Technical Data Locking Device Sizing and procedure
To view selection procedures and precautions, please proceed to the following.
Click here to narrow down the product series or to make a tentative selection.
If you have specific conditions of use and wish to make a detailed selection, please click here.
Selection of EL series
1. Maximum Torque and Maximum Thrust
Calculate maximum torque and thrust based on transmissible capacity and safety factor f.
※For servo motor and stepping motor locking, use the maximum torque (peak torque) of each as the maximum torque to be generated (Tmax).
SI Unit |
---|
Tmax = 9550 × H n ・f Tmax = Max. Generated Torque (N・m)
|
Gravity unit |
---|
Tmax = 974 × H n ・f Tmax = Max. Generated Torque (kgf・m)
|
Pmax = Pax・f
- Pmax:Max. Thrust Load kN{kgf}
- Pax:Thrust load kN{kgf}
- f:Service factor
f:Service factor
Load conditions | Service factor | |
---|---|---|
Load without shock | Low inertia | 1.5~2.5 |
Load with minor shock | Medium inertia | 2.0~4.0 |
Load with major shock | High inertia | 3.0~5.0 |
If only torque is applied
Compare the Tmax obtained from the above calculation with the catalog rated transmissible torque Mt.
Mt ≥ Tmax → Acceptable
Mt < Tmax → Use larger size or multiple units.
If torque and thrust are applied simultaneously
Calculate the total load MR, and compare it with transmissible torque Mt.
MR = Tmax2 + (Pmax × d 2 )2
- Tmax:Max. Generated Torque N・m{kgf・m}
- Pmax:Max. Thrust Load N{kgf}
- d:Shaft diameter m
Compare the MR obtained from the above calculation with the catalog rated transmissible torque Mt.
Mt ≥ MR → Acceptable
Mt < MR → Use larger size or multiple units.
*Installing multiple units is possible for this series. When installing more than one unit, multiply the Mt value with the multiplying ratio given below.
Quantity | 1 | 2 | 3 | 4 |
---|---|---|---|---|
Amplification | 1 | 1.55 | 1.85 | 2 |
2. Actual Locking Force, Transmissible Torque and Contact Pressure
(1)When the required transmissible torque Mt is different from the (Mt) listed in the Model Numbers and Specifications table
Calculate the actual locking force Fe, thrust Pax, contact pressure P and P' using the following formulas.
- C1 = Mt / [Mt] (Required transmissible torque ratio )
- Fe = C1 × [Fe] N{kgf} (Actual locking force )
- F = Fo + Fe N{kgf} (Total force )
- Pax = C1 × [Pax] N{kgf} (Thrust load )
- P = C1 × [P] MPa{kgf/mm2} (Shaft-side contact pressure )
- P' = C1 × [P'] MPa{kgf/mm2} (Hub-side contact pressure )
- Mt:Required transmissible torque N・m{kgf・m}
Fo,〔Fe〕,〔Mt〕,〔Pax〕,〔P´〕: Refer to Model Numbers and Specifications tables.
(2)When the required actual locking force Fe is different from〔Fe〕listed in the Model Numbers and Specifications table
Calculate transmissible torque Mt, thrust Pax, contact pressure P and P' using the following formulas.
- C2 = Fe / [Fe] (Required actual locking force ratio )
- Mt = C2 × [Mt] N・m{kgf・m} (Transmission Torque)
- Pax = C2 × [Pax] N{kgf} (Thrust load )
- P = C2 × [P] MPa{kgf/mm2} (Shaft-side contact pressure )
- P' = C2 × [P'] MPa{kgf/mm2} (Hub-side contact pressure )
- Fe :Required actual locking force N{kgf}
Fo,〔Fe〕,〔Mt〕,〔Pax〕,〔P´〕: Refer to Model Numbers and Specifications tables. Note) 0.25 ≦ C2 ≦ 2
(3) Multiple Product Installation
Calculate transmissible torque Mtz, thrust Paxz and contact pressure Pz and P'z using the following formulas. (z:Number of EL units installed )
- Mtz = S・Mt1
- Paxz = S・Pax1
- Pz = P1 (Shaft-side )
- P'z = P'1 (Hub-side )
Mt1, Pax1, P'1 apply to single unit installation.
