Technical Data Small size conveyor chain Selection
To view selection procedures and precautions, please proceed to the following.
Click here to narrow down the product series or to make a tentative selection.
If you have specific conditions of use and wish to make a detailed selection, please click here.
Selection Procedure for Small Size Conveyor Chains
An appropriate chain size and type can be selected based upon the type and capacity of the conveyor. In some cases, it may be difficult to determine the most appropriate chain size and type, since there are a variety of operating conditions for the conveyor. The general procedure for chain selection is as follows:
1. Check Conveyance Conditions

2. Tentatively Determine Chain Type

3. Check Allowable Load of Rollers and Attachments

4. Calculate Maximum Chain Load

5. Determine Chain Size

6. How to Select Chain for Indexing Drive
Steps 1. Check Conveyance Conditions
- 1. Type of conveyor (slat conveyor, bucket elevator, etc. )
- 2. Direction of chain travel (horizontal, inclined, or vertical conveyor )
- 3. Type, mass, and size of materials to be conveyed
- 4. Conveyor capacity, interval between conveyed objects
- 5. Conveying speed
- 6. Conveyor length
- 7. Lubrication status
- 8. Considerations for special environments (high/low temperature, presence of corrosive substances )
Steps 2. Tentatively Determine Chain Type
Use the following formula to determine maximum static chain load (F) for tentative selection of chain type.
SI Unit F(kN) = W × f1 × KV × G 1000
Gravity unit F{kgf} = W × f1 × KV
W = Total mass {weight} of conveyed objects on conveyor {Weight } kg{kgf}
f1 = Coefficient of friction (Table 3) KV = Speed coefficient (Table 4)
G = 9.80665m/s2
Tentatively select a chain that has maximum allowable load of F (for two parallel strands, use F X 0.6) or more.
The maximum allowable load of small size conveyor chain (excluding stainless steel chain and engineering plastic chain*) is the value derived from the lowest fatigue limit.
When a load lower than this value is repetitively applied to the chain, fatigue failure will never occur.
※Stainless steel and engineered plastic chains: Maximum allowable load is determined from specifying the surface pressure between pins and bushes based on wear performance.
Steps 3. Check Allowable Load
The load applied to rollers or attachments should not exceed the allowable loads shown in Table 1 and Table 2.
Table 1 Base Chain Allowable Roller Load
Size | Double Pitch Chains RS Attachment (Standard) Lambda ・X-Lambda |
Stainless steel roller (SS, AS) |
Plastic roller | KV Series Plastic Roller | Low Noise Plastic Roller | Poly Steel Chain | |||
---|---|---|---|---|---|---|---|---|---|
R-roller | S-roller | R-roller | S-roller | R-roller | S-roller | R-roller | R-roller | ||
RS25 | - | - | - | - | - | - | - | - | 0.005 {0.5} |
RS35 | - | - | - | - | - | - | - | - | 0.015 {1.5} |
RF2040・RS40 | 0.64 {65} | 0.15 {15} | 0.20 {20} | 0.05 {5} | 0.20 {20} | 0.02 {2} | 0.20 {20} | 0.14 {14} | 0.02 {2.0} |
RF2050・RS50 | 0.98 {100} | 0.20 {20} | 0.29 {30} | 0.06 {6} | 0.29 {30} | 0.03 {3} | 0.29 {30} | 0.21 {21} | 0.04 {4.0} |
RF2060・RS60 | 1.57 {160} | 0.29 {30} | 0.49 {50} | 0.09 {9} | 0.49 {50} | 0.05 {5} | 0.49 {50} | 0.34 {35} | 0.06 {6.0} |
RF2080・RS80 | 2.65 {270} | 0.54 {55} | 0.78 {80} | 0.15 {15} | 0.88 {90} | 0.09 {9} | - | 0.62 {63} | - |
RF2100・RS100 | 3.92 {400} | 0.78 {80} | 1.18 {120} | 0.25 {25} | 1.27 {130} | - | - | - | - |
RF2120・RS120 | 5.88 {600} | 1.18 {120} | 1.77 {180} | 0.34 {35} | - | - | - | - | - |
RS140 | - | 1.32 {135} | - | 0.39 {40} | - | - | - | - | - |
RF2160・RS160 | 9.61 {980} | 1.91 {195} | 2.75 {280} | 0.54 {55} | - | - | - | - | - |
Note)
- 1. Values are for lubricated chain. Values for Double Pitch and RS Attachment Chain include corrosion-resistant chains (NP/NEP series).
