Technical Data Mechanical protectors Handling
Torque Limiter TL Handling
Torque Setting
Set the Torque Limiter slipping torque by tightening the adjustment nuts or bolts.
- (1)After mounting the Torque Limiter onto the equipment, perform several test runs to find the optimal position by gradually tightening the adjustment nuts/bolts. To determine the slipping torque for a given tightening amount of the adjustment nut/bolt, use the Tightening Amount–Torque Correlation Charts below. However, the torque may vary depending on the condition of the friction surfaces and other factors. The chart is a guide only, and the best way to find the correct tightening amount for your machine is to perform a test run with the adjustment nut/bolt slightly loose and then gradually tighten it to find the optimal position. If a stable torque is required, tighten the adjustment nut/bolt by hand until it is fully seated, then tighten an additional 60 degrees with a wrench. Then allow the nut/bolt to slip approximately 500 turns. If the speed is high, divide the 500 turns into several intervals.
- (2)Torque Limiters can be supplied with a center member and pre-set torque, but the shaft bore must be finished.
Tightening Amount–Torque Correlation Charts
Zero point (0) is the state where the adjusting nut or bolts are hand-tightened and the disc springs are fixed.
Center Member Selection and Manufacture
Sprockets and gears can be used as a center member with the Torque Limiter.
If the customer intends to select or manufacture the center members by themselves, take the following precautionary steps.
- (1)The Torque Limiter’s outer diameter (D) limits the minimum diameter of the center member.
When using a sprocket with a chain drive, refer to the sprockets for the center member table below for the minimum number of teeth. - (2)Finish the friction surface of the center member (both sides) to 3S to 6S.
- (3)For the bore diameter of the center member, machine it to 3S to 6S within the center member bore diameter tolerance from the dimensions table.
- (4)The thickness where the center member is inserted should be within the S dimension in the dimensions table.
Torque Limiter Operation Detection
Torque Limiter slips and protects the machine when an overload occurs. However, if the driving source is not stopped, the Torque Limiter will continue to slip, which can cause abnormal wear and excessive heat generation on the friction facings. In such situations, it is essential to shut down the drive source immediately.
A proximity switch and digital tachometer can be used to detect Torque Limiter slippage and stop the drive source. Here are examples of how this method can be implemented:
Mounting Examples
Model 1
When the driven side experiences overload and the Torque Limiter’s center member stops
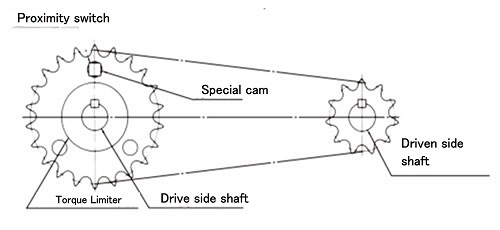
Model 2
When the driven side experiences overload and the Torque Limiter stops
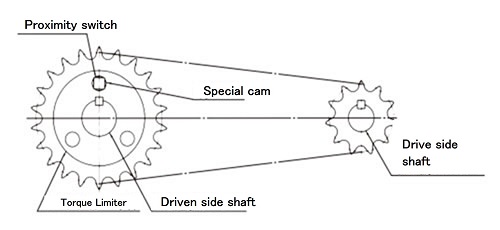
Model 3
When the Torque Limiter is used with a coupling and the center member stops due to an overload
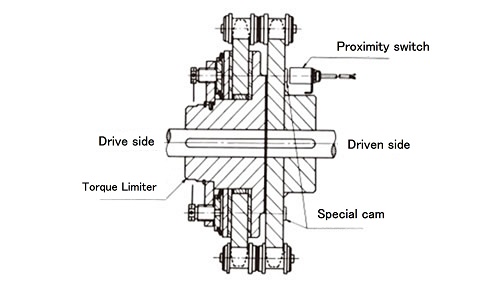
Case 4
When the Torque Limiter is used with a coupling and the Torque Limiter stops due to an overload
Avoid case 4 as much as possible because installing the special cams is difficult. When using the Torque Limiter with a coupling, use case 3.
