Technical Data Mechanical protectors Handling
Shock Guard TGX Handling
1. Setting Trip Torque
- (1)All TGX Shock Guards are shipped with torque value set at the minimum. Confirm that the Torque scale is set at “0.”
(Refer to the instruction manuals. ) - (2)From the Tightening Amount–Torque Correlation Charts below, find the adjustment nut’s (bolt’s) tightening angle equivalent to the predetermined trip torque. The torque scale is in 60° increments. First, set at 60° toward the determined tightening value, then install onto the machine and conduct a trip test. Gradually tighten and set at the optimum trip torque. Tightening Amount–Torque Correlation Charts should be used as a rough guide only, as the trip torque may not correspond with the chart values.
- (3)After setting the torque, tighten the lock screw on the adjustment nut to prevent loosening.
- (4)Do not exceed the maximum torque scale value when turning the adjustment nut (bolt). Going beyond this limit will cause the disc spring to lose flexibility during trips and become stuck. Click here for lock screw tightening torques and precautions.
Tightening Amount–Torque Correlation Charts
2. Centering
- (1)Centering I
- a. Separate the flange from the boss and center flange.
- b. Move the flange, then set to the I dimensions shown in Table 1. (Table 1)
- c. Fix a dial gauge to the shaft and measure the runout of the hub’s end face and outer circumference.
- (2)Centering II
- a. Separate the flange and the center flange.
- b. Fix a dial gauge to the shaft and measure the runout of the hub’s end face and outer circumference.
- c. Move the boss, then set to the I dimensions shown in Table 1. (Table 1)
Notes | Be sure to secure the Shock Guard using the I dimensions in Table 1. Otherwise, it may not be possible to use the Shock Guard without any backlash. |
Table 1
Model No. | I dimensions mm |
---|---|
TGX10-C | 2 |
TGX20-C | 3 |
TGX35-C | 3 |
TGX50-C | 4 |
TGX70-C | 4 |
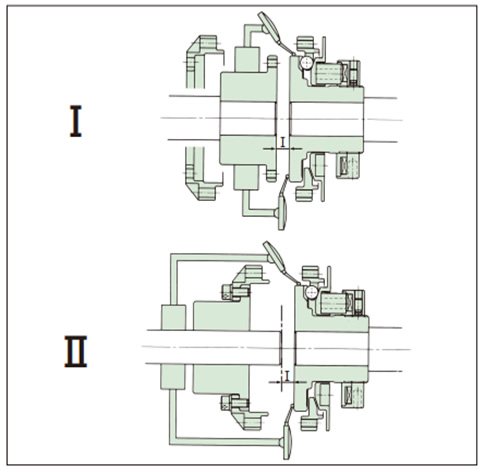
Allowable Misalignment
Model No. | Allowable Misalignment | ||
---|---|---|---|
Angular misalignment deg. | Parallel misalignment mm | End play mm | |
TGX10-C | 0.6 | 0.1 | ±0.5 |
TGX20-C | 0.6 | 0.1 | ±0.5 |
TGX35-C | 0.6 | 0.1 | ±0.5 |
TGX50-C | 0.6 | 0.1 | ±0.6 |
TGX70-C | 0.6 | 0.1 | ±0.7 |
Reference: Hub end face runout per angular misalignment θ = 0.10°
Model No. | Outer Diameter mm | Hub end face runout mm |
---|---|---|
TGX10-C | Φ53 | 0.092 |
TGX20-C | Φ75 | 0.131 |
TGX35-C | Φ98 | 0.171 |
TGX50-C | Φ138 | 0.241 |
TGX70-C | Φ177 | 0.309 |
※Make angular misalignment as small as possible when installing the Shock Guard.
3. shaft bore machining
Refer to the instruction manual for more information on the disassembly, processing, and assembly of the Shock Guard TGX and coupling-type TGX-C when performing bore finishing.
Model No. | Dimensions | |||||
---|---|---|---|---|---|---|
A×Screw diameter | B×Screw diameter | C×Screw diameter | a mm | b mm | c mm | |
TGX10 | 21×M4 or less | - | - | 30 | - | - |
TGX20 | 20.5×M5 or less | - | - | 40 | - | - |
TGX35 | 20.5×M6 | - | - | 55 | - | - |
TGX50 | 24.5×M6 | - | - | 80 | - | - |
TGX70 | 25×M6 | - | - | 100 | - | - |
TGX10-C | - | 8×M4 or less | 21×M4 or less | - | 33 | 30 |
TGX20-C | - | 12×M8 or less | 20.5×M5 | - | 55 | 40 |
TGX35-C | - | 11×M10 or less | 20.5×M6 | - | 70 | 55 |
TGX50-C | - | 13×M10 or less | 24.5×M6 | - | 92 | 80 |
TGX70-C | - | 15×M10 or less | 25×M6 | - | 116 | 100 |
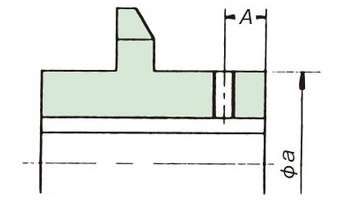
Shock Guard
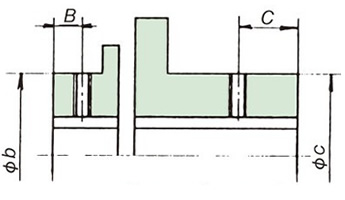
Coupling type
Hold the hub’s end face with a chuck, then center and finish as shown in the diagram below.
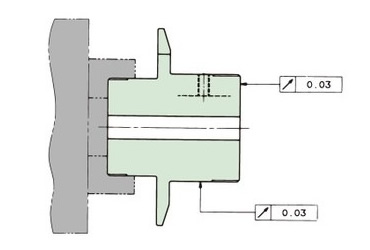
Hold the boss’s flange outer diameter with a chuck, then center and finish as shown in the diagram below.
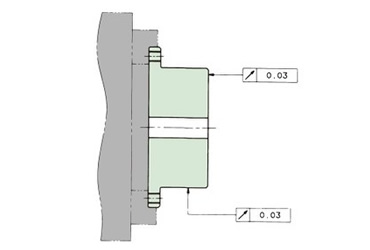