- 2. The above values for Poly Steel Chain represent the allowable load for each plastic inner link.
- 3. The material used for standard R roller guide rail should be a high tensile strength material at least S45C (JIS), 1045 (AISI) or better.
- 4. See product page for details on Bearing Cage Chain and Bearing Bush Chain.
Base Chain Allowable Roller Load
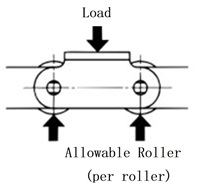
Table 2 Allowable load of A attachments
Vertical load that an “A” attachment can accept.
Depending on the shape and structure of attachments to be installed by the customer, force may be generated that will cause A attachments to twist. Contact a Tsubaki representative if you have any concerns.
Double Pitch Chains | RS Chain | ||||
---|---|---|---|---|---|
Size | Double Pitch Chains Note 1 | Stainless | Size | with attachment Note 1 | Stainless |
RF2040 | 0.262 {26.7} | 0.108 {11.0} | RS25 | 0.028 {2.9} | 0.012 {1.2} |
RF2050 | 0.455 {46.4} | 0.189 {19.3} | RS35 | 0.094 {9.6} | 0.036 {3.7} |
RF2060 | 1.06 {108} | 0.419 {42.7} | RS40 | 0.130 {13.3} | 0.054 {5.5} |
RF2080 | 1.67 {170} | 0.646 {65.9} | RS50 | 0.243 {24.8} | 0.101 {10.3} |
RF2100 | 2.51 {256} | 1.15 {117} | RS60 | 0.376 {38.3} | 0.148 {15.1} |
RF2120 | 3.68 {375} | 1.79 {183} | RS80 | 0.591 {60.3} | 0.233 {23.8} |
RF2160 | 5.84 {596} | 3.13 {319} | RS100 | 0.933 {95.1} | 0.361 {36.8} |
RS120 | 1.39 {142} | 0.629 {64.1} | |||
RS140 | 1.82 {186} | 0.869 {88.6} | |||
RS160 | 2.36 {241} | 1.19 {121} |
Note)
- 1. Includes corrosion-resistant chain (NP/NEP series).
- 2. See product page for details on Bearing Cage Chain and Bearing Bush Chain.
- ・The attachment hole of an A attachment is the point where the allowable vertical load acts on the attachment.
- ・K attachments have double the values shown for A attachments.
- ・Load should not exceed maximum allowable roller load.
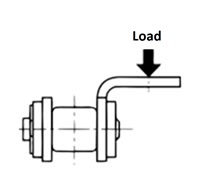
Steps 4. Calculate Max. Chain Load (F)
In this catalog, values are indicated in both SI and gravimetric units. The weight (kgf) used to calculate the max. load in the gravimetric units is the same value as the mass (kg).
- F = Maximum static load on chain :kN{kgf}
- V = Conveying speed (Chain speed ):m/min
- H = Center distance between sprockets (vertical direction ):m
- L = Center distance between sprockets (horizontal direction ):m
- C = Center distance between sprockets :m
- M = Mass {weight} of moving parts {Weight }:chain※, bucket, apron, etc. {Weight }:kg/m{kgf/m}
- W = Total mass {weight} of conveyed objects on conveyor (max. value) :kg{kgf}
For countable items :W = C Loading interval × Weight of conveyed goods {Weight } - kW = Power required
- f1 = Coefficient of friction between chain and guide rail (Table 3)
- η = Transmission efficiency of drive unit
- G = Gravitational acceleration :9.80665m/s2
※When two chains are used in parallel, the mass of the chain is the weight of two strands.
※If frequent forward and reverse operation is required, take-up is necessary to remove chain slack, so the calculation differs from the below.
When removing slack in a chain by take-up, please use the calculation formula in Q&A6.
Table 3-1 f1:Coefficient of Friction of Base Chain Rollers Rolling on Rail
Roller Type | Steel roller | Lambda chain | Plastic roller Note | Low Noise Plastic Roller | Bearing Bush Chains | |
---|---|---|---|---|---|---|
No lube | With lube | No lube | No lube | |||
R-roller | 0.12 | 0.08 | 0.08 | 0.08 | 0.1 | 0.21 |
S-roller | 0.21 | 0.14 | 0.14 | - | - | - |
Note) The plastic roller includes heat-resistant type rollers (KV type).
