Technical Data Drive chain Glossary of technical terms
1. JIS minimum tensile strength (Tensile breakage strength)
This is the minimum tensile strength determined by ASME standard. If a roller chain breaks from a tensile load below this value, then it is non-compliant. With multi-strand roller chain, the single strand value is multiplied by the number of strands. (JIS B 1801 : 2014)
These roller chains are also ISO-compliant. (ISO 606 : 2004)
2. Min. tensile strength
This is a minimum value determined by statistical processing at Tsubaki. If any roller chain fractures by a tensile load below this value, then it is non-compliant. This value varies depending on the manufacturer.
Testing method
As shown in Fig. 1, a roller chain with over five links is fixed at both ends by clevises and is stretched until breakage occurs. (JIS B 1801 : 2014)
The type of fracture is indicated by breakage of the roller chain or failure of its parts (Fig. 2.)
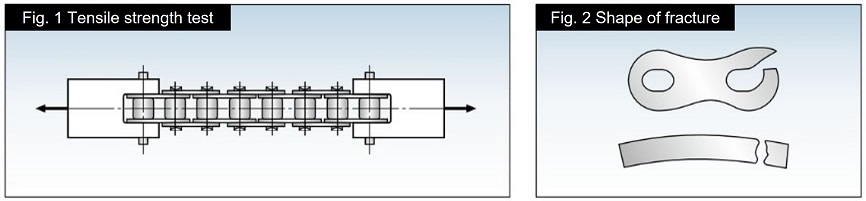
3. Max. allowable load
The maximum allowable load of roller chain (excluding Stainless Steel Chain and Engineering Plastic Chain*) is the value derived from the lowest fatigue limit. When a load lower than this value is repetitively applied to the roller chain, fatigue failure will never occur.
Under the JIS B 1811:2018 standard, the maximum allowable load indicates a test load of Fd, which has been corrected by having minimum load set at zero. The minimum load is calculated based on a fracture probability of 0.135% when a load is repetitively applied 10 million times (Fig. 3) to a straight-running roller chain having five or more effective links.
*Stainless steel and engineered plastic chains: Maximum allowable load is determined from specifying the surface pressure between pins and bushes based on wear performance.
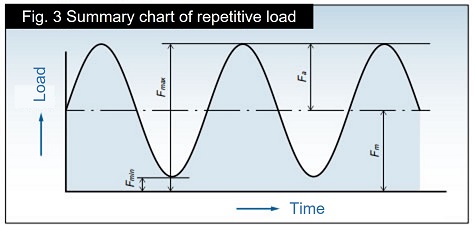
Note that strength of offset links may be lower than the chain itself.
Fd = Fu(Fmax - Fmin) Fu - Fmin
Fu:JIS min. tensile strength
4. Transmission Capacity Table
RS Roller Chain, Super Roller Chain, Heavy Duty Chain, and Low Noise Drive Chain kilowatt ratings tables show kW values for 15,000 hours of operation using a two-shaft drive and 100 pitches of roller chain under conditions 1 to 5 below.
- 1) The chains are operated under ordinary conditions where the ambient temperature is -10℃ to 60℃ (14°F to 140°F) and there is no abrasive dust.
- 2) There are no negative effects from corrosive gasses or high humidity.
- 3) The two drive shafts are level and the chain is installed in the proper position.
- 4) There is minimal load variation during transmission.
- 5) The recommended lubrication system and lubricant shown in the kW ratings tables is used for RS Roller Chain, Super Roller Chain, Heavy Duty Chain, and Low Noise Drive Chain.
5. Moment of Inertia
Moment of inertia is used to show the degree of inertia in rotational movement; in other words, “rotation difficulty” or “rotation ease.”
This is equivalent to the mass (weight) of the object being used for straight-line transmission.
Moment of inertia is shown in the SI units table as: I = MK2(kg・m2 M : mass of rotating body K:turning radius)
It is shown in the gravimetric units table as: I = G・K2 G (kgf・m・S2 G : mass of rotating body G : gravitational acceleration)
Although, GD2 = 4G I (D : diameter of rotating body) is generally being used now in place of moment of inertia.
6. Total length tolerance of roller chain
Length test method and length tolerance are specified in JIS B 1801-2014.
The length tolerance of any individual size when subjected to a measured load (e.g. 500 N [50.99 kgf] for RS 80-1) specified in JIS is 0 to +0.15% of the reference length.
The reference length is calculated by multiplying the reference pitch (P) by the number of links. (Applicable to products bearing a JIS identification number. )
7. Elastic elongation of chain under load
An elastic elongation curve of a chain under load looks as shown below. Values shown here are the standard references for single-strand RS Roller Chains.
Do not apply loads greater than the maximum allowable load to roller chains.
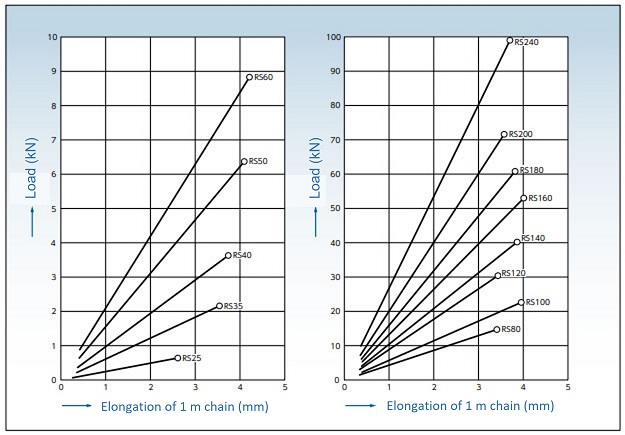