Technical Data Mechanical protectors Handling
Shock Guard TGM Handling
Torque Setting
Precise torque can be set by simply turning the adjustment screw with a hexagon wrench.
- 1. The torque is temporarily set to the minimum torque value at the time of shipment. The front face of the adjustment screw is aligned with the “Min” torque (torque meter line 1) printed on the nameplate. This is the base point at which the adjustment screw is threaded.
- 2. Before setting the torque, Loctite 243 or an equivalent adhesive should be applied to the exposed threads of the adjustment screw. This prevents loosening after setting the torque.
- 3. Refer to the Tightening Amount–Torque Correlation Charts below or the table to the right to determine the adjustment screw tightening angle equivalent to the trip torque. Set at 60° toward the determined tightening value, then install on the machine and perform a trip test. Gradually tighten and set at the optimum trip torque. Tightening Amount–Torque Correlation Charts should be used as a rough guide only, as the trip torque may not correspond with the chart values.
- 4. Do not set the torque lower than the “Min” torque on the nameplate (torque meter line 1). Use a weak spring when a trip torque below the minimum is required.
- 5. Do not turn the adjustment screw when the Shock Guard is disengaged.
- 6. Torque can be set at a Tsubaki factory before shipment if required. (Refer to the instruction manuals. )
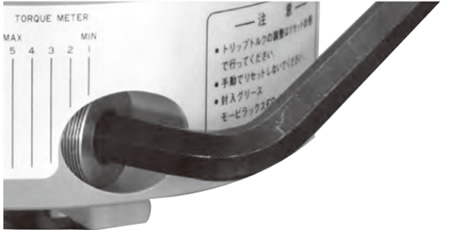
Model No. | Approximate torque per turn N・m{kgf・m} |
Max. turns |
---|---|---|
TGM3 | 0.28 {0.029} | 8 |
TGM6 | 0.48 {0.049} | 8 |
TGM20 | 1.02 {0.10} | 13 |
TGM60 | 4.90 {0.5} | 10 |
TGM200 | 9.80 {1.0} | 16 |
TGM400 | 20.6 {2.1} | 11 |
TGM800 | 41.2 {4.2} | 11 |
