Technical Data Mechanical protectors Handling
Torque Keeper TFK Handling
Handling 1
- 1. The Torque Keeper is shipped with pilot bores. Finish bore after disassembly. Click here for bore finishing.
- 2. When disassembling two or more Torque Keepers, it is important to label the parts to avoid mixing them up. When reassembling, use the labeled parts to ensure that the Torque Keeper is reassembled correctly. If the parts are mixed up, the torque curve will not match the actual slipping torque.
- 3. When using the Torque Keeper with belt and chain drives, such as timing belts and roller chains, be careful not to overtighten, as this can prevent a stable slipping torque.
Handling 2
The Torque Keeper is set at 50% of the maximum torque range (refer to each product pages) and is shipped with the corresponding torque curve.
This 50% torque is called the “zero point” and it is the basis for setting the slipping torque.
To set the slipping torque of TFK20/25/35, tighten the adjustment nut with a hook wrench. To set the slipping torque of TFK50/70, tighten the three adjustment bolts with a wrench. Refer to the below to determine the zero point.
Setting the slip torque
TFK20・25・35
- (1)When the required slipping torque is above the zero point, tighten the adjustment nut to the angle required, following the provided torque curve. This operation is facilitated by the torque scale (which shows the angle) and matchmarks.
- (2)When the required slipping torque is below the zero point, loosen the adjustment nut beyond the point required and then tighten it to the desired angle, following the provided torque curve.
(ex. )Set to a slipping torque –30° from the zero point.
- 1.Loosen the adjustment nut to –60° from the zero point.
- 2.Tighten the adjustment nut from –60° to –30°.
TFK20・25・35 Torque indicator
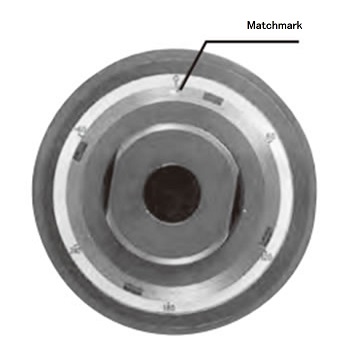
TFK50・70
- (1)When the required slipping torque is over the zero point, tighten the three adjustment bolts to the angle required, following the provided torque curve. This operation is facilitated by the torque scale (which shows the angle) and matchmarks.
- (2)When the required slipping torque is below the zero point, loosen the three adjustment bolts beyond the point required and then tighten them to the desired angle, following the provided torque curve.
(ex. )Set to a slipping torque –60° from the zero point.
- 1.Loosen the adjustment bolts to –90° from the zero point.
- 2.Tighten the adjustment bolts from –90° to –60°.
TFK50・70 Torque indicator
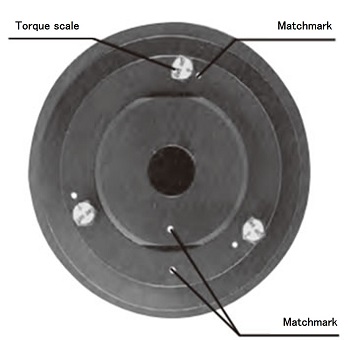
(Note )When initially setting the Torque Keeper or changing the setting during operation, it is recommended that the machine be run for two or three minutes before normal operation. This will result in a more stable slipping torque. Running-in is performed based on the set slipping torque according to the following procedure.
(1)When the slipping torque is below the zero point:
- 1. Run in the machine at zero-point torque for two to three minutes.
- 2. Set the slipping torque as explained above and then begin normal operation.
(2)When the slipping torque is above the zero point:
- 1. Set the slipping torque as explained above.
- 2. Run in the machine for two to three minutes.
- 3. Return the adjustment nut or bolts to the zero point.
- 4. Set the slipping torque again and then begin normal operation.