Z | S |
---|---|
1 | 1 |
2 | 1.55 |
3 | 1.85 |
4 | 2 |
3. Shaft and Hub
"Power-Lock" EL Series shaft-hub locking devices do not have a self-centering function. A hub must be pre-centered, using the guide portion provided between the shaft and hub.
A guide portion length above d/2 is generally preferred. Also, select guide tolerance based on the degree of accuracy you desire.
(1) Material Strength
Select shaft and hub materials that meet the following strength requirements.
σ0.2S ≧ 1.4 × P σ0.2B ≧ 1.4 × P'
- σ 0.2S、σ 0.2B:Yield point of shaft and hub material MPa{kgf/mm2}
- P、P':Contact pressure on the shaft and hub bore MPa{kgf/mm2}
Please refer to the strength table for iron and steel materials, which shows the yield point values of typical steel materials.
(2) Required Hub Outer Diameter DN and Allowable Hollow Shaft Bore Diameter dB
Hubs must have a DN that is greater than the value obtained from the following formula. If using a hollow shaft, its bore must be equivalent to or less than the dB obtained from the appropriate formula below.
(a) Bolts Fastened to the Hub Section
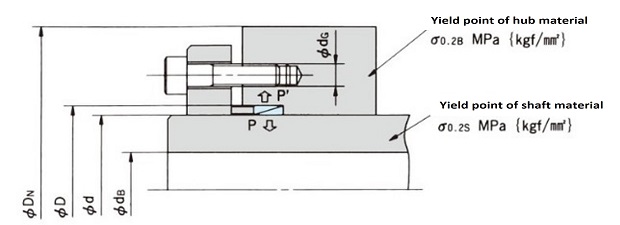
DN ≧ D σ0.2B + 0.8 × P' σ0.2B - 0.8 × P' + dG
dB ≦ d σ0.2S - 1.2 × P σ0.2S
(b) Bolts Fastened to the Shaft Section
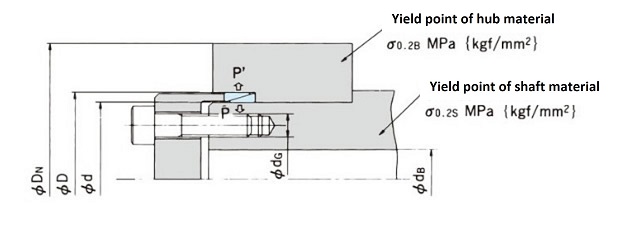
DN ≧ D σ0.2B + 0.6 × P' σ0.2B - 0.6 × P'
dB ≦ d σ0.2S - 1.6 × P σ0.2S - dG
P、P':Contact pressure on the shaft and hub MPa{kgf/mm2}
4. Selecting Locking Bolts
(1) Bolt Strength Classes and Mechanical Properties
Click here for Bolt Strength Classes and Mechanical Properties in details. In general, however, 10.9 and 12.9 class bolts should be used.
These bolts are less affected by vibration and do not loosen as easily as others. The tightening torque for 10.9 bolts may be used for 12.9 bolts.
(2) Bolt Head Bearing Surface Pressure
When using 10.9 or 12.9 bolts, check the pressure at their bearing surfaces.
If this pressure exceeds the maximum values provided below, the bearing surfaces will eventually deform, causing the bolts to loosen from decreased axial force.
When the bearing pressure rises above the maximum values, reduce by increasing the strength of pressure flange (either change the material or treat with heat) or by lowering the tightening torque in order to prevent the bearing surfaces from deforming to a large degree. The calculations for bearing surface area and bearing surface pressure are as follows.