Set torque = Min. torque + (Approximate torque per turn × Number of adjustment screw turns )
Tightening Amount–Torque Correlation Charts
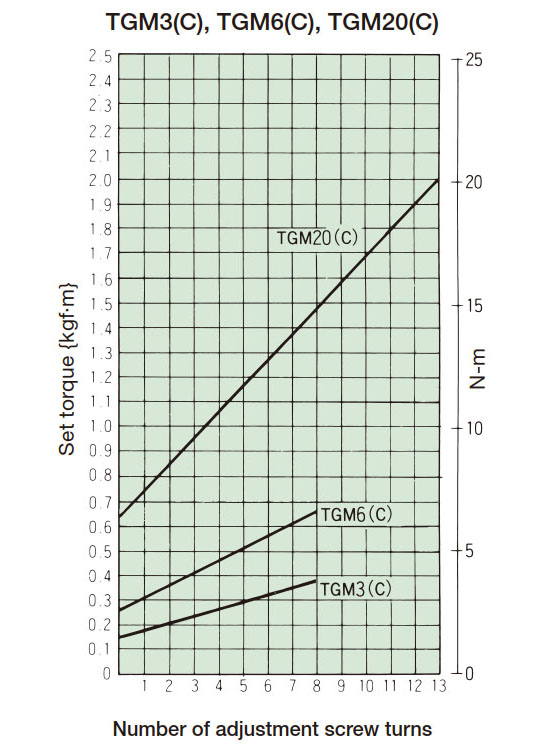
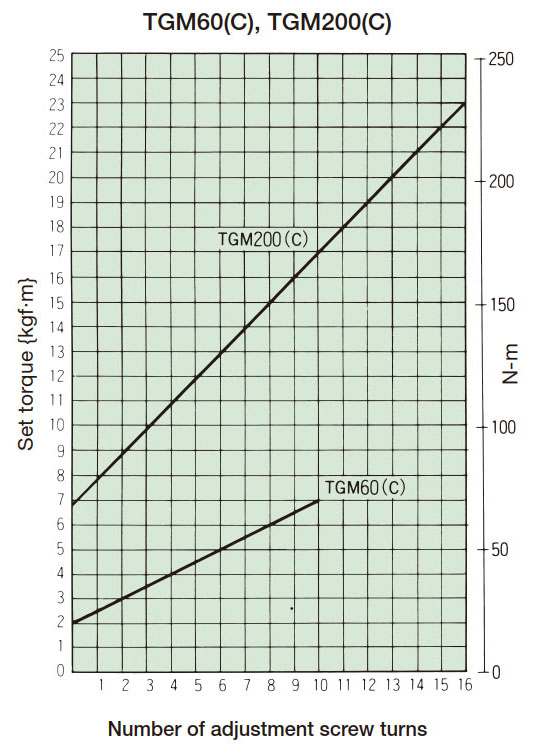
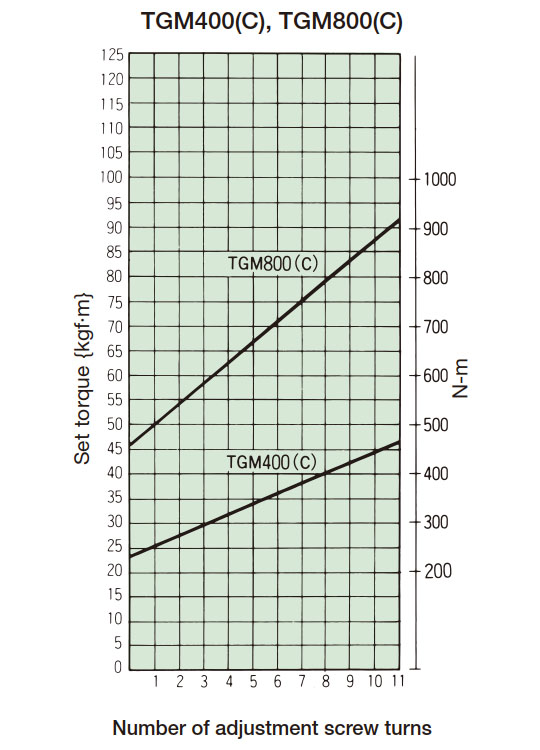
Overload detection
Overload is easily detected by the limit switch.
When the Shock Guard trips due to overload, the cam follower disengages from the pocket, and the cam shaft and main unit (case) will rotate freely.
At the same time, the LS detecting plate moves in the axial direction.
The limit switch detects this movement and shuts off the power or triggers the warning alarm.
The overload can be detected whether the stop side is on the cam shaft side or the main unit (case) side.
The LS detecting plate slides three times for each trip.
- (1)Table 1 shows LS detecting plate travel and force during tripping. Select a limit switch that meets the PT (pre-travel) and OF (operating force) requirements.
- (2)Figures 1 and 2 show limit switch installation examples.
- (3)Connect the limit switch’s “b” contact parallel to the start button’s contact.
- (4)Figure 3 shows an example of a typical circuit. Tsubaki recommends using a self-holding circuit.
Model No. | Travel mm | Force during travel N{gf} |
---|---|---|
TGM3 | 4 | 3.9 {400} |
TGM6 | 4 | 3.9 {400} |
TGM20 | 4 | 3.9 {400} |
TGM60 | 6 | 3.9 {400} |
TGM200 | 6 | 5.4 {550} |
TGM400 | 8 | 5.9 {600} |
TGM800 | 8 | 5.9 {600} |
・Limit Switch Installation Example
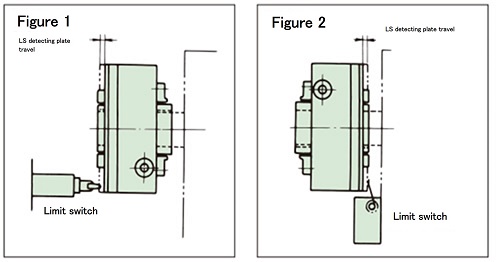
・Circuit Example
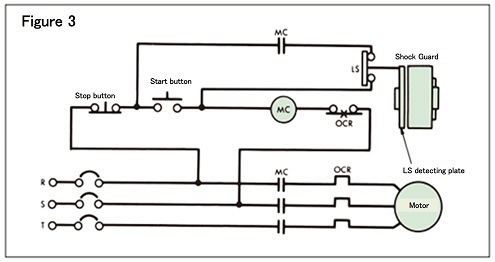
Mounting
1. Installing to the shaft
- ・We recommend a shaft diameter tolerance of h7 for mounting the Shock Guard to the shaft. Use a JIS 1301-1996 (new JIS standard) parallel key.