By selecting the number of special cams as shown in the table below, slips can be detected within approximately 1 to 10 seconds based on the detection rotational speed.
Number of Special Cams and Detection Rotational Speed
Number of special cams | Detection rotational speed range r/min |
---|---|
1 | 6~60 |
2 | 3~30 |
3 | 2~20 |
4 | 1.5~15 |
5 | 1.2~12 |
6 | 1.0~10 |
7 | 0.85~8.5 |
8 | 0.75~7.5 |
9 | 0.67~6.7 |
10 | 0.6~6.0 |
Electrical Schematic Diagram (reference)
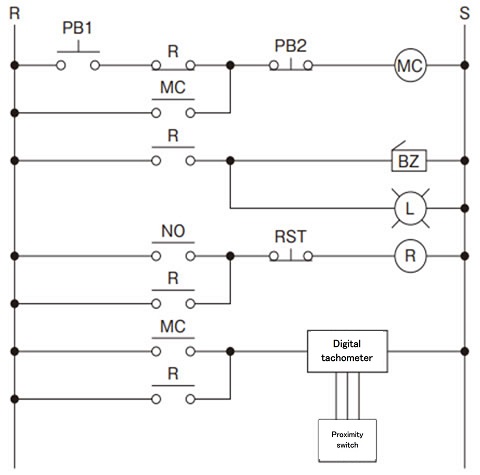
- PB1:Motor start button
- PB2:Motor stop button
- RST:BZ, L reset button
- MC:Electromagnetic contactor for motor
- R:Auxiliary relay
- NO:Digital tachometer output “a” contact
- BZ:Buzzer
- L:Lamp
Digital tachometer :Omron H7CX-R11-N
Proximity switch :Omron TL-N5ME2
Note ) We recommend the above Omron digital tachometers and proximity switches.
For more information, refer to Omron Corporation catalogs.
Special Cam Dimensions and Installation
The special cam is fixed by a screw on the driven side.
Use a screw lock to prevent loosening.
Special Cam Reference Drawing
※Special cam must be prepared by the customer
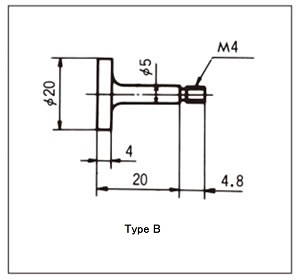
Sprockets for the Center Member
When using the sprocket as a center member, refer to the notes below.
In the table below, the sprocket is used as a center member for the chain drive.
- (1)Minimum number of teeth in which the chain does not interfere with the special cam (as with the reference drawings) when using installation cases 1 and 2.
- (2)Minimum number of teeth in which the chain does not interfere with the friction facings of the Torque Limiter.