Bearing surface area = As = π 4 (D2 - da2max) mm2
- D:Bolt head diameter (Refer to Technical Data )mm
- da max:Nominal diameter (Refer to Technical Data )mm
- Bearing surface pressure Ps = Fv / As MPa{kgf/mm2}
- FV:Tightening torque N{kgf}
Maximum Surface Pressure by Material (Junker)
Material | Mechanical Properties | Maximum Surface Pressure Pw MPa{kgf/mm2} |
||||||
---|---|---|---|---|---|---|---|---|
Product name | German Standards | JIS Equivalent | Tensile strength MPa{kgf/mm2} |
Yield Point in Compression MPa{kgf/mm2} |
||||
LowCarbon Steel | St37 | S10C | 346 | 35.3 | 272 | 27.9 | 294 | 30 |
MediumCarbon Steel | St50 | S30C | 505 | 51.5 | 329 | 33.6 | 490 | 50 |
Heat Treated Carbon Steel | C45 | S45C (Thermally Refined ) |
721 | 73.6 | 478 | 48.8 | 882 | 90 |
Cast iron | GG22 | - | 228 | 23.3 | 443 | 45.2 | 980 | 100 |
5. Pressure System Designs
Pressure flanges experience a great deal of stress while locking bolts are being tightened. To avoid plastic deformation, use a pressure flange with the appropriate material strength and provide enough leeway in the design to account for some stress.
Provided below are example pressure system design and calculations.
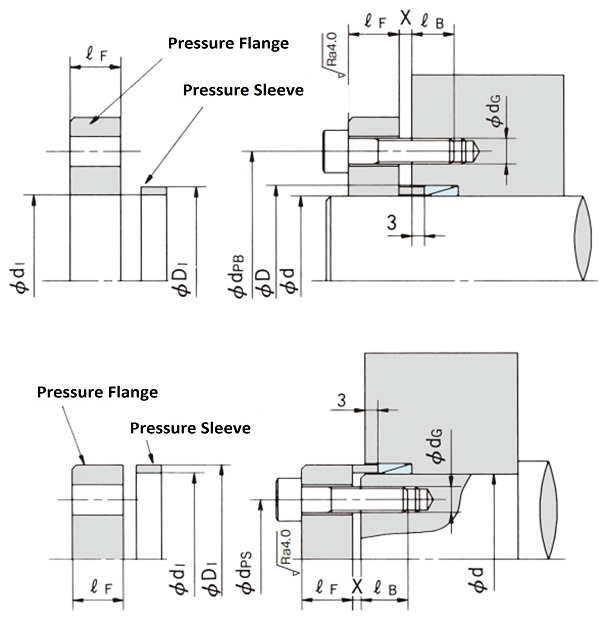
See table below for d1, D1 and X dimensions.
Model No. d X D mm |
Gap X Number of EL P.L.s Installed |
Pressure Sleeve Diameters | ||||
---|---|---|---|---|---|---|
1 | 2 | 3 | 4 | d1 | D1 | |
PL010X013E | 2 | 2 | 3 | 3 | 10.1 | 12.9 |
PL011X014E | 2 | 2 | 3 | 3 | 11.1 | 13.9 |
PL012X015E | 2 | 2 | 3 | 3 | 12.1 | 14.9 |
PL013X016E | 2 | 2 | 3 | 3 | 13.1 | 15.9 |
PL014X018E | 3 | 3 | 4 | 5 | 14.1 | 17.9 |
PL015X019E | 3 | 3 | 4 | 5 | 15.1 | 18.9 |
PL016X020E | 3 | 3 | 4 | 5 | 16.1 | 19.9 |
PL017X021E | 3 | 3 | 4 | 5 | 17.1 | 20.9 |
PL018X022E | 3 | 3 | 4 | 5 | 18.1 | 21.9 |
PL019X024E | 3 | 3 | 4 | 5 | 19.2 | 23.8 |
PL020X025E | 3 | 3 | 4 | 5 | 20.2 | 24.8 |
PL022X026E | 3 | 3 | 4 | 5 | 22.2 | 25.8 |
PL024X028E | 3 | 3 | 4 | 5 | 24.2 | 27.8 |
PL025X030E | 3 | 3 | 4 | 5 | 25.2 | 29.8 |
PL028X032E | 3 | 3 | 4 | 5 | 28.2 | 31.8 |
PL030X035E | 3 | 3 | 4 | 5 | 30.2 | 34.8 |
PL032X036E | 3 | 3 | 4 | 5 | 32.2 | 35.8 |
PL035X040E | 3 | 3 | 4 | 5 | 35.2 | 39.8 |