Allow some clearance between the top of the key and keyway. - ・When fixing the Shock Guard to the shaft, tighten bolts in three places on the cam actuation plate. (one for the key, and two for the shaft )
- ・Depending on the installation method, such as mounting the Shock Guard to the end face of the shaft, the set bolts for the cam actuation plate may not be usable. In this case, use the tapped holes on the mounting seat side.
Set bolts for these tapped holes are not supplied, so use bolts with a length that fits the bore diameter.
Make sure that the head of the set bolts does not extend beyond the cam shaft end. If the head of the screws protrudes, they will interfere with the inner diameter and sides of the mounting seats when the Shock Guard trips. - ・Loctite 243 or equivalent should be used to prevent loosening if there is a possibility that vibration during operation may cause the bolts to loosen.
2. Installing a drive member
- ・To install drive members like sprockets, pulleys, gears, and couplings, use the three mounting seats and tighten the bolts with the torque shown in Table 2.
- ・Refer to the instruction manual for sprocket installation. If you need to use a Tsubaki Power-Lock (keyless locking device) or a backlash-free coupling, contact a Tsubaki representative.
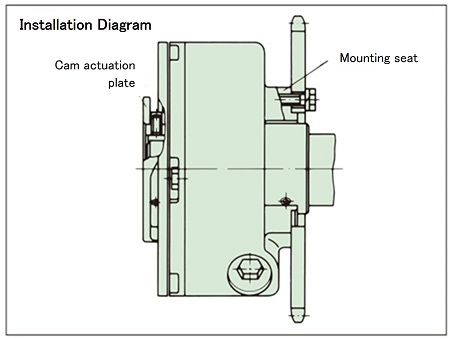
3. Mounting Bolt
Table 2 lists the recommended screw-in lengths and tightening torques for bolts attached to the case’s mounting seat.
The bolt pilot bores should have a JIS grade of B10012 or lower.
Model No. | Bolt screw-in length mm | Bolt tightening torque N・m{kgf・m} | Pilot bore dia. for mounting bolt mm |
---|---|---|---|
TGM3 | 6~7 | 2.0~2.9 {0.2~0.3} | 4.5 |
TGM6 | 6~7 | 2.0~2.9 {0.2~0.3} | 4.5 |
TGM20 | 8~9 | 3.9~5.9 {0.4~0.6} | 5.5 |
TGM60 | 9~11 | 6.9~11 {0.7~1.1} | 6.6 |
TGM200 | 15~17 | 34~51 {3.5~5.2} | 11.0 |
TGM400 | 18~25 | 59~89 {6.0~9.1} | 14.0 |
TGM800 | 18~25 | 59~89 {6.0~9.1} | 14.0 |
4. Connecting
The input/output connection is placed between the variator, reducer, or intermittent drive device and the machine/device.
Figures 4, 5, and 6 show typical connecting examples.
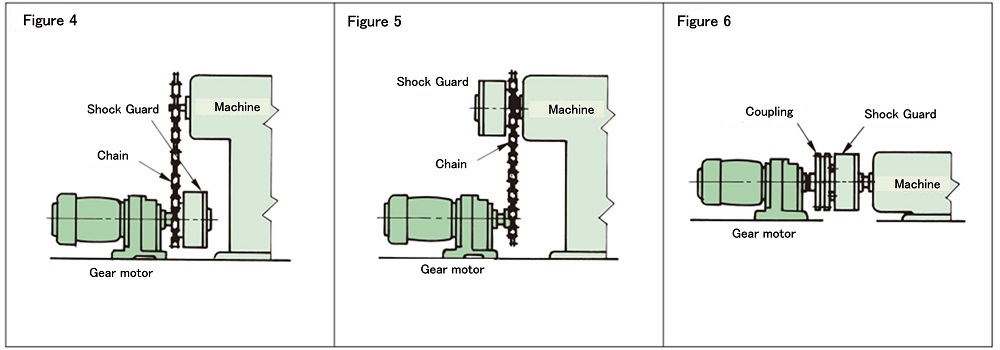
Resetting
Auto-resetting type only requires restarting the motor and other parts of the drive unit to reengage.
- 1. When the Shock Guard trips due to overload, stop the motor and remove the cause of the overload.
- 2. Reset with an input rpm of 50 or less by “jogging” the motor.
To avoid injury, do not reset the Shock Guard main unit or the shaft by hand. - 3. A distinct clicking sound is made when the cam follower settles in its pocket.
Lubrication
The TGM Series is sealed with high-quality grease before shipment and does not require additional lubrication under normal operating conditions.
EXXON MOBILE | MOBILUX EP-2 |
---|
*The above product name is a trademark of Exxon Mobil JAPAN.