Technical Data Small size conveyor chain Selection
Conveyor Design Guidelines
1. Conveyor System and Roller Type
Table 20
Conveyor System | Roller type | Features and Use |
---|---|---|
Chain Rolling (horizontal, inclined ) ![]() Double Pitch Chains |
R-roller Heavy in chain weight Greater allowable roller load Less roller wear |
Smooth operation and vibrations are small. Power required is low since frictional resistance is small. Center distance between sprockets should be generally over 10 m. Applicable for speeds over 20 m/min. |
Chain Rolling
![]() |
S-roller Lightweight Lower allowable roller load |
Center distance between sprockets should be generally 10 m or less. Applicable for speeds 20 m/min or less. |
Chain Sliding ![]() Double Pitch Chains |
Resistant to loading shocks and bad environments; however, the rail is damaged quickly. Construction is simple. Power required is large. |
2. Conveyor Arrangement
Table 21
![]() |
Both the conveying and return sides are supported by rails. The most recommended and streamlined layout. A sag is produced on the take-off side of the sprocket. |
![]() |
The return side is supported by guides, rollers, or idlers. Since the chain bends when it comes into contact with the rollers or guides, friction increases, allowing for easy wear Also, chain vibration exerts a negative effect on overall running. Consequently, it is not desirable to have a long center distance between sprockets. |
![]() |
The return side is not supported. The tension due to the mass of the chain on the return side produces vibrations causing rough conveyance. |
Examples showing slat conveyors and a cross rod conveyor that are most commonly used:
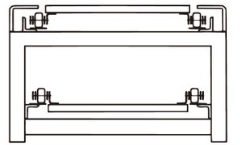
Slats are installed using A attachments, and the rollers roll over the rails on both the conveying and return sides.
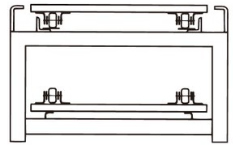
Slats are installed using K attachments. Compared to the above example, this type of arrangement is suitable for wide slat conveyors where the mass of the conveyed goods is heavy.
However, on the return side the slats slide on the rail.
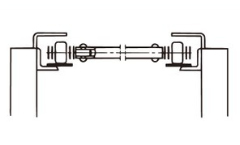
This is a cross rod conveyor where a pipe is installed by means of an EP attachment, GNK attachment, or Hollow Pin Chain. T
The rollers roll on the rails on both the conveying and return sides.
3. Use of Standard Small Size Conveyor Chain at High/Low Temperatures
As a general rule, standard small size conveyor chain can be operated in clean air environments and in ambient temperatures between –10°C and 60°C. When the chain is operated in environments outside this range, the following points should be taken into consideration.
Operation at very low or high temperatures: Chain must be selected or used in a different manner when it is operated in freezing chambers, cold areas, when it passes through dryers or heat-treatment furnaces, or when it is affected by heat from the material being conveyed. Table 22 below provides guidelines for the relationship between allowable load and temperature for standard chains.
Table 22 Temperature Corrected Working Load
Temperature Range ℃ | Allowable load |
---|---|
Down to –30 | Max. allowable load in catalog × 1/4 |
Down to –20 | 〃 × 1/3 |
-10 ~ 150 | 〃 × 1 |
Up to 200 | 〃 × 3/4 |
Up to 250 | 〃 × 1/2 |
Table 23 Temperature Environment and Points of Concern
Temperature Range ℃ | Usage Conditions | Notes |
---|---|---|
-50 ~ -30 | Under –30°C or lower conditions, consider corrosion-resistant SS or AS chain. Standard chains cannot be used. |
(1)Low-temperature embrittlement may occur with standard chain, reducing impact resistance. (2)Congealing of lubricant. (3)Rust due to condensation. (4)Seizure due to frost formation. |
-30 ~ -10 | Standard chain should be selected on the basis of the corrected working load above (Table 22. ) | |
60 ~ 150 | Different lubricant is required. | |
150 ~ 250 | Because wear resistance is reduced in this temperature range, consider selecting the next larger pitch chain size over the one originally selected to reduce bearing pressures. When standard chain is to be used, evaluate whether or not the chain can be used at a reduced allowable load. (Table 22. ) | (1)Excessive wear due to decreased pin and bush hardness. (2)Increased elongation due to softening (3)Insufficient lubrication and chain seizure due to deterioration of lubricant. (4)Excessive wear and chain seizure due to formation of scale. |
250 ~ 400 | Consider corrosion-resistant SS or AS chain. |
4. Lubricants and High/Low Temperatures
Special low-temperature or high-temperature lubricants are required if a chain will be exposed to temperatures outside the range of –10°C to 60°C. See here for details on recommended lubricants.
5. Cautions on Use in Special Environments
Please click here.
6. Other Precautions
- (1)To keep long conveyors consistently operating in top condition, use take-up devices to eliminate chain slack.
Take-up stroke = (Distance between shafts × 0.02) + Leeway length
0.02:2% allowable wear elongation of chain - (2)Chain must always be engaged with at least three sprocket teeth.
- (3)When operating with multiple strands of conveyor chain, sprockets should be mounted on the same shaft and all sprocket teeth should be properly aligned.
- (4)When operating a long conveyor with two or more strands of chain, and when especially high pitch accuracy is required, Tsubaki can provide specially configured chain to minimize the relative difference in length. Also, special sprockets can be manufactured to ensure that sprocket teeth are properly aligned.
7. Corrosion Resistance Guide for CorrosionResistant Chains and Sprockets
Please click here.