Table 3-2 f1:Coefficient of Friction of Base Chain Plates Sliding on Rail
Steel Plate | Poly Steel Chain | |
---|---|---|
No lube | With lube | |
0.3 | 0.2 | 0.25 |
Formulae
SI Unit | {Gravity unit } |
---|---|
Horizontal conveyance Goods are directly loaded on the conveyor F = (W + 2.1 × M × C) × f1 × G 1000 kW = F × V 6120 × 1 η ![]() F = (W + 2.1 × M × C) × f1 kW = F × V 6120 × 1 η |
|
Vertical conveyance F = (W + M × C) × G 1000 kW = W × V 60 × G 1000 × 1 η ![]() F = W + M × C kW = W × V 6120 × 1 η |
|
Inclined conveyance ※ Goods are directly loaded on the conveyor ![]() F = (W + M × C) L × f1 + H C + 1.1 × M × (L × f1 - H) × G 1000 kW = V 60 F - M × (H - L × f1) G 1000 × 1 η F = (W + M × C) L × f1 + H C + 1.1 × M × (L × f1 - H) kW = V 6120 F - M × (H - L × f1) × 1 η Note) When calculating the value for F, if L x f1–H<0, make L x f1–H=0. Also when calculating the value for kW, if H–L x f1<0, make H–L x f1=0. |
|
Horizontal, inclined conveyance ※ Goods are directly loaded on the conveyor ![]() F =
(
W
C1 + C2
+ 2.1 × M) C1 × f1+
(
W
C1 + C2
+ M) × (L1 × f1 + H)
kW = V 60 F - M × (H - L1 × f1) G 1000 × 1 η F =
(
W
C1 + C2
+ 2.1 × M) × C1 × f1+
(
W
C1 + C2
+ M) × (L1 × f1 + H)
kW = V 6120 F - M × (H - L1 × f1) × 1 η Note) When calculating the value for F, if L1 x f1–H<0, make L1 x f1–H=0. Also when calculating the value for kW, if H–L1 x f1<0, make H–L1 x f1=0. |
Steps 5. Determine Chain Size
Multiply the maximum load (F) applied to a chain by the speed coefficient (KV) given in Table 4 for a chain that satisfies the following formula:
F × KV ≦ Maximum allowable load of the chain
Table 4 Speed coefficient (KV)
Chain speed m/min | Speed coefficient (Kv) |
---|---|
15 or less | 1.0 |
15~30 | 1.2 |
30~50 | 1.4 |
50~70 | 1.6 |
70~90 | 2.2 |
90~110 | 2.8 |
110~120 | 3.2 |
The recommended speed of the following chains is as follows :
|
Less than 30m/min |
|
70 m/min or less |
Table 5 Small Size Conveyor Chain Strength (Units :kN{kgf})
Size | general use chain | Lambda chain Long life Lambda chain |
---|---|---|
RF2040 | 2.65 {270} | 2.65 {270} |
RF2050 | 4.31 {440} | 4.31 {440} |
RF2060 | 6.28 {640} | 6.28 {640} |
RF2080 | 10.7 {1090} | 10.7 {1090} |
RF2100 | 17.1 {1740} | 17.1 {1740} |
RF2120 | 23.9 {2440} | 23.9 {2440} |
RF2160 | 40.9 {4170} | - |
Size | Stainless Steel Double Pitch Chain | Surface Treated Double Pitch Chain | |||||
---|---|---|---|---|---|---|---|
SS Series | HS Series | AS Series | NS Series | LSK Series | NP Series | NEP Series | |
RF2040 | 0.69 {70} | 1.19 {121} | 0.69 {70} | 0.44 {45} | 0.44 {45} | 2.65 {270} | 2.65 {270} |
RF2050 | 1.03 {105} | 1.85 {189} | 1.03 {105} | 0.69 {70} | 0.69 {70} | 4.31 {440} | 4.31 {440} |
RF2060 | 1.57 {160} | 2.78 {283} | 1.57 {160} | 1.03 {105} | 1.03 {105} | 6.28 {640} | 6.28 {640} |
RF2080 | 2.65 {270} | 4.77 {486} | 2.65 {270} | 1.77 {180} | - | 10.7 {1090} | 10.7 {1090} |
RF2100 | 2.55 {260} | - | - | - | - | 17.1 {1740} | 17.1 {1740} |
RF2120 | 3.82 {390} | - | - | - | - | 23.9 {2440} | - |
RF2160 | 6.37 {650} | - | - | - | - | 40.9 {4170} | - |
