Technical Data Coupling Handling
ECHT-FLEX Coupling NEF / NEHSeries Handling
Centering
(1) Single hub / Spacer type
The more accurate the initial centering of the coupling, the less stress it will experience during operation.
Wear of the shaft bearing, depressions in the mounting surface, changes in conditions affected by temperature and vibration can reduce the life of the coupling and your equipment.
Center accurately and conduct periodic adjustment according to the following procedure.
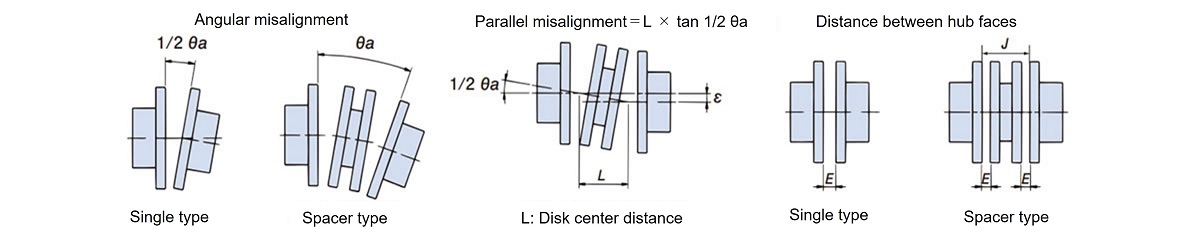
Parallel misalignment (Parallel Misalignment ) = L×tan 1/2 θa L:Disk center distance = J - E
Note: The single type coupling cannot absorb parallel misalignment (parallel misalignment of the shaft center).
The allowable angular misalignment, parallel misalignment, and error in the distance between the coupling’s flange faces are all correlated to each other. Increasing one factor decreases the others, so the factors need to be considered together. Perform the initial centering adjustment carefully so that the following recommended value is not exceeded.
Model No. | Angular misalignment (Angular Misalignment ) | Parallel misalignment (Parallel Misalignment ) ε[mm] |
Hub face distance misalignment E[mm] |
|
---|---|---|---|---|
1/2 θ a [deg] |
Dial reading | |||
NEF02S | 0.25 | 0.25 | ※(Note ) Errors cannot be absorbed. |
4.9±0.25 |
NEF04S | 0.25 | 0.29 | 6.1±0.25 | |
NEF10S | 0.25 | 0.35 | 6.6±0.25 | |
NEF18S | 0.25 | 0.40 | 8.3±0.25 | |
NEF25S | 0.25 | 0.45 | 11.2±0.25 | |
NEF45S | 0.25 | 0.55 | 11.7±0.25 | |
NEF80S | 0.25 | 0.62 | 11.7±0.25 | |
NEF130S | 0.25 | 0.73 | 16.8±0.25 | |
NEF210S | 0.25 | 0.84 | 17.0±0.25 | |
NEF340S | 0.25 | 0.93 | 21.6±0.25 | |
NEF540S | 0.25 | 1.07 | 23.9±0.25 | |
NEF700S | 0.25 | 1.20 | 27.2±0.25 |
※Note ) The single type is structurally unable to absorb parallel misalignment, but should be adjusted to within 0.02 mm during centering.
Model No. | Angular misalignment (Angular Misalignment ) | Parallel misalignment (Parallel Misalignment ) ε[mm] |
Hub face distance misalignment E[mm] |
|
---|---|---|---|---|
θ a [deg] |
Dial reading T.I.R.[mm] |
|||
NEF02W | 0.5 | 0.50 | 0.075 | 4.9±0.25 |
NEF04W | 0.5 | 0.58 | 0.13 | 6.1±0.25 |
NEF10W | 0.5 | 0.71 | 0.14 | 6.6±0.25 |
NEF18W | 0.5 | 0.81 | 0.17 | 8.3±0.25 |
NEF25W | 0.5 | 0.91 | 0.18 | 11.2±0.25 |
NEF45W | 0.5 | 1.10 | 0.22 | 11.7±0.25 |
NEF80W | 0.5 | 1.25 | 0.25 | 11.7±0.25 |
NEF130W | 0.5 | 1.46 | 0.27 | 16.8±0.25 |
NEF210W | 0.5 | 1.69 | 0.31 | 17.0±0.25 |