PL036X042E | 3 | 3 | 4 | 5 | 36.2 | 41.8 |
PL038X044E | 3 | 3 | 4 | 5 | 38.2 | 43.8 |
PL040X045E | 3 | 4 | 5 | 6 | 40.2 | 44.8 |
PL042X048E | 3 | 4 | 5 | 6 | 42.2 | 47.8 |
PL045X052E | 3 | 4 | 5 | 6 | 45.2 | 51.8 |
PL048X055E | 3 | 4 | 5 | 6 | 48.2 | 54.8 |
PL050X057E | 3 | 4 | 5 | 6 | 50.2 | 56.8 |
PL055X062E | 3 | 4 | 5 | 6 | 55.2 | 61.8 |
PL056X064E | 3 | 4 | 5 | 7 | 56.2 | 63.8 |
PL060X068E | 3 | 4 | 5 | 7 | 60.2 | 67.8 |
PL063X071E | 3 | 4 | 5 | 7 | 63.2 | 70.8 |
PL065X073E | 3 | 4 | 5 | 7 | 65.2 | 72.8 |
PL070X079E | 3 | 5 | 6 | 7 | 70.3 | 78.7 |
PL071X080E | 3 | 5 | 6 | 7 | 71.3 | 79.7 |
PL075X084E | 3 | 5 | 6 | 7 | 75.3 | 83.7 |
PL080X091E | 4 | 5 | 6 | 8 | 80.3 | 90.7 |
PL085X096E | 4 | 5 | 6 | 8 | 85.3 | 95.7 |
PL090X101E | 4 | 5 | 6 | 8 | 90.3 | 100.7 |
PL095X106E | 4 | 5 | 6 | 8 | 95.3 | 105.7 |
PL100X114E | 4 | 6 | 7 | 9 | 100.3 | 113.7 |
PL110X124E | 4 | 6 | 7 | 9 | 110.3 | 123.7 |
PL120X134E | 4 | 6 | 7 | 9 | 120.3 | 133.7 |
PL130X148E | 5 | 7 | 9 | 11 | 130.4 | 147.6 |
PL140X158E | 5 | 7 | 9 | 11 | 140.4 | 157.6 |
PL150X168E | 5 | 7 | 9 | 11 | 150.4 | 167.6 |
(1) Bolt Pitch Circle Diameter dpB、dpS mm
- (When d = Φ10 ~ Φ30 ) dpB = D + 8 + dG dpS = d - 8 - dG
- (When d = Φ32 ~ Φ150 ) dpB = D + 10 + dG dpS = d - 10 - dG
However, if you are mounting a pressure flange to the hub, use 1/2 of the maximum number of bolts allowed or less, so that they may fit into the dpB circumference.
(2) Thickness of Pressure Flange ℓFmm
ℓF ≧ 2 × dG
(3) Strength of Pressure Flange (σ 0.2F)
- When tightening with the torque required for 8.8 bolts. ... σ0.2F ≧ 294 MPa{30kgf/mm2} (S35C equivalent )
- When tightening with the torque required for 10.9 bolts. ... σ0.2F ≧ 343 MPa{35kgf/mm2} (S45C equivalent )
- When tightening with the torque required for 12.9 bolts. ... σ0.2F ≧ 392 MPa{40kgf/mm2} (S55C equivalent )
σ0.2F:Yield point of pressure flange MPa{kgf/mm2}
(4) Functioning Length of the Screw ℓBmm
ℓB ≧ 1.5 × dG
Example of pressure flange processing
X:The number of "Power-Lock" EL Series shaft-hub locking devices provided is based on the minimum space available when the ring between the pressure flange and the hub or shaft is under pressure.
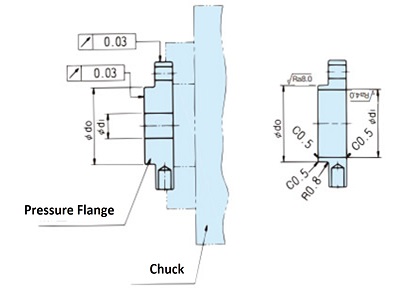