Technical Data Mechanical protectors Handling
Shock Guard TGB Handling
1. Setting Trip Torque
- (1)All TGB Shock Guards are shipped with torque value set at the minimum. Confirm that the Torque scale is set at “0.”
(Refer to the diagrams for each size. ) - (2)For TGB70 to TGB130, loosen the lock nuts on the three adjustment bolts. (The adjustment nuts of TGB08 to TGB50 can be turned as is. )
- (3)From the Tightening Amount–Torque Correlation Charts below, find the adjustment nut’s (bolt’s) tightening angle equivalent to the predetermined trip torque. First, set at 60° toward the determined tightening value, then install onto the machine and conduct a trip test. Gradually tighten and set at the optimum trip torque. Tightening Amount–Torque Correlation Charts should be used as a rough guide only, as the trip torque may not correspond with the chart values.
- (4)For TGB20 to TGB50, tighten the lock screw on the adjustment nut to prevent loosening. For TGB70 to TGB130, tighten the hexagon nut to prevent loosening.
(The adjustment nut on TGB08 to TGB16 is coated to prevent loosening. ) - (5)Do not exceed the maximum torque scale value when turning the adjustment nut (bolt). Going beyond this limit will cause the disc spring to lose flexibility during trips and become stuck. (TGB08 to TGB16 use coil springs. )
2. Tightening Amount–Torque Correlation Charts
3. shaft bore machining
TGB08~16
・The boss is made of iron-based sintered alloy and the surface is hardened.
- (1)Loosen the adjustment nut to disassemble all components. Make sure not to get any dust or dirt on the components.
- (2)Chuck the outer diameter of the boss flange portion and center at the boss portion. The hub’s material is a surface-hardened ironbased sintered alloy, so we recommend using a carbide cutting tool (JIS 9-20, K-01).
- (3)Machine the keyway just under the tap for the set screw.
- (4)After bore finishing, apply grease to the drive balls and thrust bearing before reassembling.
- (5)For shaft bore step machining please refer to the table and diagram below.
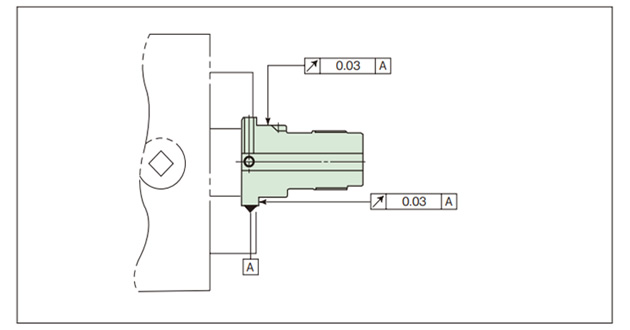
Model No. | Shaft Bore Diameter Φd mm |
Length of Machinable Shaft Bores L mm |
Counterbore diameter ΦD mm |
---|---|---|---|
TGB08 TGB08-C |
Φ6≦ and ≦Φ8 | 20 | Φ11 |
TGB12 TGB12-C |
Φ7 or more, less than Φ10 | 20 | Φ15 |
Φ10 or more, less than Φ12 | 30 | ||
Φ12 | Total length | Not necessary | |
TGB16 TGB16-C |
Φ8 or more, less than Φ10 | 20 | Φ15 |
Φ10 or more, less than Φ12 | 30 | ||
Φ12 or more, Φ10 or less | Total length | Not necessary |
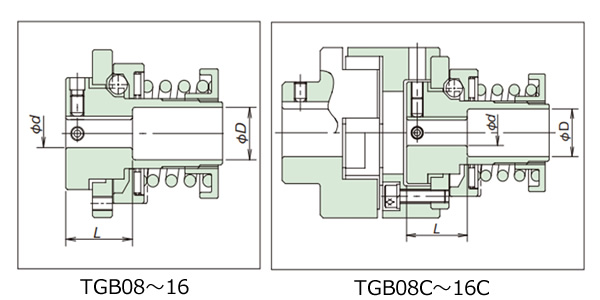
TGB20~130
・The boss has undergone a thermal refining process.
- (1)Loosen the adjustment nut to disassemble all components.
Remove the shaft’s snap ring and the center flange. Make sure not to get any dust or dirt on the components. - (2)Chuck the outer diameter of the boss flange portion and center at the boss portion.
- (3)Tapping for the set screws should be machined so they are spaced 90° from each other around the keyway.
- (4)After bore finishing, apply grease to the drive balls and thrust bearing before reassembling.
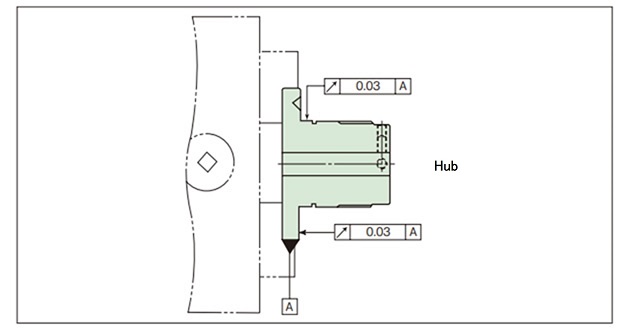
4. Resetting
Auto-resetting type only requires restarting the motor and other parts of the drive unit to reengage.
- (1)When the Shock Guard trips due to overload, stop the motor and remove the cause of the overload.
- (2)Reset the Shock Guard and operate at less than 50 r/min or by “jogging” the motor.
⚠Do not manually reset the Shock Guard by turning the main unit or shaft as this can be dangerous.
- (3)Clicking sounds indicate that the drive balls have rolled back into the pockets.