NEF340W | 0.5 | 1.86 | 0.33 | 21.6±0.25 |
NEF540W | 0.5 | 2.14 | 0.37 | 23.9±0.25 |
NEF700W | 0.5 | 2.41 | 0.46 | 27.2±0.25 |
NEH09W | 0.35 | 1.68 | 0.30 | 19.0±0.25 |
NEH14W | 0.25 | 1.20 | 0.30 | 19.0±0.25 |
NEH20W | 0.25 | 1.34 | 0.33 | 19.0±0.25 |
NEH30W | 0.25 | 1.50 | 0.36 | 21.5±0.25 |
NEH41W | 0.25 | 1.64 | 0.43 | 24.0±0.25 |
NEH55W | 0.25 | 1.94 | 0.50 | 29.5±0.25 |
NEH70W | 0.25 | 2.05 | 0.51 | 31.3±0.25 |
NEH90W | 0.25 | 2.23 | 0.55 | 32.0±0.25 |
NEH110W | 0.25 | 2.43 | 0.55 | 32.5±0.25 |
NEH135W | 0.25 | 2.56 | 0.60 | 34.0±0.25 |
NEH150W | 0.25 | 2.74 | 0.65 | 34.5±0.25 |
NEH180W | 0.25 | 2.85 | 0.70 | 35.5±0.25 |
(2) Long spacer type
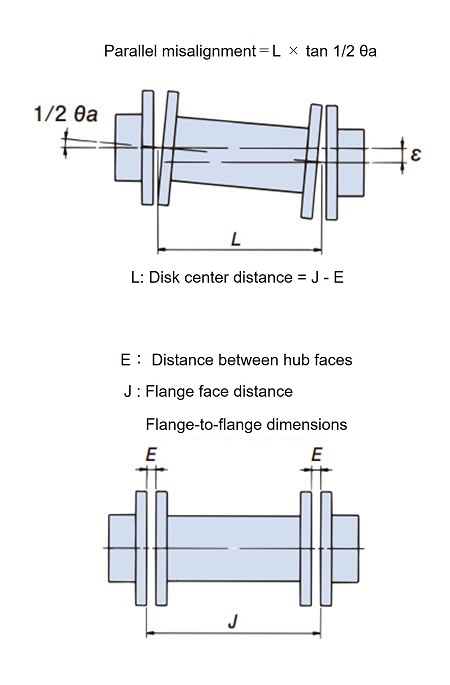
Model No. | Angular misalignment (Angular Misalignment ) | Parallel misalignment (Parallel Misalignment ) ε[mm] |
Hub face distance misalignment E[mm] |
|
---|---|---|---|---|
θ a [deg] |
Dial reading T.I.R.[mm] |
|||
NEF04W | 0.5 | 0.58 | L×0.43×10-2 | 6.1±0.25 |
NEF10W | 0.5 | 0.71 | L×0.43×10-2 | 6.6±0.25 |
NEF18W | 0.5 | 0.81 | L×0.43×10-2 | 8.3±0.25 |
NEF25W | 0.5 | 0.91 | L×0.43×10-2 | 11.2±0.25 |
NEF45W | 0.5 | 1.10 | L×0.43×10-2 | 11.7±0.25 |
NEF80W | 0.5 | 1.25 | L×0.43×10-2 | 11.7±0.25 |
NEF130W | 0.5 | 1.46 | L×0.43×10-2 | 16.8±0.25 |
NEF210W | 0.5 | 1.69 | L×0.43×10-2 | 17.0±0.25 |
NEF340W | 0.5 | 1.86 | L×0.43×10-2 | 21.6±0.25 |
NEF540W | 0.5 | 2.14 | L×0.43×10-2 | 23.9±0.25 |
NEF700W | 0.5 | 2.41 | L×0.43×10-2 | 27.2±0.25 |
NEH09W | 0.35 | 1.68 | L×0.31×10-2 | 19.0±0.25 |
NEH14W | 0.25 | 1.20 | L×0.22×10-2 | 19.0±0.25 |
NEH20W | 0.25 | 1.34 | L×0.22×10-2 | 19.0±0.25 |
NEH30W | 0.25 | 1.50 | L×0.22×10-2 | 21.5±0.25 |
NEH41W | 0.25 | 1.64 | L×0.22×10-2 | 24.0±0.25 |
NEH55W | 0.25 | 1.94 | L×0.22×10-2 | 29.5±0.25 |
NEH70W | 0.25 | 2.05 | L×0.22×10-2 | 31.3±0.25 |
NEH90W | 0.25 | 2.23 | L×0.22×10-2 | 32.0±0.25 |
NEH110W | 0.25 | 2.43 | L×0.22×10-2 | 32.5±0.25 |
NEH135W | 0.25 | 2.56 | L×0.22×10-2 | 34.0±0.25 |
NEH150W | 0.25 | 2.74 | L×0.22×10-2 | 34.5±0.25 |
NEH180W | 0.25 | 2.85 | L×0.22×10-2 | 35.5±0.25 |
Relationship between parallel misalignment and angular misalignment for the spacer type coupling
Parallel misalignment (Parallel Misalignment )
(Amount of parallel misalignment per unit length in distance between disk centers L. )
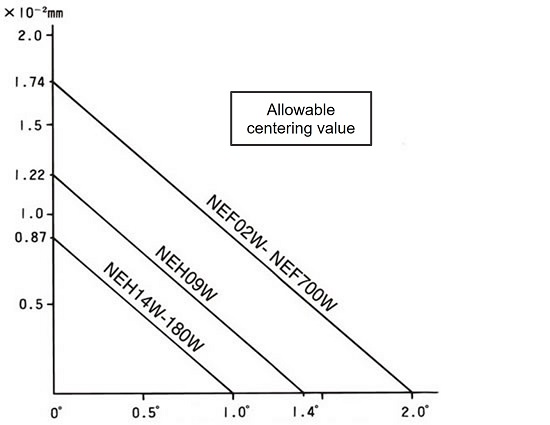
Allowable angular misalignment (Angular Misalignment )(θa)
Parallel misalignment (Parallel Misalignment )
(Amount of parallel misalignment per unit length in distance between disk centers L. )
