Technical Data Reducers Worm Gear Reducers Selection
To view selection procedures and precautions, please proceed to the following.
Click here to narrow down the product series or to make a tentative selection.
If you have specific conditions of use and wish to make a detailed selection, please click here.
Selection procedure
First, identify the selection table in the flowchart.
Follow these procedures for sizing a TD series reducer, or when the operating conditions in “Sizing table 3” fall outside sizing table 1 or 2 for a EWJ/EW/SWJ/SW series reducer.
These conditions are necessary for sizing: load torque or transfer kW, input speed, reduction ratio, load characteristics, operating hours, start/stop frequency, etc.
1. Determine compensation factor
The transfer capacities listed in Sizing Table 3 are based on a service factor (Sf) of 1.0. Choose either service factor (Sf) or thermal rating factor (only applicable to the EWJ/EW/SWJ/SW series) depending on the load characteristics, operating hours, and start frequency. Use the larger value as the compensation factor. Refer to the table of Load Categories by Machine Type for the load characteristics. If you cannot find your machine, choose the closest or contact us for assistance.
Table 1 Service factor table (Sf)
Load characteristics | Operating hours (per day) | ||
---|---|---|---|
2 | 10 | 24 | |
U:Constant load | 1.00 (1.25) |
1.00 (1.25) |
1.25 (1.50) |
M:Load with light impact | 1.00 (1.25) |
1.25 (1.50) |
1.50 (1.75) |
H:Load with heavy impact | 1.25 (1.50) |
1.50 (1.75) |
1.75 (2.00) |
Note
- 1)Use the figure within ( ) if the reducer is to be started more than 10 times per hour.
- 2)The above table shows rough service factor standards Decide on the service factor according to the operating conditions.
Table 2 .Thermal rating factor (EWJ/EW/SWJ/SW series)
Input speed r/min |
Size | Reduction ratio Operating hours |
Thermal rating factor |
---|---|---|---|
1750, 1450 | EWJ25 ~ 70 SWJ25 ~ 42 |
1/10 ~ 1/60 Continuous 1 hour or more |
1.3 |
SWJ50 ~ 70 | 1.15 | ||
1750, 1450 | EW80 ~ 200 SW80 ~ 200 |
1/10 ~ 1/60 Continuous 2 hours or more |
1.5 |
1150, 950 | EW80 ~ 200 SW80 ~ 200 |
1.15 | |
For any other size | 1.0 |
2. Determine compensation kW and compensation torque
Use the compensation kW or compensation torque to calculate formula 1.
Design kW = load kW × Correction factor ........(Formula 1 )
Correction torque = Load torque × Correction factor ...(Formula 1 )
3. Determination of reduction ratio
Use the actual input speed you will be using, and the required output speed to determine the reduction ratio. Contact us if you wish to drive the input faster than 1750 r/min.
The reduction ratios for TD Series are given as nominal reduction ratios. Please refer to the actual reduction ratios for single reduction reducers, or for double reduction reducers.
4. Determine size and model
From the Transfer Capacity table, select the size and model that satisfies the compensation kW or compensation torque.
If the reducer is to be driven slower than 100 r/min, select from the output torque column for 100 r/min.
Note these factors when sizing a TD series reducer.
[Equivalent thermal capacity :TD Series ]
Determine the temperature compensation factor (f1) from the actual ambient temperature and temperature compensation factor table (Table 3). Calculate the equivalent thermal capacity, then use formula 2 to check that it is within the capacity in the Transfer Capacity table.
Equivalent thermal capacity = load kW (or torque) × f1......(Formula 2 )
Table 3. Temperature compensation factors (f1) (TD Series )
Ambient Temperature | Temperature compensation factors |
---|---|
30°C or lower | 1.0 |
40°C or lower | 1.3 |
50°C or lower | 1.5 |
5. Check shaft load
Use formula 3 to check that the radial load on the shaft is within the allowable radial load for each series.
Allowable Radial Load (N{kgf})≧ T × f × Lf R ...(Formula 3 )
- T:Correction torque (N・m {kgf・m})
- f:O.H.L. factors (Table on the right )
- Lf:Point of action factor (Table on the right )
- R:Pitch radius (m) of sprockets and pulleys (m)
O.H.L. factors (f)
Chain | 1.00 |
---|---|
Gears Toothed belt |
1.25 |
V-Belt Tough toothed belt |
1.5 |
Solid shaft type
Point of action factor (Lf)
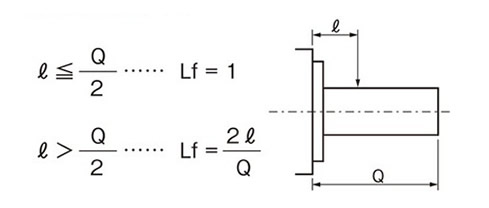
Hollow shaft type
Point of action factor (Lf)
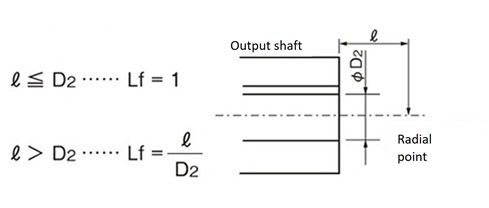
Check axial load
If axial loads are anticipated on the output shaft, make sure they are within the allowable axial loads for each series.
Contact us if radial and axial loads occur simultaneously
Alternating loads
In situations where alternating loads are frequently applied, such as with index driving, there is a risk of unexpected trouble due to the backlash of the reducer and the looseness of fastening parts.
When considering such applications, enter the usage conditions on the Inquiry Form for Selection and contact us for details.
6. Calculate required input kW
Required input kW = Rated input kW × Load torque Rated Output Torque × Sf