Torque Curve (common to coupling type )
Weak spring type
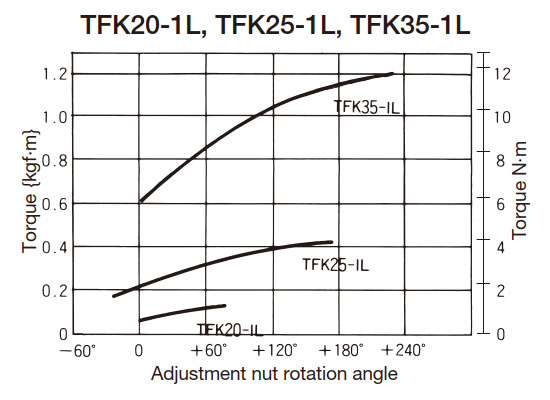
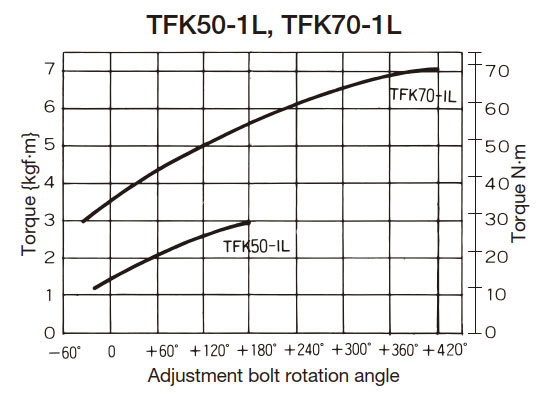
Standard spring models { } is for reference.
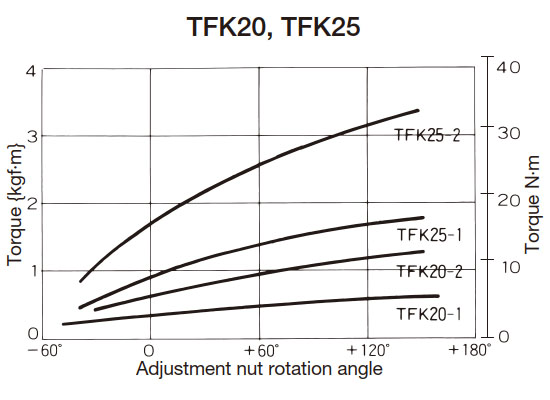
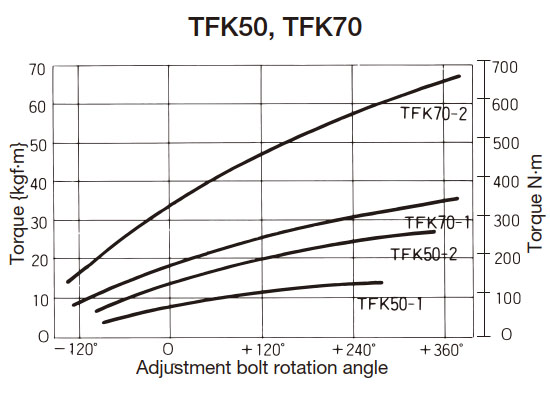
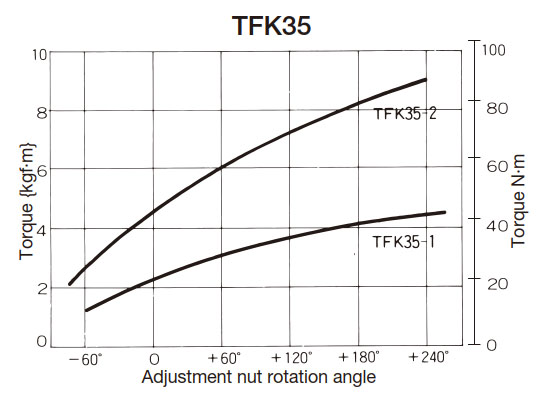
Finding the Zero Point
After finishing the shaft bore and reassembling the unit, determine the zero point as explained below:
TFK20・25・35
- 1. During reassembly, match the “0” on the torque scale with the position of the set screw on the hub (part ⑧ click here). (Make sure it is not positioned 180° in the opposite direction. )
- 2. Hand-tighten the adjustment nut and then use a hook wrench to further tighten it until the matchmark reaches the “0” position on the torque scale.
TFK50・70
- 1. Tighten the adjustment nut and align it with the matchmark on the hub.
- 2. Hand-tighten the bolts and then use a wrench to further tighten them until the “0” position on the indicators align with the matchmarks.
- Note) 1. Indicator 0 on the torque curve shows 50% of maximum torque.
- Note) 2. Each torque curve is an example. Refer to the attached torque curve of the actual unit.