Technical Data Coupling Sizing and procedure
To view selection procedures and precautions, please proceed to the following.
Click here to narrow down the product series or to make a tentative selection.
If you have specific conditions of use and wish to make a detailed selection, please click here.
ECHT-FLEX Coupling NEF / NEHSeries Selection
1.Correction torque calculation
1-1. When connected to servomotor or stepping motor
To determine the correction torque, multiply the maximum torque of the servomotor or stepping motor by the service factor (SF) corresponding to the type of load listed in the table below.
Load type | Uniform load | Moderately variable load | Highly variable load |
---|---|---|---|
Service factor (SF) | 1.2 | 1.4 | 1.5 |
1-2. When connected to general-purpose motor
To determine the correction torque, multiply the load torque calculated with the following formula by the service factor (SF) corresponding to the type of load listed in the table on the right.
T = 9550 × P n
- T' = T × SF
- T = Load torque N・m
- P = Power transmission kW
- n = Speed r/min
- T' = Correction torque N・m
Load type | Motor type | ||||
---|---|---|---|---|---|
General purpose motor, gas turbine | Engine | ||||
Small moment of inertia | Large moment of inertia | Four cylinders | Six cylinders | Eight cylinders | |
Uniform load | 1.5~1.75 | 1.75~2.0 | 2.5~4.0 | 2.0~2.5 | 1.5~2.0 |
Moderately variable load | 2.0~2.5 | 2.5~3.0 | 4.0~5.0 | 2.5~3.5 | 2.0~3.0 |
Highly variable load | 3.0~4.5 | 4.5~6.0 | 4.5~5.5 | 3.0~4.0 | 2.5~3.5 |
- ※If shock loads will be applied, calculate the correction torque by multiplying the motor’s maximum output torque by a shock factor of 1 to 2.5.
- * When the coupling method is clamp or Power-Lock coupling, prevent startup torque or other torque being applied even instantaneously if it will exceed the bore’s friction transmission torque (see each product pages).
2.Shaft diameter
Check that the shafts to be mounted are within the coupling’s range of mountable shaft diameters.
With the Power-Lock, check the Power-Lock size, quantity and transmission torque.
With the clamp type, make sure that the correction torque determined in Item (1) does not exceed the allowable transmission torque for the clamp.
Strength must be checked when mounting the product on a hollow shaft. Inquire for information.
3.Show model No.s
ECHT-FLEX Couplings satisfying Items 1 to 2 above should be chosen from the transmission capacity table.
Note .Long Spacer Type rotation limits
When long spacer types are used at high speeds, the rotation speed needs to be checked to avoid the resonance point.
When selecting long spacer types, check each model number’s J dimension and whether its rotation speed is within the limit.
Select by increasing the model number if the rotational speed used is over the listed rate.
Model No. | Rotational speed used [r/min] | ||||||||||||||
---|---|---|---|---|---|---|---|---|---|---|---|---|---|---|---|
3600 | 2000 | 1800 | 1500 | 1200 | 1000 | 900 | 750 | 720 | 600 | 500 | 400 | 300 | 200 | 150 | |
NEF04W | 980 | 1310 | 1380 | 1510 | 1680 | 1840 | 1940 | 2130 | 2170 | 2380 | 2610 | 2910 | 3360 | 4120 | 4750 |
NEF10W | 1120 | 1500 | 1580 | 1730 | 1940 | 2120 | 2230 | 2450 | 2500 | 2730 | 2990 | 3350 | 3860 | 4730 | 5460 |
NEF18W | 1180 | 1580 | 1660 | 1820 | 2040 | 2230 | 2350 | 2570 | 2620 | 2870 | 3150 | 3520 | 4060 | 4970 | 5740 |
NEF25W | 1310 | 1760 | 1850 | 2030 | 2260 | 2480 | 2610 | 2860 | 2920 | 3190 | 3500 | 3910 | 4510 | 5520 | |
NEF45W | 1440 | 1930 | 2030 | 2230 | 2490 | 2720 | 2870 | 3140 | 3210 | 3510 | 3840 | 4290 | 4960 | ||
