Do not press stop under any circumstances. This may cause critical damage to jacks.
- ⚠ (3)Make sure that the load applied to the jack is coaxial with the direction of the screw shaft of the jack. If the acting direction or position is inappropriate, bending load or lateral load will be applied to the jack, which may cause damage. (Fig. 2)
For side load, make sure to use guides so the load or bending momentum do not apply directly to the jack. - ⚠ (4)Please make sure that the torque of these two jacks do not exceed the allowable input shaft torque.
Fig. 2
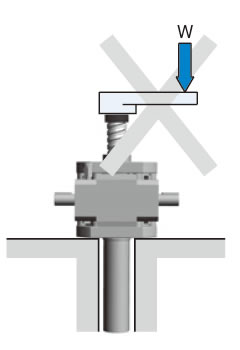