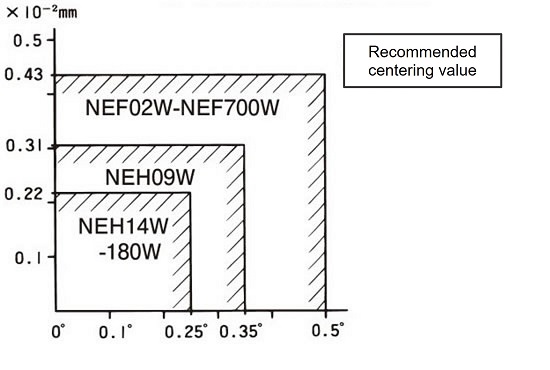
Allowable angular misalignment (Angular Misalignment )(θa)
- (1) Adjusting the hub-to-hub dimension “E”
For both the Spacer Type and Single Type couplings, measure dimension “E” at four places (at 90° angles), and adjust the hub position so that the average value of dimension “E” is within ±0.25 mm.
When a stepped shaft is used for both the drive and driven shafts, the margin for adjustment may be limited. In this case, give consideration in advance so that dimension “E” can be adjusted.
- (2) Adjusting the angular misalignment (θ°)
- (a) With a dial gauge fixed to one of the hubs as shown above, rotate the hub to find the minimum indication on the dial gauge, and set that to “0”.
- (b) Rotate the hub with the dial gauge 360°, and read the value for the angular misalignment.
- (c) Adjust the equipment by moving it with a shim so that the reading on the dial gauge comes within the recommended angular misalignment range specified in the table above.
- (3) Adjusting the parallel misalignment “ε” (mm)
- (a) With a dial gauge fixed to the hub flange as shown above, rotate the hub to find the minimum indication on the dial gauge, and set that to “0”.
- (b) Rotate the hub with the attached dial gauge 360 degrees, and read the parallel misalignment value.
- (c) The reading on the dial gauge around the periphery of the hub flange may fluctuate markedly at the hub’s drilled bore. This is because the flange is displaced toward the periphery while machining the drilled bore. When reading the dial gauge, disregard the values at such locations.
- (d) Adjust the equipment by moving it with a shim so that the reading on the dial gauge comes within twice the recommended parallel misalignment (ε) range specified in the table.
- (e) If the equipment is moved for the purpose of parallel misalignment adjustment, perform the angular misalignment adjustment procedure once again.
- (4) Repeat the above adjustment procedures until all of the coupling’s displacement values are acceptable.
- (5) Tighten all the U-nuts to the torque specified below.
ECHT-FLEX Couplings transmit torque using the frictional force generated between the disk and washer by the U-nut’s fastening force.
Always use the U-nut tightening torque specified below.
1. Reamer bolt tightening torques
ECHT-FLEX Couplings transmit power using the frictional force of the reamer bolts and U-nuts.
Tighten the reamer bolts and U-nuts securely with the specified torque.