Size | General Use Series | Low Noise Series | Heat-resistant package | |||||
---|---|---|---|---|---|---|---|---|
Standard Series | NP Series | SS Series | SP Roller | Standard Series | NP Series | SS Series | ||
RF2040 | 0.44 {45} | 0.44 {45} | 0.44 {45} | 0.23 {23} | 0.44 {45} | 0.44 {45} | 0.44 {45} | 0.44 {45} |
RF2050 | 0.69 {70} | 0.69 {70} | 0.69 {70} | 0.34 {34} | 0.69 {70} | 0.69 {70} | 0.69 {70} | 0.69 {70} |
RF2060 | 1.03 {105} | 1.03 {105} | 1.03 {105} | 0.54 {55} | 1.03 {105} | 1.03 {105} | 1.03 {105} | 1.03 {105} |
RF2080 | 1.77 {180} | 1.77 {180} | 1.77 {180} | 0.88 {89} | 1.77 {180} | 1.77 {180} | 1.77 {180} | - |
RF2100 | 2.55 {260} | 2.55 {260} | 2.55 {260} | - | - | - | - | - |
Size | Standard | LMC Series | NP Series | SS Series |
---|---|---|---|---|
RF2040 | 1.77 {180} | 1.47 {150} | 1.77 {180} | 0.44 {45} |
RF2050 | 3.14 {320} | 2.55 {260} | 3.14 {320} | 0.69 {70} |
RF2060 | 4.22 {430} | 3.43 {350} | 4.22 {430} | 1.03 {105} |
RF2080 | 7.65 {780} | 6.18 {630} | 7.65 {780} | 1.77 {180} |
Size | Standard |
---|---|
RF2040 | 1.86 {190} |
RF2050 | 2.84 {290} |
RF2060 | 4.02 {410} |
RF2080 | 6.96 {710} |
Indexing conveyor chain
Size | Standard Series | High Precision Series | Stainless Steel Package |
---|---|---|---|
RF2040 | 0.78 {80} | 0.78 {80} | 0.44 {45} |
RF2050 | 1.27 {130} | 1.27 {130} | 0.69 {70} |
RF2060 | 1.77 {180} | 1.77 {180} | 1.03 {105} |
RF2080 | 2.94 {300} | 2.94 {300} | 1.77 {180} |
Size | Max. allowable load |
---|---|
RF2040 | 0.45 {45} |
RF2050 | 0.69 {70} |
RF2060 | 1.03 {105} |
RF2080 | 1.77 {180} |
Size | Max. allowable load |
---|---|
BCM12.5-9 | 0.3 {30} |
BCM15-9 | 0.3 {30} |
Size | Max. allowable load |
---|---|
BC050 | 0.49 {50} |
BC075 | 0.69 {70} |
BC100 | 0.69 {70} |
BC150 | 1.27 {130} |
Size | general use chain | Lambda chain | Long life Lambda chain |
---|---|---|---|
RS25 | 0.64 {65} | - | - |
RS35 | 1.52 {155} | 1.52 {155} | - |
RS40 | 2.65 {270} | 2.65 {270} | 2.65 {270} |
RS50 | 4.31 {440} | 4.31 {440} | 4.31 {440} |
RS60 | 6.28 {640} | 6.28 {640} | 6.28 {640} |
RS80 | 10.7 {1090} | 10.7 {1090} | 10.7 {1090} |
RS100 | 17.1 {1740} | 17.1 {1740} | 17.1 {1740} |
RS120 | 23.9 {2440} | 23.9 {2440} | - |
RS140 | 32.4 {3300} | 32.4 {3300} | - |
RS160 | 40.9 {4170} | - | - |
Size | RS Chain with stainless steel attachments | RS Chain with surface treated attachments | Poly Steel Chain | Plastic roller Chain |
|||||
---|---|---|---|---|---|---|---|---|---|
SS Series | HS Series | AS Series | NS Series | LSK Series (Stainless steel roller ) |
NP Series | NEP Series | SP Roller | ||
RS25 | 0.12 {12} | - | - | 0.12 {12} | - | 0.64 {65} | - | 0.08 {8} | - |
RS35 | 0.26 {27} | - | - | 0.26 {27} | - | 1.52 {155} | - | 0.18 {18} | - |
RS40 | 0.69 {70} | 1.19 {121} | 0.69 {70} | 0.44 {45} | 0.44 {045} | 2.65 {270} | 2.65 {270} | 0.44 {45} | 0.23 {23} |
RS50 | 1.03 {105} | 1.85 {189} | 1.03 {105} | 0.69 {70} | 0.69 {070} | 4.31 {440} | 4.31 {440} | 0.69 {70} | 0.34 {34} |
RS60 | 1.57 {160} | 2.78 {283} | 1.57 {160} | 1.03 {105} | 1.03 {105} | 6.28 {640} | 6.28 {640} | 0.88 {90} | 0.54 {55} |