- (3)Bushing length
- (4)Sprocket bore diameter (Center member bore diameter )
Model No. | Sprocket bore dia. (Center member bore diameter ) |
Min. number of sprocket teeth | ||||||||||||||||||
---|---|---|---|---|---|---|---|---|---|---|---|---|---|---|---|---|---|---|---|---|
RS35 | RS40 | RS50 | RS60 | RS80 | RS100 | RS120 | RS140 | RS160 | ||||||||||||
Min. number of teeth | Bushing length |
Min. number of teeth | Bushing length |
Min. number of teeth | Bushing length |
Min. number of teeth | Bushing length |
Min. number of teeth | Bushing length |
Min. number of teeth | Bushing length |
Min. number of teeth | Bushing length |
Min. number of teeth | Bushing length |
Min. number of teeth | Bushing length |
|||
TL200 | 30+0.03 0 |
△20 | 3.8 | 16 | 6 | - | - | - | - | - | - | - | - | - | - | - | - | - | - | |
TL250 | 41+0.05 0 |
- | - | 20 | 6.5 | 17 | 6.5 | - | - | - | - | - | - | - | - | - | - | - | - | |
TL350 | 49+0.05 0 |
- | - | 26 | 6.5 | 21 | 6.5 | 18 | 9.5 | 15 | 9.5 | - | - | - | - | - | - | - | - | |
TL500 | 74+0.05 0 |
- | - | - | - | △29 (30) |
6.5 | 25 | 9.5 | 19 | 9.5 | - | - | - | - | - | - | - | - | |
TL700 | 105+0.05 0 |
- | - | - | - | - | - | △33 (35) |
9.5 | 26 | 12.5 | 21 | 12.5 | 18 | 12.5 | - | - | - | - | |
TL10 | 135+0.07 0 |
- | - | - | - | - | - | - | - | - | - | △29 (30) |
12.5 | 24 | 15.5 | △22 | 19.5 | - | - | |
TL14 | 183+0.07 0 |
- | - | - | - | - | - | - | - | - | - | △39 (40) |
15.5 | △33 (35) |
15.5 | △29 | 19.5 | △26 | 23.5 | |
TL20 | 226+0.07 0 |
- | - | - | - | - | - | - | - | - | - | △54 | 15.5 | △46 (60) |
15.5 | △40 | 19.5 | △35 | 23.5 |
- Note) 1. △ denotes non-standard A-type sprocket. When using a standard stock sprocket, use the number of teeth in parenthesis ( ).
- Note) 2. Bush length is for reference.
Model No. | Sprocket bore dia. (Center member bore diameter ) |
Min. number of sprocket teeth | ||||||||||||||||||
---|---|---|---|---|---|---|---|---|---|---|---|---|---|---|---|---|---|---|---|---|
RS35 | RS40 | RS50 | RS60 | RS80 | RS100 | RS120 | RS140 | RS160 | ||||||||||||
Min. number of teeth | Bushing length |
Min. number of teeth | Bushing length |
Min. number of teeth | Bushing length |
Min. number of teeth | Bushing length |
Min. number of teeth | Bushing length |
Min. number of teeth | Bushing length |
Min. number of teeth | Bushing length |
Min. number of teeth | Bushing length |
Min. number of teeth | Bushing length |
|||
TL200 | 30+0.03 0 |
△25 | 3.8 | 19 | 6 | - | - | - | - | - | - | - | - | - | - | - | - | - | - | |
TL250 | 41+0.05 0 |
- | - | 24 | 6.5 | 20 | 6.5 | - | - | - | - | - | - | - | - | - | - | - | - | |
TL350 | 49+0.05 0 |
- | - | 30 | 6.5 | 24 | 6.5 | 21 | 9.5 | 17 | 9.5 | - | - | - | - | - | - | - | - | |
TL500 | 74+0.05 0 |
- | - | - | - | 32 | 6.5 | △28 (30) |
9.5 | 21 | 9.5 | - | - | - | - | - | - | - | - | |
TL700 | 105+0.05  0 |
- | - | - | - | - | - | 36 | 9.5 | △28 (30) |
9.5 | △23 (24) |
12.5 | 20 | 12.5 | - | - | - | - | |
TL10 | 135+0.07  0 |
- | - | - | - | - | - | - | - | - | - | △31 (32) |
12.5 | 26 | 15.5 | △23 | 19.5 | - | - | |
TL14 | 183+0.07  0 |
- | - | - | - | - | - | - | - | - | - | △41 (45) |
15.5 | 35 | 15.5 | △30 | 19.5 | △27 | 23.5 | |
TL20 | 226+0.07  0 |
- | - | - | - | - | - | - | - | - | - | △56 (60) |
15.5 | △47 (60) |
15.5 | △41 | 19.5 | △36 | 23.5 |
- Note) 1. △ denotes non-standard A-type sprocket. When using a standard stock sprocket, use the number of teeth in parenthesis ( ).
- Note) 2. Bush length is for reference.