Model No. | Reamer bolt tightening torque [N・m] |
Reamer bolt size | |
---|---|---|---|
NEF02 | 4.90 | M5 | |
NEF04 | 8.82 | M6 | |
NEF10 | 8.82 | M6 | |
NEF18 | 21.6 | M8 | |
NEF25 | 21.6 | M8 | |
NEF45 | 41.2 | M10 | |
NEF80 | 78.4 | M12 | |
NEF130 | 78.4 | M12 | |
NEF210 | 177 | M16 | |
NEF340 | 177 | M16 | |
NEF540 | 470 | M20 | |
NEF700 | 657 | M24 | |
NEH09 | 470 | M20 | |
NEH14 | 568 | M22 | |
NEH20 | 784 | M24 | |
NEH30 | 1170 | M27 | |
NEH41 | 1590 | M30 | |
NEH55 | 2250 | M36 | |
NEH70 | 2550 | M36 | |
NEH90 | 3230 | M39 | |
NEH110 | 3920 | M42 | |
NEH135 | 4900 | M45 | |
NEH150 | 5490 | M48 | |
NEH180 | 6860 | M52 |
Model No. | Reamer bolt A Tightening torque [N・m] |
Reamer bolt A Size |
Reamer bolt B Tightening torque [N・m] |
Reamer bolt B Size |
||||
---|---|---|---|---|---|---|---|---|
NEF45G | 41.2 | M10 | 8.82 | M6 | ||||
NEF80G | 78.4 | M12 | 21.6 | M8 | ||||
NEF130G | 78.4 | M12 | 21.6 | M8 | ||||
NEF210G | 177 | M16 | 41.2 | M10 | ||||
NEF340G | 177 | M16 | 41.2 | M10 | ||||
NEF540G | 470 | M20 | 78.4 | M12 | ||||
NEF700G | 657 | M24 | 78.4 | M12 | ||||
NEH09G | 470 | M20 | 78.4 | M12 | ||||
NEH14G | 568 | M22 | 78.4 | M12 | ||||
NEH20G | 784 | M24 | 177 | M16 | ||||
NEH30G | 1170 | M27 | 177 | M16 | ||||
NEH41G | 1590 | M30 | 470 | M20 |
Size | M5 | M6 | M8 | M10 | M12 | M16 | M20 | M22 | M24 |
---|---|---|---|---|---|---|---|---|---|
S | 8 | 10 | 13 | 17 | 19 | 24 | 30 | 32 | 36 |
Size | M27 | M30 | M36 | M39 | M42 | M45 | M48 | M52 | |
S | 41 | 46 | 55 | 60 | 65 | 70 | 75 | 80 |
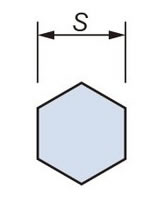
2. Tightening the reamer bolt
When tightening the reamer bolts, be careful not to apply an axial force to the coupling hub. If an axial force is applied to the hub, the disk may warp and become fixed in that warped state.
Tighten the reamer bolts securely with the torque specified in the table above.
- ・The U-nut is made of metal. It can be mounted and dismounted up to 20 times. If you will need to mount and dismount the U-nut more than 20 times, keep a spare U-nut on hand.
- ・There is no need to apply oil or grease to reamer bolts
- ・The reamer bolt can be inserted in either direction.
3. Removing the coupling
The Spacer Type coupling can be removed from the shaft without running the drive or driven equipment. This feature considerably simplifies centering adjustment when re-mounting the coupling.
[Removal procedure ]
- 1. Loosen all reamer bolts and remove the disks and spacers. (Fig. 1)
- 2. Loosen the set bolt that fastens the hub, and then slide the hub off to remove it. (Fig. 2)
- 3. To re-mount the coupling, perform the above steps in reverse order. After both hubs are mounted to the shaft, it is recommended that you check the centering level to verify the mounting state.
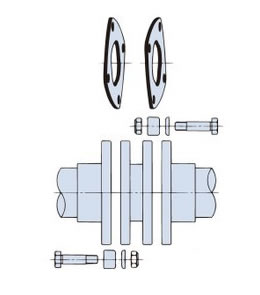
Fig. 1
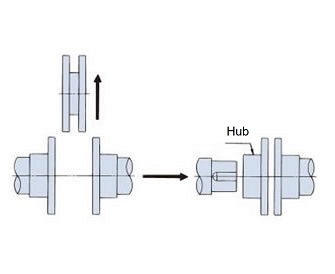
Fig. 2
4. Inspection
After operating the equipment for one or two hours, check the angular misalignment and the parallel misalignment once again. At this time, re-tighten the bolts and nuts with the torque specified in the table above.
Once the equipment has been in operation for 6 months or one year, check the reamer bolts and U-nuts for looseness. It is recommended that you mark the reamer bolts and U-nuts at the time of installation so that you can check for looseness later on. Be sure to check for any abnormalities in other components as well.