RS80 | 2.65 {270} | 4.77 {486} | 2.65 {270} | 1.77 {180} | - | 10.7 {1090} | 10.7 {1090} | - | 0.88 {89} |
RS100 | 3.82 {390} | - | - | - | - | 17.1 {1740} | 17.1 {1740} | - | - |
RS120 | 3.82 {390} | - | - | - | - | 23.9 {2440} | - | - | - |
RS140 | 4.61 {470} | - | - | - | - | 32.4 {3300} | - | - | - |
RS160 | 6.37 {650} | - | - | - | - | 40.9 {4170} | - | - | - |
Size | Standard | Lambda Series | NP Series | SS Series |
---|---|---|---|---|
RS40 | 1.77 {180} | 1.47 {150} | 1.77 {180} | 0.44 {45} |
RS50 | 3.14 {320} | 2.55 {260} | 3.14 {320} | 0.69 {70} |
RS60 | 4.22 {430} | 3.43 {350} | 4.22 {430} | 1.03 {105} |
RS80 | 7.65 {780} | 6.18 {630} | 7.65 {780} | 1.77 {180} |
Size | Standard |
---|---|
RS40 | 1.86 {190} |
RS50 | 2.84 {290} |
RS60 | 4.02 {410} |
RS80 | 6.96 {710} |
Note)
- 1. SS and NS chains are not pre-lubricated before shipping. Always lubricate the chain before use, except when using underwater or when the chain will contact water.
- 2. Using a chain without lubrication may result in premature articulation problems.
- 3. Maximum allowable loads are based on lubricated (including water lubricated) conditions.
Steps 6. How to Select Chain for Indexing Drive
When selecting chain for indexing operations using indexing equipment, in addition to the normal load based on F (load from frictional force), the added load from inertia (F1) must be taken into account when calculating the total load acting on the chain.
In general, this additional load F1 is found from the formula F1 = mα. The steps to calculate chain load based on this formula are explained below.
- m = Total mass on driven side (kg)
- α = Maximum acceleration (m/s2)
SI Unit | {Gravity unit } | ||||||||
---|---|---|---|---|---|---|---|---|---|
![]() |
|||||||||
1) Find total mass “m” on driven side. m = W + M1 + 1 2 M2 Note) 1 2 M2:is an approximate calculated value for the inertial force of the sprocket converted to the mass (weight) of the chain. |
|||||||||
2) Find the additional load from inertia from F1 = mα based on the maximum acceleration α (m/s2) and the formula in 1) above. For example, when using a cam indexing system, maximum acceleration α can be found by using the following formula:
Use the value for Am corresponding to the cam curve.
For details, check with the manufacturer of the indexing equipment. |
|||||||||
3) Find FΣ, the total working load taking the additional tension due to inertia into consideration. FΣ = F + F1/1000 F:Chain load based on frictional force (kN) 3) Find FΣ, the total working load taking the additional tension due to inertia into consideration. FΣ = F + F1/G F:Chain load based on frictional force (kN) G:Gravitational acceleration 9.80665(m/s2) |
|||||||||
4) Determine Chain Size FΣKv ≦ Maximum allowable load of the chain Kv:Speed coefficient (Table 4) |
|||||||||
5) Check the allowable roller load of the chain. ×
(Drag to move. )
Typical value that will not cause roller rotational failure, assuming use under lubricated conditions. |