NEF80W | 1560 | 2090 | 2200 | 2410 | 2690 | 2950 | 3100 | 3400 | 3470 | 3800 | 4160 | 4650 | 5360 | ||
NEF130W | 1780 | 3280 | 2510 | 2750 | 3070 | 3360 | 3540 | 3870 | 3950 | 4330 | 4740 | 5290 | |||
NEF210W | 1890 | 2520 | 2660 | 2910 | 3250 | 3560 | 3750 | 4100 | 4190 | 4580 | 5020 | 5610 | |||
NEF340W | 2024 | 2720 | 2870 | 3130 | 3500 | 3830 | 4040 | 4420 | 4510 | 4930 | 5400 | ||||
NEF540W | 2180 | 2910 | 3070 | 3360 | 3750 | 4100 | 4320 | 4730 | 4820 | 5280 | 5780 | ||||
NEF700W | 2270 | 3030 | 3190 | 3490 | 3890 | 4260 | 4490 | 4910 | 5010 | 5490 | |||||
NEH09W | 2190 | 2930 | 3090 | 3380 | 3780 | 4130 | 4360 | 4770 | 4870 | 5330 | 5830 | ||||
NEH14W | 2190 | 2930 | 3090 | 3380 | 3780 | 4130 | 4360 | 4770 | 4870 | 5330 | 5830 | ||||
NEH20W | 2400 | 3200 | 3380 | 3690 | 4130 | 4520 | 4760 | 5210 | 5320 | 5820 | |||||
NEH30W | 2570 | 3430 | 3610 | 3960 | 4420 | 4840 | 5100 | 5580 | 5690 | ||||||
NEH41W | 2650 | 3540 | 3730 | 4080 | 4560 | 4990 | 5260 | 5760 | 5870 |
Long spacer high-speed type
A larger coupling size can be selected as a way to avoid a dangerous RPM range. When use of a larger size is not possible, the same effect can be achieved by increasing the spacer weight. Please contact us.
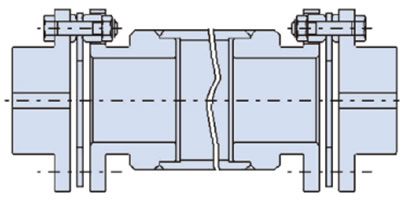
Cautions for servomotor drive
Depending on the natural frequency and electric control status of the system as a whole, a ball screw drive system using a servomotor may generate large vibration or abnormal sound caused by oscillation due to the characteristics of the servomotor.
In this case, adjust the torsional stiffness and moment of inertia of the overall drive system to increase the torsional natural frequency, or adjust the servo gain with the electric control tuning function of the servomotor.
Dynamic balance adjustment
Normally, because ECHT-FLEX couplings provide a well-balanced design, they need no particular balance adjustment. However, when the coupling is used at a high rotation speed, or when a long spacer is used, balance adjustment may be required. In this case, inform us of your desired operating rotation speed, JIS balance rating, dimension “J ”, or spacer length so that we can perform your balance adjustment.
For dynamic balance adjustment, we use the following two methods: 1) Drilling the spacer flange end face, and 2) Mounting a balance weight to the spacer pipe periphery. (The spacer with a balance weight is shown below. The balance weight mounting position and quantity vary depending on operating conditions.
Be careful not to interfere with the balance weight during rotation. )
When requesting a balance adjustment, specify either method 1) or 2) above.

A spacer mounted with a balance weight
Notes for large distance between shaft ends
For large distance between shaft ends, Tsubaki offers a Long Spacer Type that can be used in a floating state without the need for an intermediate shaft bearing. We recommend this type of coupling if it fits your application needs.

Long spacer type
To avoid the ‘skipping rope phenomenon’ when your conditions require use of an intermediate shaft instead of a long spacer, use bearings to fasten intermediate shafts. The spacer type is the recommended disk coupling in this case.

Spacer type + fixed intermediate shaft + Spacer type
If the distance between shafts is short and an intermediate shaft is used in a floating condition, be sure to use the Single-Type coupling.

Single hub + floating intermediate shaft +Single hub
Never use the spacer type with additional floating shaft.

Spacer type + floating intermediate shaft + Spacer type
Pay special attention to the above when replacing gear couplings or roller chain couplings with disk couplings.